Training needs to be continuous to be effective. When delivering training, too many businesses sign people up for a seminar, or provide an annual online module to complete, and assume they’ve done their job. According to Safety Works!, a program from the Maine Department of Labor, training needs to take place at several junctures during an individual’s employment:
- New employees and those changing jobs should receive a safety briefing and overview of standard safety policies and procedures.
- All employees should receive ongoing training in the hazards and safety protocols related to their specific jobs.
- Retraining should occur when changing jobs, when an employee has been away from work for an extended time, when safety incidents occur, and when new equipment or procedures are introduced.
- As required by industry or federal standards.
To truly lower risk, safety training should be relevant to the job, and workers should have an opportunity to practice and demonstrate their new skills. Lessons should be sequential, matching the order in which employees perform tasks on the job. Training should also be hands-on, giving workers a chance to perform tasks and engage in discussion, both with instructors and with one another. In other words, while watching videos, completing self-paced online courses, and listening to lectures can be a part of the overall safety program, to be truly effective, training should be dynamic and engaging and focused on real-world skills and actions.
When training sessions are over, businesses should ask workers for their feedback to see if they felt the activities were relevant to what they do. Incorporating employee feedback is crucial to making ongoing improvements to training quality. If workers say the training was ineffective—for example, too much classroom lecture and not enough on-the-job activity—then instructors should change the way they design each course so that workers get maximum value from the training.
ONGOING PRIORITY
Teaching one safety class and assuming workers have all the training they need is a risky proposition. Managers and other leaders should follow up with department heads, foremen and other supervisors to see whether workers are implementing the training they’ve received. If a worker performs a task in an unsafe manner, coaching or retraining should happen immediately. In-the-moment assistance is far more effective than assistance after an injury has occurred.
In fact, supporting a culture of safety means that workers must take ownership of occupational safety and health within their work areas. After all, their lives at stake. Involving employees in the development of safety and health policies and training increases engagement. It also ensures that their training is relevant and addresses the most common issues in that specific work environment. Some businesses form safety committees on sites or within plants, committees run by workers and not by managers. They become resources for their colleagues when it comes to safety issues, and they can also report issues, like poor equipment function, before those issues lead to injuries. Because they’re closest to the actual work, they become valuable eyes and ears when it comes to safety issues.
Giving employees ownership over the health and safety of the work environment also means demanding accountability as well. Safety responsibilities should be a part of every job description, with adherence to safety policies and practices a part of performance reviews. When employees engage in unsafe practices or behaviors, they should be disciplined and retrained if necessary.
By the same token, employees who demonstrate commitment to safety and actively support safety goals should be rewarded. Track key performance indicators related to occupational safety and health, such as injury rates, lost time for injury and illness, and severity of workplaces injuries or illnesses associated with work activities, and communicate the results to the entire staff. Facilities or departments that make notable improvements should receive incentives or awards, including individual recognition for leaders and top performers. If goals aren’t being reached, investigate the causes and look for employee input into issues and changes that can be made to achieve those goals.
SAFETY TRAINING
To support a culture of employee safety and prepare your workers to do their jobs safely, keep the following dos and don’ts in mind:
Do:
- Review OSHA requirements for your business, and implement required safety protocols.
- Analyze the work environment to identify safety risks and develop plans to address risks.
- Set safety-related goals.
- Invest in ongoing safety training programs that address workplace-specific risks, best practices and trends.
- Retrain employees as required.
- Involve employees in safety planning and training to keep them engaged.
- Hold employees accountable for safety.
- Recognize employees who go above and beyond to support a safe workplace.
- Implement a specific injury or illness protocol and a system for reporting incidents.
Don’t:
- Rely on a single training session to adequately prepare employees for safety excellence.
- Put off correction or retraining. Immediate action is most effective for changing behavior.
- Accept the minimum in terms of training, safety equipment and protocols.
- Ignore employee input or concerns.
- Forget to document all information related to safety, including training, injury statistics and corrective actions.
- Allow retaliation for the reporting of safety concerns or accidents.
CLOSING THOUGHT
Many businesses discover, like Alcoa did, that the quest to improve safety leads to better production outcomes and lower costs related to injury and illness. But most importantly, a safety focus communicates something important to workers: It shows their employers value their health and well-being.
For More Information:
This article was originally published by Columbia Southern University on The Link. Columbia Southern University offers associate, bachelor’s and master’s degree programs in occupational safety and health, as well as a bachelor’s in environmental management. CSU’s online bachelor’s and master’s programs in occupational safety and health are touted by the Board of Certified Safety Professionals as Graduate Safety Practitionerˇ Qualified Academic Programs. For more, visit columbiasouthern.edu/osh.
Modern Contractor Solutions, November 2022
Did you enjoy this article?
Subscribe to the FREE Digital Edition of Modern Contractor Solutions magazine.
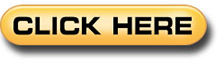