Long-lasting, durable surfaces result from quality compaction
By Jeff Winke
It has been more than a few years since the term and method of “intelligent compaction” (IC) has become a given in discusions of paving. Today, it has become the norm—compaction is pretty much considered intelligent compaction.
NO MORE GUESSING
Here is a simple dictionary type definition: IC refers to the compaction of road materials, such as soils, aggregate bases, or asphalt pavement materials, using modern vibratory rollers equipped with an integrated measurement system, an onboard computer reporting system, Global Positioning System (GPS) based mapping, and optional feedback control. IC rollers facilitate real-time compaction monitoring and timely adjustments to the compaction process by integrating measurement, documentation, and control systems. IC rollers also maintain a continuous record of color-coded plots, allowing the user to view plots of the precise location of the roller, the number of roller passes, and material stiffness measurements.
“Operators have told me that intelligent compaction takes the guessing game out of their rolling pattern,” says Daniel F. Brown, president of Phend & Brown, Inc., Milford, Indiana. “They no longer need to remember which utility power pole or mailbox they started or stopped at with their rolling pattern. Additionally, uniform pass coverage is assured because pass coverage is being measured and documented.”
RESEARCH PROJECT RESULTS
Back in 2011, the FHA reported on a major 3-year research project which was designed to verify that IC, which at the time had been considered “emerging technology,” was mature enough to be implemented in the real world. The intent of the project was to create the blueprint in the FHWA IC strategic plan. This study was under the Transportation Pooled Fund project, which included 12 participating state department of transportation: Georgia, Indiana, Kansas, Maryland, Minnesota, Mississippi, New York, North Dakota, Pennsylvania, Texas, Virginia, and Wisconsin.
The report’s Executive Summary states that the project “demonstrated tried-and-true Intelligent Compaction (IC) technologies through 16 field projects and open house activities, numerous meetings and training for State personnel and local earthwork/paving contractors, and assistance on the development of State IC specifications.”
The IC project’s key conclusions:
- IC mapping of existing support layers is effective in identifying weak support areas for corrective actions prior to the compaction of the upper layers.
- With HMA paving, IC tracking compaction roller passes and HMA surface temperatures can provide the necessary means to maintain a consistent rolling pattern within optimal ranges of temperatures for coverage of 100 percent of the construction area.
- IC technologies can be especially beneficial to maintain consistent rolling patterns under lower visibility conditions, such as night paving operations.
- IC technology, the report states, will have profound influence on the responsibilities of various stages of pavement constructions and will eventually help produce better and more consistent pavement products.
“We are currently running Topcon C-53 IC Systems acquired through the Topcon Solutions Store on two Caterpillar CB-534 D XW rollers, and two systems on Bomag BW190 AD rollers,” states Brown. “At the time of purchase, the C-53, which offers the GX-55 control box, was the newest technology available.
“We like that the technology provides for remote mobile access via Sitelink to allow process balance decisions to be based on real-time data for the entire paver/roller operation, which in turn ensures that optimal production rates and density values are consistently achieved.”
TRACKING FOR PERFORMANCE
Topcon Positioning Systems offers an intelligent compaction system that is designed to track pass counts of multiple rollers or IC machines working on the same project. Through secure connectivity to Topcon’s global Sitelink3D service, each compactor not only performs its tasks, but also becomes part of the overall monitored project.
“Each operator is not only able to see their own passes, but those made by other machines on-screen in real time,” Brown says. “And in real time, the paving superintendant, foreman, and general contractor personnel can also see what exactly is going on via the Sitelink platform. This ensures proper compaction from each machine and eliminates redundancy.”
ESSENTIAL FOR BIG JOBS
“We’re using the Topcon C-53 IC System with a GX-75 control box on our 850 Series Sakai oscillation/vibration paving roller, which allows the machine operator to monitor the compaction pattern and the temperature as they’re working,” states Sergio Muniz, paving superintendent with Payne & Dolan, Inc., Waukesha, Wisconsin. “I like that I can jump onto my laptop and see the work being completed in real time and make certain we’re complying with the tough DOT state specifications.”
Muniz adds: “We’re finding the Topcon system to be essential for our high-profile big jobs to ensure we remain on task and is instrumental for when we work at night. It also is proving handy for smaller parking-lot-type jobs as well.”
CLOSING THOUGHT
The key benefit of IC is greater control over the compaction results, which in turn provides better finished paved results. Compaction at its most elemental is the exertion of force on something so that it becomes more dense, while Intelligent Compaction provides the technological means to ensure that compaction is performed consistently, thoroughly, and accurately. The goal is to achieve optimum densities that ensure adequate support, stability, and strength. Achieving these densities uniformly is key, and clearly IC aids this process.
About the author:
Jeff Winke is a business and construction writer based in Milwaukee, Wisconsin. He can be reached through jeff_winke@yahoo.com.
Modern Contractor Solutions, February 2020
Did you enjoy this article?
Subscribe to the FREE Digital Edition of Modern Contractor Solutions magazine.
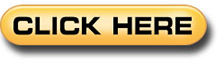