By Danielle Waltz & Alexis Hailpern
We live in an age of innovation where change in our environment creates change in technology and materials. While three specific materials seem to be a constant in construction—concrete, aluminum and brick—they are not immune to innovation. All three materials are going through an innovative process fueled the potential concern of the environmental impact of building materials.
Construction attorneys and in-house counsel need to take note of innovation and new building materials. Understanding the products that are coming into the construction world will only benefit legal construction teams as, inevitably, new products become new legal issues. Having a baseline for innovative products prior to legal issues arising is beneficial to both the advocate and the client in terms of time, cost, and general knowledge.
CONCRETE
Concrete, commonly used for foundation and many facets of superstructure construction, is generally poured on site or delivered pre-cast. The use of concrete comes with reinforcing and strength requirements based on structure size and the climate where the structure will exist.
Innovation: Self-Healing Concrete:
Self-healing concrete is mixed with water-activated bacteria or capsules and fibers containing adhesive liquids to allow self-healing when it cracks, producing calcite to aid the process. Calcite is a carbonate, the mineral component in limestone—another widely used construction material.
Self-healing concrete has many advantages both for the environment and for the cost of construction. Self-healing concrete has a long-life span, a relatively low cost, and reduces infrastructure maintenance. Additionally, being more eco-friendly, self-healing concrete cuts greenhouse gases sometimes present with traditional concrete, creating more sustainable development.
Light-Emitting Concrete:
Developed by Dr. Jose Carlos Rubio from the Michoacan University of Saint Nicholas of Hidalgo in Mexico, light-emitting concrete is a wonder and a beauty. Light-emitting concrete emits soft light at night (without the use of electricity) through a polycondensation process wherein a chemical reaction between the raw materials contained in the concrete (sand, silica, industrial waste, alkali, and water) produces a strong, gel-like mixture which emits light. Conventional concrete forms crystal flakes when mixed with water which blocks absorption of solar energy. Dr. Rubio successfully sought out to modify the microstructures of cement to eliminate the crystals.
Light-emitting concrete is “charged” through the day. The translucent gel enables the absorption of solar energy, although not requiring the sun. The gel can recharge during overcast days, and it can also be charged via artificial lighting. Light-emitting concrete will most-likely be applied to roads, lanes, and safety signs. Because it is aesthetically pleasing, another use could be construction décor.
Importantly, light-emitting concrete conserves energy, maintaining longer life span than fluorescents made from plastic. It is also sun-resistant, not decaying via ultraviolet rays. Best of all, light-emitting concrete is produced through recycling industrial waste.
ALUMINUM
The history of aluminum is nearly as fascinating as its current innovation. Before the construction of the Empire State Building, aluminum was an expensive product used by few. During the early 1920s, aluminum went through an electrolysis process rendering it cheaper and easier to produce. Thereafter, 730 tons were used to construct the Empire State Building, and that in and of itself was an innovation. Now recognized as one of the most sustainable and energy-efficient construction materials (generally contains ½ to ¾ of recycled content), aluminum is experiencing a renaissance.
Transparent Aluminum:
Aluminum oxynitride, or ALON, is aluminum that is transparent. Unbelievably, ALON is stronger than steel by three times, four times harder than silica glass, and 85% harder than sapphire. Aluminum becomes a revolutionary ceramic alloy when nitrogen, oxygen, and aluminum are fused in precise measures to create a transparent, strong aluminum product.
ALON can be used for windows and fire-resistant glass window panes. ALON is also used by the military for under water or deep-sea vehicles or domes and for safety glass.
Despite the innovations described above, conventional aluminum comes with advantages. It is corrosion resistant, requires no framework or cure time, and needs minimal maintenance. Aluminum has a high structural strength, is less expensive than steel, yet lighter than steel with an equal strength to steel. Conventional aluminum is the primary building material for LEED certified builds as it is environmentally friendly. While cost prohibitive for common use at this point, ALON has many advantages on top of the advantages that already come with the use of conventional aluminum that may help facilitate its use once the cost problem is solved.
BRICK
Bricks, although timely to lay, are used in construction because of their strength and aesthetic appeal. With its load bearing qualities, brick can support an entire building while requiring little maintenance. While brick is often considered “traditional,” it is also going through innovation.
Wool Brick:
Originated in Spain and Scotland, wool brick is made by adding wool fibers to regular clay material used in traditional bricks. The purpose of the fiber is to reinforce the brick, reduce production time, and avoid deformities. The wool and clay combination is then mixed with a natural polymer extracted from seaweed.
Wool brick emits zero carbon as an unfired, naturally dried material whereas traditional bricks are fired using large amounts of coal and natural gas creating greenhouse gases. Zero carbon emissions aside, unfired brick like wool brick is approximately 37% stronger than conventional brick using unfired earth products.
Wool brick is stronger than conventional brick, it is more durable, leaves less of an environmental footprint and is non-toxic, which may warrant its increased use in the future.
Pollution-Absorbing Brick:
Pollution-absorbing brick removes pollution from air as opposed to innovative materials, which only reduce pollution. Also known as breathe brick, pollution-absorbing brick serves as an air filtration machine.
Developed by professor architect Carmen Trudell at Cal Poly San Louis Obispo, breathe brick was inspired by the cyclone filtration in vacuum cleaners. Working on the basic premise of air filtration systems, pollution-absorbing bricks take in air, then separates pollutants and other particles.
Breathe bricks are made of porous concrete, having faceted shape with recycled plastic placed between two bricks. A hopper is installed at the base to collect particles—basically a double walled building cavity with a cyclone filter. Like a vacuum, breathe bricks filter 30% of pollution particles and need to be cleaned.
Although breathe bricks can only be used in one-two story structures when used as a load bearing material, they do not use much energy. They are inexpensive relative to other air-filtration gadgets, and they are made with recycled materials. Breathe bricks do take up more space due to their shape and pattern; however, they are most sustainable and more environmentally friendly than traditional bricks. While very innovative, breathe bricks do not require a specialist to construct a breathe brick system, rending them cost-effective.
CLOSING THOUGHT
Our world is constantly changing, and construction is not immune to those changes. New, innovative construction materials are the wave of the future, and the growth of the industry over the next couple of years will be immense once these products are widely available.
Sources:
- Science Direct, Self Healing Concrete (November 08, 2021), www.sciencedirect.com/topics/engineering/self-healing-concrete.
- Cement World, The Development of Light-Emitting Cement (November 07, 2021), www.worldcement.com/the-americas/09052016/development-light-emitting-cement-62/.
- Southern Aluminum Installations, Inc., How Aluminum Launched to the Top of the Industry (November 08, 2021), www.southernaluminuminc.com/aluminum-launched-top-industry/.
- Technology in Architecture, Transparent Aluminum – Aluminum Oxynitride (November 07, 2021), technologyinarchitecture.com/transparent-aluminium-aluminium-oxynitride/.
- The Aluminum Association, Building & Construction Quick Read (November 07, 2021), www.aluminum.org/product-markets/building-construction.
- Science Daily, Bricks Made with Wool (November 08, 2021), www.sciencedaily.com/releases/2010/10/101005085503.htm.
- Phys.org, Bricks Made with Wool (November 07, 2021), phys.org/news/2010-10-bricks-wool.html.
- Architecture Magazine, Breathe Brick (November 08, 2021), www.architectmagazine.com/awards/r-d-awards/citation-breathe-brick_o.
- Arch Daily, This Innovative Brick Sucks Pollution From the Air Like a Vacuum Cleaner (November 07, 2021), www.archdaily.com/771767/this-innovative-brick-sucks-pollution-from-the-air-like-a-vacuum-cleaner.
About the Authors:
Danielle Waltz is a commercial and construction litigator and government relations specialist in Jackson Kelly PLLC’s Charleston, West Virginia, office, where she is a member. She represents a variety of construction clients. She is a member of the International Association of Defense Counsel (IADC) and is active in its Construction Law and Litigation Group. She can be reached at dwaltz@jacksonkelly.com.
Alexis Hailpern is a commercial attorney in Jackson Kelly’s Denver Office focusing the majority of her practice on commercial transactions, including drafting and negotiating construction contracts. She can be reached at alexis.hailpern@jacksonkelly.com.
Modern Contractor Solutions, November 2021
Did you enjoy this article?
Subscribe to the FREE Digital Edition of Modern Contractor Solutions magazine.
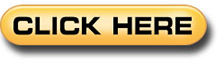