When a major contractor needed to rehabilitate several miles of the Chicago Transit Authority’s (CTA’s) rapid transit tracks, he relied on a portable modular conveyor to help meet the important requirements of placing ballast along the track bed.
BUILDING A NEW CHICAGO
The project was part of Chicago Mayor Rahm Emanuel’s “Building a New Chicago” initiative. The CTA’s Red Line South Reconstruction Project involved rebuilding the 10.2-mile stretch from just north of Cermak-Chinatown to 95th Street. According to the CTA, the 44-year-old line had exceeded its expected life and slow zones and delays plagued it. Five months later, the $425 million project—funded by the “Illinois Jobs Now!” program—delivered a brand new railroad to an estimated 80,000 daily riders.
The scope of work included improvements to eight stations and elevators to make the entire south Red Line more accessible to customers with disabilities. As noted, the project also included the placement of a new track bed, including new rail ties, tracks, and ballast (the stone material along the tracks).
A key to replacing the 1 to 3 inch ballast was a portable modular conveyor from E2 Systems, LLC. The versatile equipment helped the contractor meet some unique project needs.
The tracks are located between the eastbound and westbound lanes of Chicago’s busy Dan Ryan Expressway (Interstate 90/94), which presented one of the major challenges.
The project also involved placing more than 200,000 tons of AREMA (American Railway Engineering and Maintenance of Way Association) No. 3 ballast, as well as 90,000 tons of Illinois DOT CA6 (course aggregate), the placement of which mostly had to be at night, when lane closures would be least disruptive to Chicago commuters.
The project called for a minimum of 8 inches of sub-ballast: 12 inches of ballast placed under the railroad ties and 7 inches of ballast placed between the ties.
PLACING THE BALLAST
Although completing the track work under the auspices of the CTA, the contractor also worked with the Illinois Department of Transportation (Illinois DOT), whose specifications and standards applied to the adjacent highway.
The DOT provided guidance on lane closures and the use of the highway lanes and shoulders for equipment access. Workers needed to complete the work on the tracks and the adjacent area without disturbing the walls and fences, which meant the ballast had to be “pitched” over the safety/security structures that were required by the Illinois Department of Transportation.
The concrete walls and fences are a necessary safety feature, but they also made placing the 1- to 3-inch stone during the track reconstruction project more challenging. The contractor was only allowed to close a single lane and the shoulder from 6:00 p.m. until 6:00 a.m., which only provided a 17-foot working path.
“The Illinois DOT’s wall is 42 inches high, and the fence added another 2 feet of height, so we had to make adjustments to the equipment to clear the 6-foot barrier, which operated 6 to 8 feet away on the inside shoulders. A standard conveyor would not shoot the ballast that far,” says the project manager.
FINDING A SOLUTION
The contractor used two different approaches to placing the ballast. The first was a series of metal bins, into which dump trucks dropped the ballast. The boxes were then tipped over the walls and fences, after which, workers spread the ballast into place.
The other approach used E2 System’s portable modular conveyor, which a front-end loader placed along the shoulder. Moving the 8.5-foot-wide conveyor into place and assembling it to its base was easy because of its compatibility with most manufactures’ wheel loaders and other modular equipment. The conveyor can also be rotated 180 degrees to accommodate desired travel direction, another feature that proved helpful in both set up and operation.
After the short set up, individual dump trucks backed into place, deposited their loads of ballast into the conveyor’s 2 cubic yard hopper, and then the conveyor moved the ballast into place. Although the hopper was large enough to handle large loads, this project did not need the extra capacity, because the conveyor moved the ballast into place within seconds.
NON-STOP PRODUCTIVITY
As the first group of dump trucks headed back to staging areas (a nearby quarry and the contractor’s yard), crews easily and quickly moved the conveyor, which weighs only about 9,800 pounds. This process of “walking” the conveyor along the shoulder was smooth and seamless, and without any apparent effort or time.
“The biggest advantage is the very simple, open design,” the contractor’s project manager says. “There are not a lot of moving parts, which made me comfortable, especially with the large, abrasive materials we were handling. We looked at other equipment with augurs, multiple conveyors, and more. With other systems, we were concerned about the large ballast ripping the belt apart.”
At the end of the shift, the workers dissembled the conveyor, loaded it onto a lowboy trailer, and returned it to the yard. The conveyor folded at mid-point to travel in a 10-foot path while attached to the loader. Folding and travel features controlled from the conveyor’s base also helped make short work of loading and unloading the equipment, as well as assembly/disassembly from the base.
RESULT FOR CHICAGO
As for the City of Chicago, the CTA’s Red Line passengers now have a reliable rapid transit system that links riders between the south side and downtown in about 20 minutes.
Riders and casual observers may not be aware of how all that stone under and around the tracks got there, but for the contractor and agencies involved, it was no secret that an affordable, portable, and modular conveyor was a key component in this successful construction project. www.materialplacer.com ■
For More Infomration
For additional information about E2 Systems, LLC, call 248.795.3000, email info@materialplacer.com, or visit www.materialplacer.com.
Modern Contractor Solutions, November 2014
Did you enjoy this article?
Subscribe to the FREE Digital Edition of Modern Contractor Solutions Magazine!
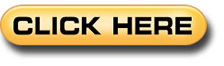