[h2]Part 1: Hydronic radiant floors deliver low-cost, low-energy comfort[/h2]
In North America, most interior spaces constructed in the past 50 years—from an agricultural barn to a single family home to a high-rise office building—are warmed by heating air and pumping it through the space. The actual goal is not to heat the air or the space, but the people and objects in it. Air is used to conduct the heat, but air is a poor conductor.
There is a more energy-efficient and more effective way. Radiant floor heating offers a comfortable environment from the ground up, without the noise of forced air and without the dust, microbes or mold spores that can get blown around by it. Modern radiant floor systems with high-performing insulating panels are energy-efficient, extremely comfortable, and lower in operating cost than conventional air-heating.
[h3]HOW IT WORKS[/h3]
Radiant heat is the way the sun heats the earth. The vacuum of space stops convection and conduction, but radiant energy, including light and infrared (heat) energy, pass through it brilliantly.
Radiant flooring works the same way. The floor is heated from underneath, either by hot water tubes or by an electric wire embedded in the subfloor, and that heat radiates outwards. Radiant energy directly heats liquids and solids in the room, including people. It warms a room from the bottom up, including warming the air, but air is not the main way the heat is transmitted. Occupants in a radiant-floor building often perceive the temperature to be 5 to 10 degrees warmer than the actual air temperature, because the people are being directly radiantly heated.
Of course, the floor described above has one large design flaw: it radiates heat downwards as well as upwards, which could waste heat into the ground or an unoccupied basement. Modern radiant floor systems redirect heat upwards by installing an insulator/reflector under the heating system.
[h3]WATER VERSUS ELECTRICITY[/h3]
The two main types of radiant floor are electric and hydronic. Electric systems are essentially long loops of high-resistance wire snaking around under the subfloor. The wire heats up when current is passed through it. It can be set in a thin cementitious underlayment to be topped by a floor covering.
Hydronic systems have a hot water tube looped around in the subfloor, usually cast into a few inches of concrete or lightweight gypcrete. A recirculating system pumps hot water from the heat-source through the floor, where it gives off the heat. Cooled-down water is returned to the source to be reheated.
Electric systems are usually cheaper to install, and so thin they add very little to the height to the floor. However, they are less efficient and can be 30 to 40 percent more expensive to operate. Because of the expense, they are usually used where only a small portion of the building is being radiantly heated (for example, one bathroom in a house), or where height is a problem. For whole houses, offices, retail spaces, barns, or any sizeable heating application, hydronic is the method of choice.
[h3]THE SYSTEM[/h3]
In simple terms, the hydronic system consists of 1) a heat source such as a boiler or thermal solar collector; 2) a recirculating pump; 3) a manifold distributor to direct heated water into different tube circuits, and collect return water; 4) circuits of tubing to carry the water through the floor; 5) an insulation board to hold the tube and conserve the heat, and 6) the floor itself.
When the thermostat calls for heat, water is pumped out through the tubing. Each circuit on the system can be controlled separately if it has its own thermostat. The tube heats the subfloor material and uses its thermal mass to store and distribute that heat. When the system is first started, it takes a little while to “fill up” the floor with heat before it starts to radiate effectively. Once heated, a 3-inch concrete slab keeps giving out heat long after the recirculating system shuts off.
Famed architect Frank Lloyd Wright designed his “Usonian” homes of the 1930’s with hydronic radiant floors using copper tubing. Since then, a number of different plastics have been tried, but the most common tube material now is PEX (cross-linked polyethylene), an extruded tube with excellent durability and high heat properties. Recently, PEX-AL-PEX tubing has gained popularity, because it prevents oxygen from leaking into the system and potentially shortening the life of the boiler. The most common diameters for PEX in residential radiant floors are 1/2-inch and 5/8-inch. Commercial floors use tube up to 1 inch diameter.
Floor configuration has evolved, too. Systems years ago used flat foam insulation boards—either bare or foil-faced—and had a variety of arrangements for holding the tubing in position for concrete: clip-racks, plywood panels with routed tube-channels, or simply stapling the tube to the foam.
New all-in-one foam insulation boards simplify installation. Flat foam with routed tube-channels came first, but that allows only one tube-spacing and minimizes insulation thickness below the tubing where it’s needed most, reducing efficiency.
The most recent improvement is the molded EPS PEX board, such as the Amvic Insulated Radiant PEX Board, a design that features a uniform insulation thickness under both concrete and tubing. They are available in different thicknesses and densities for varying R-values. Panels of this type feature molded mushroom-shaped nubs that hold the PEX in position but leave it largely exposed to the concrete for maximum heat transfer. The nub approach allows flexibility in designing the tube layout. EPS is a high-efficiency insulator for radiation, conduction, and convection, and strong enough to easily carry several inches of concrete.
In the next issue of MCS, Part 2 will focus on the design and installation of a hydronic radiant floor system.
<p style=”text-align: center;”>■ ■ ■</p>
[divider]
<strong>About the Authors</strong> Gary Brown is vice-president of marketing for Toronto-based Amvic Building System, a manufacturer of insulating concrete forms (ICFs) and rigid foam insulation. Including his 9 years at Amvic, he is a 24-year veteran of the energy-efficient, sustainable building industry. Brown can be reached at gbrown@amvicsystem.com.
Steven H. Miller, CDT, is an award-winning writer and photographer, and a marketing communications consultant specializing in issues of the construction industry. He can be contacted at steve@metaphorce.com.
<hr align=”left” width=”50%” />
<strong>Modern Contractor Solutions, <em>MAY 2014</em></strong>
Did you enjoy this article?
Subscribe to the FREE Digital Edition of Modern Contractor Solutions Magazine!
<a class=”subbutton” title=”Subscribe” href=”http://www.mcsmag.com/subscription-form/”><img src=”https://mcsmag.com/dev/wp-content/uploads/2013/05/BUTTON_ClickHere1.jpg” alt=”Subscribe” width=”202″ height=”35″ /></a>
Inner Warmth – Hydronic radiant floors
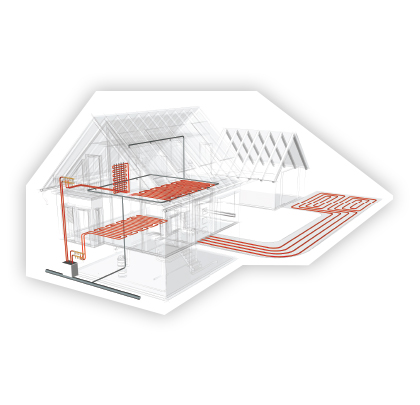