The Federal Highway Administration requires that bridges be inspected every 2 years. In the state of Michigan alone, 4,406 Trunkline bridges (40 percent of the total) are checked every 2 years to meet these requirements, resulting in 2,203 bridges examined annually. Bridge deck scanning methods typically include hammer sounding and chain dragging, which put bridge engineers and technicians on the bridge and in the lane near the flow of traffic resulting in significant safety concerns. By incorporating these types of inspection methods, there are also the inherent costs of lane closures, delays, and detours, referred to as Road User Costs. The FHWA mandates that states must minimize the Road User Cost aspect since it dramatically affects the motoring public with added fuel costs, lost labor hours, increased emissions, and more. However, there is a safer, faster, and more cost-effective technology available.
Using high tech electro-optic lenses, experienced and certified thermographers are able to identify and locate subsurface defects or cracks at highway speeds of 50 miles per hour with no lane closures. During these bridge deck scans, the thermographers remain safe inside the service vehicle within the flow of traffic, resulting in higher bridge scan completion rates per day. With deck scanning executed at highway speeds, commerce is able to maintain a continuous flow, eliminating the Road User Costs associated with lane closures and traffic delays.
THE TECHNOLOGY
Using surface temperature maps, thermographers are able to detect delaminations inside the concrete bridge structure. A standard video camera intercepts and records the reflection of visible light, whereas infrared cameras record naturally-occurring emissions and reflections of thermal light radiation. Unlike radar or microwave systems that both transmit and measure radiation, the sensor used is a safe, passive system that does not emit, so it can be used directly by operators in any situation without health or safety concerns.
Thermal Detection of Bridge Deck Delaminations
Bridge surfaces are subject to continually varying thermal inputs due to their exposure to atmospheric events, such as wind convection, solar radiation, and thermal radiation exchanges. Infrared scans are best performed during the steepest changes in bridge temperature. In the case of inclement weather the system software must advise the technician to refrain from acquiring data until conditions have optimized.
The thermal images from the scan record the infrared radiance of the bridge elements to identify hot and cold spots. These variations can indicate the presence of delaminations within the concrete. The infrared imaging sensor with GPS tracking and sophisticated analysis software are synchronized to accurately locate delaminations.
Substructures
With an infrared scoping service, the thermally visible delaminations in concrete substructures and superstructures can be detected either from inspection boats when needed or handheld or tripod mounted from the ground. Precision digital range finders and specialized collection software allow accurate measurements of the delamination surface area which can be later quantified during analysis of collected image data. The variety of specialized and calibrated optics allow for such scoping practices to be done from distances of 100 feet. This eliminates the need for lane closures where a typical snooper truck would otherwise be used to access the substructure elements with no Road User Costs being incurred.
Visible Crack Detection
To accompany the infrared scans, high-definition visible band imagery can be used to identify cracks, patches, and spalling in the bridge decks. The reporting of these cracks should consist of a description using the corresponding AASHTO Condition States, following the standard for those cracks that fall into the various condition state categories.
Results
Following the bridge scan, certified thermographers analyze the infrared deck defects using advanced analysis software that allows for quantification of the delamination and spall defect areas. Most bridge engineers prefer to receive results in the form of MicroStation or AutoCAD drawings showing all of the numbered defect areas drawn in proper location and orientation with a high degree of accuracy. Crack data from the visible band imagery is often presented as another layer on the same MicroStation or AutoCAD drawing and can be accompanied by information including number, density, and size of the crack. After project completion, the files are traditionally provided to the client to enable end users to seamlessly integrate the critical information into existing bridge files. As bridge data is compiled over time, regression models may be generated for comparison of bridge decks, rate of delamination growth, and an analysis of multiple bridge deck characteristics.
One example of this technology was developed by a team of engineers and thermographers at BridgeGuard, a division of Talon Research, Inc. Engineers with BridgeGuard specialize in the infrared detection of hidden objects in industries ranging from military to medical, security to infrastructure. Their proprietary technology has been contracted in 10 states and has been demonstrated in another 20 states across the country.
Bridge deck scans can be completed at 50 miles per hour while technicians remain inside the vehicle eliminating safety concerns and Road User Costs. This unique infrared application and accompanying sensors form a sensor suite that far surpasses the existing ASTM standard for bridge inspections. The deliverable is a highly accurate and easily integrated native CAD file format. The outcome is an accurate prioritization of a bridge owners’ assets and a significant reduction in contractor overruns for rehabilitation projects.
The BridgeGuard technology has the ability to collect large amounts of data at up to 1,000 times faster than traditional chain drag and sounding methods, resulting in cost savings. Bridge owners and taxpayers can save up to 70 percent with BridgeGuard technology on large bridges with high-traffic counts by eliminating Road User Costs and avoiding safety concerns. The end result is that millions of dollars can be saved with a comprehensive systematic and technology based asset management approach. ■
About The Author:
Dorothy Ruohonen is the CEO and owner of BridgeGuard, a division of Talon Research, Inc. For more information, contact David Raasakka, national sales manager with BridgeGuard, at 906.483.2667, or visit www.bridgeguard.net.
_________________________________________________________________________
Modern Contractor Solutions, December 2013
Did you enjoy this article?
Subscribe to the FREE Digital Edition of Modern Contractor Solutions magazine.
Infrared & Visible Bridge Scoping
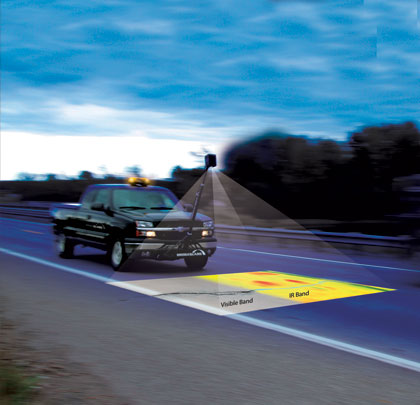