The pandemic accelerated trends in the construction industry related to labor shortages, supply chain disruptions, and material cost increases. Ultimately, these trends resulted in an increased appetite in the sector for offsite or industrialized construction, new methods of material procurement, and technology adoption.
Here are specific trends that the industry can expect to see in 2022:
1. RAPID GROWTH OF PREFAB & OFFSITE CONSTRUCTION METHODS
The challenges mentioned above facing the industry today are pushing contractors to embrace offsite prefabrication to deliver projects effectively. Safety protocols during the pandemic also drove production offsite to prefab shops and factories to prevent the spread of COVID at the jobsite.
Also relevant to the rise of offsite methods are the ubiquitous use of 3D BIM modeling, onsite 3D scanning to determine as-built conditions, and software platforms purpose-built to run offsite factories, which simplify this transition. This is leading to an expansion in the amount of single- and multi-trade prefabrication, panelization, and volumetric modular construction being done offsite.
Trade and specialty contractors who adopt prefab methods are seeing additional benefits. They can pull dangerous or time-consuming overhead work into the shop to increase their teams’ safety and efficiency. They are also developing standardized catalogs of items that their prefab shops can efficiently produce so jobsite teams know which types of prefabs they can request to accelerate their install schedules. This has some follow-on benefits: it standardizes the parts used in the shop, limiting waste and simplifying material procurement. Additionally, as the production capacity of the prefab shop is better understood, contractors can build product catalogs for their design and detailing teams, allowing the production of more repetitive prefab elements and increasing the efficiency of the shop teams.
2. REAL-TIME TRACKING OF SUPPLY CHAIN NETWORKS
The continued rise of offsite construction creates new challenges and opportunities for general contractors. As they develop new kits-of-parts and jobsite-based assembly factories, opt for the direct procurement of materials, or leverage more single- or multi-trade offsite prefabrication, the complexity of tracking what’s getting produced, which stage of production and where offsite elements are, as well as quantifying subcontractor or vendor delivery and installation performance also increases in complexity.
These complexities drive the adoption of better, more comprehensive software platforms for tracking procurement, production, delivery, and performance in real time. These are being adopted in the point solutions or custom spreadsheets that have traditionally sufficed to track project deliveries and subcontractor performance. A best practice for teams looking to understand the current state of prefab operations for their business is to adopt technology that provides real-time visibility into specific jobs, including current status, location, and timing of produced materials. This improves accuracy of projects and drives productivity for today’s teams.
3. INCREASING USAGE OF MASS TIMBER & OTHER SUSTAINABLE MATERIALS
According to a recent report from United Nations Environment Programme, the building and construction industry is responsible for nearly 40% of global greenhouse gas emissions. As the industry at large is beginning to realize its impact, it’s identifying new best practices, processes, and materials to reduce carbon emissions and increase energy efficiency. Leading the way is Mass Timber, manufactured using small-diameter lumber from sustainably managed forests. Mass timber sequesters carbon and helps projects meet sustainability targets.
Timberlab grew from the desire to alleviate pinch points in the mass timber industry through ownership of essential services and products that are not widely available in the construction market. A Swinerton company, Timberlab, was launched to deliver the entire lifecycle of a mass timber project from inception to installation and accelerate the mainstream adoption of mass timber. From Ascent, the world’s tallest hybrid building, to the PDX Airport Terminal Redevelopment—Timberlab is a leading example of wood innovation and prefabrication possibilities.
4. RISE OF THE BUILDING PRODUCT PLATFORM
Historically, the construction industry has started every project from scratch: planning, designing, and constructing each custom project in a one-off fashion. Not standardizing or “productizing” reusable design and fabrication elements results in wasted time and resources, higher costs, and prolonged schedules. Now, however, innovative building owners and developers are leveraging their work from previous projects, developing catalogs of reusable elements, and applying them to future projects. These kits-of-parts are paving a new way forward for the industry.
Once defined, the kits-of-parts are incorporated into building product platforms used to quickly generate new project designs in a fraction of the time traditionally required. This dramatically reduces the soft costs associated with design, estimating, and project management. These product platforms are now being developed for many building types, including data centers, global hotel chains, healthcare facilities, commercial offices, multifamily housing, and more.
Additionally, these building product platforms allow owners and developers to move up the value chain, unlocking new revenue streams with reduced supply chain risk. With a product platform, it’s finally possible for owners and developers to own desirable portions of the supply chain through the direct procurement of high-margin materials with opportunities to leverage volume discounts on bulk purchases. Not only are there cost advantages, but direct deals with partner manufacturers and material suppliers allow greater confidence in timely material deliveries through comprehensive material demand forecasts.
CLOSING THOUGHT
The pandemic has increased the pace of change in the construction industry. What’s emerging now is a more innovative industry embracing new project delivery methods, including offsite construction and prefabrication, new levels of productization of buildings, and direct procurement of materials. By embracing these innovations and the new digital technologies that enable them, productivity rates are increasing, and contractors, owners, and developers can move up the value chain to add more value and earn more revenue on projects.
About the Author:
Justin Schwaiger, PE, is Manufacton’s director of customer success, enabling construction companies to efficiently run their offsite factories by building scalable implementation programs and partnerships advancing industrialized construction. For more, visit www.vizztechnologies.com.
Modern Contractor Solutions, May 2022
Did you enjoy this article?
Subscribe to the FREE Digital Edition of Modern Contractor Solutions magazine.
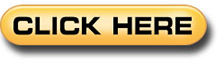