Inspection processes, like other aspects of construction management, are evolving … and that’s good news for construction businesses.
It’s tempting to view a construction inspection as a simple, linear process. It may even seem that this is one area in which traditional—and manual—methods don’t need to be changed. But, there are several compelling reasons why many construction firms are switching to software-based inspection processes.
SAFETY
Worker safety is a key area that can benefit from an improved inspection process. OSHA uses its News Release/Enforcement page to publish the dozens of violations it identifies over the course of each month, along with fines assessed. While the violations occur across a range of industries, prominent on each list are construction firms … a somber reminder that jobsite conditions are complex and difficult to oversee. Achieving optimal safety requires constant diligence, achieved in large part by timely, detailed inspections.
Equipment inspections are tied to worker and public safety (as well as to job schedule and profitability). Multiple pieces of heavy equipment on every jobsite require daily, monthly, and annual assessment. This translates into a tremendous amount of data to be collected and distributed to decision-makers. Any breakdown in the system can have dire consequences; for example, experts have speculated that the Tappan Zee crane collapse in July 2016 could have been due to an overlooked equipment deficiency. Even before the Tappan Zee incident, New York City was in the process of implementing new regulations surrounding crane use, prompted by a February crane collapse in Manhattan. With each new round of safety measures adopted by governing agencies, construction firms face a change in work flow, habits, and data collection.
LITIGATION
HG.org, an online law and government information site, features an article titled “Construction Defects: What Often Goes Wrong and How the Contractor Can Avoid Defects Litigation.” Originally published in the mid-1990s, the article gives insight into the difficulties contractors faced in their effort to reduce construction defects in a pre-digital era. It states, “Inspection is a crucial function that does not start with the building inspector, or the special inspector. Inspection must begin with the superintendent. The superintendent must be aware of the resources available to him to gather sufficient information to assure that the work is being performed in accordance with the approved plans and specifications, and the manufacturer’s recommendations for the use and installation of the material products being used, and that the work is in conformance with the requirements of the Codes.”
This assessment reflects an extraordinary burden of responsibility, along with a presumption of extensive inherent knowledge on the part of every supervisor. In reality, a lack of adequate access to all available resources frequently led to incomplete inspections, and consequently, to defects that were not caught during inspections. Today, this situation can be significantly alleviated through the use of software, especially conditional software that feeds relevant data to the inspector and is available in real time via mobile device on the jobsite.
MARKET-DRIVEN CHANGES
As if increased safety and fewer construction defects weren’t enough, there is a direct market incentive for honing the inspection process: Doing so can translate into winning more work. Concepts such as quality control and risk management are much discussed in project management circles. The underlying goal of these efforts is to reduce mistakes and prevent slowdowns. Improving the end product handed over to owners—along with handing it over early or on time—also earns business.
Inspections directly support quality control and lower risk by benchmarking construction progress against a project’s predefined scope, budget, and goals. But, they can only do so if they are complete, accurate, and accessible.
COMPLEXITY OF INSPECTIONS
In the past, the true complexity of inspections often became apparent only after the fact, when litigation, safety incidents or citations, and/or owner feedback shed glaring light on the weaknesses of the process. Paper forms, which in theory were completed, signed, dated, and stored chronologically in binders, were in fact often difficult to locate. Other times the forms, if located, proved to be incomplete, especially if inspectors had inadvertently used outdated forms. Notes and photos that were created to accompany inspection forms easily became separated and lost. As the pieces of paper multiplied in number, the storage system became less accurate. Because information transmission and storage was so difficult, supervisors, owners, and other key personnel had limited visibility into project details.
Desktop computers with software applications, along with company servers, represented the first wave of digital inspection management. These tools represented a great improvement. Still, files that were emailed or loaded onto the server became lost in the system. Incompatible file types were particularly difficult to keep together (think word processing documents or pdfs that needed the support of photographic evidence stored as .jpgs).
CLOUD-BASED SOLUTIONS
Mobile, cloud-based solutions offer a welcome alternative to paper and desktop applications. Software-as-a-Service (SaaS) inspection forms are easy to access by all personnel in the field, using a tablet or smartphone, even when an internet connection isn’t available. Once forms are completed and synced to the cloud, they are instantly accessible to other team members, although many software solutions are configured in such a way that data cannot be altered by non-authorized staff. Workflow and role-based permissions provide a chain of custody and version control.
Missing and incomplete forms become a thing of the past. Different file types (photos, signatures, calculations, etc.) are kept together and automatic electronic time and date stamps keep paperwork in chronological order.
The benefits of switching to cloud-based data collection are immediately realized. Construction schedules—and profits—are easier to maintain, because real-time information sharing via the cloud can lead to faster problem resolution. Defects and safety oversights are less likely to escalate, reducing the risk of incidents, citations, or litigation. These benefits compound as they carry over from project to project and foster a company culture that becomes a competitive advantage. ■
About The Author: Darrin Harris is the CEO of Kordata. With more than 15 years of experience in building mobile solutions, Kordata was created to serve those businesses and enterprises that struggle to find a software solution that truly fits their company. Recognizing that every business has its own set of unique, evolving challenges, the Kordata platform is built with complete flexibility and configurability, allowing organizations to collect and manage their data across multiple operations in a way that fits their business. For more information, visit www.kordata.com.
_________________________________________________________________________
Modern Contractor Solutions – September 2016
Did you enjoy this article?
Subscribe to the FREE Digital Edition of Modern Contractor Solutions magazine.
Improving Inspection Data Collection
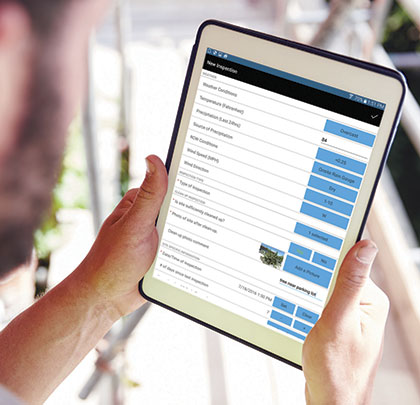