Things are changing within the construction and demolition industry. While worker safety has always been a primary concern on any jobsite, a growing focus on overall environmental impact is causing contractors to rethink how things have traditionally been done. Noise and dust restrictions are key concerns on every jobsite, leaving contractors to find new ways to remove concrete that are less invasive.
For many contractors around the world, Hydrodemolition has emerged as an ideal solution to these challenges. Remote equipment operation keeps workers out of harm’s way and reduces physical demands, resulting in fewer injuries. Hydrodemolition also eliminates the risk of silica dust exposure for operators and the public and is considered one of the quietest methods currently available.
Additionally, Hydrodemolition revolutionizes what contractors can accomplish in a day compared to handheld tools and other manual methods—completing jobs up to 25 times faster in some cases with a 30 percent labor savings. The ability to improve productivity, even amid labor shortages, allows Hydrodemolition contractors to expand their markets and opportunities without expanding their crews.
Are there any Hydrodemolition specific challenges contractors should be aware of if they are considering adding this method to their service offerings?
Wastewater treatment should be considered by any contractor looking to add Hydrodemolition to their service offerings. While the method provides a number of benefits, the wastewater it produces has an increased pH level and high turbidity—cloudiness or haziness caused by debris—and needs to be handled correctly. Wastewater restrictions have been increasing recently, following a general trend in more stringent environmental protections.
Fortunately, to keep contractors ahead of the curve, fast, cost-effective solutions, like our EcoClear, are available from original equipment manufacturers. These self-contained units meet or exceed current standards to provide on-site, on-demand water treatment that gives contractors more control and versatility.
How is Aquajet evaluating and addressing all challenges to help contractors stay competitive?
Customer feedback has always played an important part in our designs and innovations. By listening to the contractors using these machines day in and day out, we’ve been able to provide solutions to not only changing regulations and the broader trends in the industry, but also the everyday challenges our customers are facing. The result is innovative equipment options, like our EcoClear or the brand-new Ecosilence 3.0, that open up new markets and applications for Hydrodemolition contractors.
In general, how do you incorporate customer feedback into your designs?
When an operator comes to us with a challenge—say, for example, the need for more precise, consistent concrete removal—we look for ways to make it happen. The end result might be a system upgrade like our Equal Distance System (EDS) that increases safety and ease of use. Or, for more substantial challenges, like improving the versatility of an existing product to better meet customer needs, it could result in a brand-new machine, as was the case with the Ecosilence 3.0. A combination of customer feedback and innovative solutions from our team led to a total redesign of this self-contained system, which houses a high-pressure pump and engine combination to power a Hydrodemolition robot, as well as integrated water tank and filters.
Can you give a specific example of a customer-driven solution?
Our Ecosilence 2.0 was popular because the low noise levels allowed Hydrodemolition operators to work in sensitive areas like urban centers and around hospitals and schools. However, one customer, who was working in a harbor, came to us with a unique problem. The old design relied on pulling in outside air to cool the engine. In this case, the cool marine air flooded the compartment with fog. Solving this challenge led to a brand-new, cutting-edge machine that allows Aquajet customers to successfully operate in a number of demanding situations.
To solve the fog problem, our engineers looked at ways to isolate the engine from the cooling system to prevent dust, debris, and cool air from causing disruptions. This resulted in a new skid-mounted unit that features an integrated, low-emission engine with the latest technology and a liquid-to-air heat exchanger. It employs auto start/stop technology, which temporarily shuts down the engine when not in operation, reducing idling and saving as much as 20-25 liters of fuel a day. By isolating the engine, our engineers were able to further limit sound emissions, as well.
From there, we were able to reduce the overall size of the container to just 20 feet—ISO standard size for easier transportation—while maintaining ample space for a work bench, tools, hose storage, and an Aqua Cutter 710 Hydrodemolition robot.
The word innovative gets used a lot with new products. What does this word mean to Aquajet, and how do you see innovation incorporated in your designs?
A lot of the time, when people use innovative, they just mean new. And, while that is certainly true, for Aquajet, innovative means more. In addition to being cutting edge, the product or feature has to provide demonstrable benefits to the operator over what is already existing. We don’t want new for the sake of new; we strive to make the changes and updates that will revolutionize the safety, productivity and overall efficiency for our end users.
Our engineers approach every task with this definition in mind. They look for ways to incorporate customer feedback and the latest science and technology to create products that solve the challenges of today’s Hydrodemolition contractors.
What do you think will be the biggest challenge for Hydrodemolition contractors in the next 5 years?
We feel the next 5 years will see increasing regulations on dust, vibrations, noise, and other aspects that were previously considered “part of the job” continue for all construction and demolition contractors. Along with that, we believe Hydrodemolition contractors will see increased stringency on wastewater regulations. Looking ahead, it’s safe to say our products will continue to evolve to meet these changing regulations. Our products, including the EcoClear and the new Ecosilence 3.0, are engineered for the most stringent markets, putting our customers ahead of the curve, and our engineers will continue working to keep them there.
for more information:
Aquajet, which was acquired by Brokk AB in 2016, is known as the industry leader in Hydrodemolition machines and solutions, both in terms of quality and volume. The company’s headquarters and production facilities are in Holsbybrunn, Sweden. Similar to Brokk, Aquajet sells globally. For more, visit www.aquajet.se.
Modern Contractor Solutions, July 2020
Did you enjoy this article?
Subscribe to the FREE Digital Edition of Modern Contractor Solutions magazine.
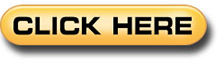