By Thomas Renner
Innovation is the name of the game for many industries seeking new solutions to solve problems, improve efficiency, or boost the bottom line. One of the last places most architects or contractors look to innovate, however, is up. While roofing materials have improved over time, there is little that can be done to the inherent structure of a roof. The reasons are obvious. For structural and performance reasons, there is little wiggle room in roof design. Roofs are not like pizza varieties.
A recent project for the Virginia Department of Transportation at its hazardous chemical storage building debunks thoughts that there is a lack of creativity in roofing design.
The team of architects and engineers at Gauthier, Alvarado & Associates designed a hybrid solution that is cost efficient, durable, and unique in the roof design of the building. The solution includes roof hatches, a coating material that is most often associated with truck beds, and EPDM roofing—an extremely durable synthetic rubber roofing membrane—that is expected to last up to 35 years. The primary objective of the solution was to stave off corrosion caused by materials that are stored in the building.
“Since this is a government project, longevity was a priority,’’ says Stephanie Stein, the lead architect on the project for Gauthier Alvarado. “As a result, any surface that comes into direct contact with the salt needed to be corrosion resistant to increase the lifespan of the building in this extremely corrosive environment.”
SALT-INDUCED CORROSION
Salt for roads is the primary material stored in the building. This salt is applied to roadways to improve safety, but the material has a detrimental effect on building materials. Salt removes moisture from an environment, causing a hygroscopic reaction. The mineral retains water, which then promotes condensation. The water absorption allows corrosion to occur at lower humidity and for longer periods than otherwise expected. Salt also increases water’s ability to carry current and hastens the corrosion process.
As a building ages and the overall salt content of the building increases, the building fabric tends to become damper over time. When the wet salt dries out, it crystalizes and expands, creating pressure that over time breaks down the building fabric. Crumbling, spalling, flaking and cracking of the building fabric is largely related to the crystallization of salts.
Roofing materials and other components in the Virginia building showed impacts of corrosion, requiring a new roof and some rebuilding of concrete walls.
UNIQUE SOLUTION
The building sits in a hilly region of the state, near the West Virginia border. Accessing the site is challenging, and one objective was to simplify delivery and loading operations.
To solve that dilemma, architects specified three aluminum roof hatches manufactured by The BILCO Company. The hatches, 3-feet, 11-inches wide and 11-feet long, are manufactured with Type 316L stainless steel hardware, which is the most corrosion-resistant type of stainless steel. The roof hatch curbs were coated in an asphalt-based liquid coating to provide an additional layer of protection for the concrete inside the building.
“BILCO offers stainless steel roof hatches, but since this is a project that is designed and built on a government budget, we provided a more economical solution,” Stein says.
The unique solution to protect the hatches from corrosion came in the form of a liner. The spray-on material, installed by Rhino Linings of Winchester, Virginia, is most frequently applied to truck beds. The company has applied it in other applications as well, such as vans, boats, and even dugouts for baseball teams. The polyurethane material protects against corrosion while also providing excellent abrasion, impact, and chemical resistance.
“With this solution, we combined the durability associated with the BILCO pre-manufactured aluminum roof hatches with the corrosion-resistant properties of the truck bed liner,” Stein says.
Dinks Construction, the general contractor for the project, installed the roof hatches while a team from Don Largent Roofing installed an EPDM roof.
ADDITIONAL MEASURES
The structural engineering team took additional steps to protect the durability of the hatches. “One of our prime concerns during the design phase was the additional force exerted on to the roof hatches during salt loading operations,” Stein says.
They designed a structural steel bumper to provide additional support to the roof hatch. When the hatches are open prior to loading the building with salt, the roof hatch covers rest upon the bumpers. “The additional force applied to the roof hatch covers during the salt loading is then directly transferred to the steel bumpers to protect the structural integrity of the roof hatches,” Stein says.
The building’s design not only protects against corrosion, but also allows for a quicker, more efficient solution for storing the chemicals. For hazardous storage buildings without roof access, salt has to be moved by front-end loaders or some other type of conveyance. The drop-and-go solution is much quicker and even more environment-friendly. Road crews access the salt from the lower part of the building.
CLOSING THOUGHT
Tucked away a short distance from the highway and nestled in the region’s hills, the structure will not generate tremendous attention. It is nonetheless critical to improving roadway safety, and offers a long-term solution to a challenge that faces many communities in the storage of corrosive materials.
“This was a fun project because it was quite different,” Stein says. “This was our second roof and roof hatch system that we designed for VDOT. We had the opportunity to incorporate a few lessons learned from the first roof system replacement. It is our hope that we will continue to adapt this roof system prototype for additional VDOT sites in the future.”
About the author:
Thomas Renner writes on building, construction, engineering and other trade industry topics for publications throughout the United States.
Modern Contractor Solutions, July 2021
Did you enjoy this article?
Subscribe to the FREE Digital Edition of Modern Contractor Solutions magazine.
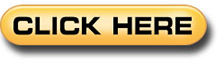