During heavy rainstorms a large metro area’s waste treatment facility can be pushed to its capacity. And when overflow becomes an issue, the community’s homes and businesses can get flooded.
In Chicago, the Metropolitan Water Reclamation District (MWRD) is taking steps to “reduce the destruction caused by future strong weather systems in our region”—aka, flooding. MWRD will be undertaking an expansion project at the wastewater treatment facility located in nearby Lemont, Illinois. According to MWRD, the Lemont plant will benefit from a new $30 million Wet Weather Treatment Facility to help improve stormwater management. The project has begun and will be completed by summer of 2015.
THE PROJECT
The Lemont project includes a new pump station, a diversion structure for emergency high-level overflow, separator and disinfection, and yard piping and tie-ins to an existing electrical and controls distribution system.
Additionally, a significant component of the project is the construction of a diversion structure for emergency high-level overflow. The new wet weather reservoir and wet well make up a large in-ground concrete structure, measuring 215 feet by 165 feet by 30 feet deep. The concrete walls are 2.5 to 3 feet thick and the base measures 4 feet thick. It is expected to be solid, leak-proof, and capable of handling overflow from the biggest storms. Joseph J. Henderson & Son, Inc. won the contract for the construction of the overflow reservoir structure. Established in 1928, J.J. Henderson is a family owned, design-build general contractor.
The site for the new stormwater management reservoir in Lemont is predominately rock—a mixture of aged dolomite, limestone, and slurry.
J.J. Henderson first used a robotic total station to set control points throughout the site as a basis for registering the 3D laser scanner point cloud data.
For the blasting operations, J.J. Henderson contracted Ludwig Explosives, Inc., Lemont, Illinois, and assisted them with layout of the blasting limits to match the final excavation configuration. Approximately 55,000 cubic yards of rock and soil were removed from the site in 8-foot lifts.
“Ludwig Explosives was very accurate in following the excavation plan,” says Sam Henderson with J. J. Henderson & Son, Inc. “To provide a safe work environment in the excavation, rock anchors and a chain-link fence were draped over each wall to catch and hold back any falling rock.”
The construction of the concrete wet weather reservoir structure began with pouring a 1-foot-thick mud slab as a level footing for the base slab varying between 3 and 5 feet in thickness. A total of 600 rock anchors measuring 33 feet long and approximately 1½ inches in diameter were driven 30 feet into the ground. The rock anchors are designed to secure the base from uplift-pressures, since the reservoir is only full during major storm events.
The sheer excavated walls were monitored weekly to verify that the wall surfaces had not shifted. This monitoring focused on safety for workers in the deep pit constructing the reservoir structure.
PRECISION POINTS
With the Lemont plant project, J.J. Henderson used its Topcon GLS-1500 laser scanner to create point clouds of the excavated sheer walls to monitor any movement. Scan data recorded from different control points was registered using Topcon’s ScanMaster 3.0 Office Software. The registered point clouds were then exported in a .pts format to Bentley’s Power GEOPAK, where the point clouds were overlaid onto the project engineers’ site model. J.J. Henderson used this workflow to compare the excavation dimensions to the site design, verifying that enough rock had been removed.
“We conducted weekly surface-to-surface comparisons of the registered point clouds looking for deformation in the rock walls,” says Henderson.
According to Henderson, the laser scanner has been critical to the company’s effectiveness and productivity on the Lemont plant wastewater treatment facility diversion structure.
“I conduct weekly scans of the rock walls using the laser scanner’s occupation and back sight scanning techniques to register the data. I found that a few of the hubs that I’ve been setting up over are now inaccessible as equipment has moved throughout the course of the project,” Henderson says. “The site is growing more crowded as the project progresses. I’m usually able to set up over any one hub and using occupation and backsight orientation, register the data. In one instance, a key control point I’ve been using for the scans was being blocked by a crane moving rebar.”
To accommodate, Henderson set up in another (unknown) location with a clear line of site to the area of interest. He then target scanned two known points. Back in ScanMaster 3.0, tie points created from the target scans were used to run a resection, enabling registration of the scans.
On another occasion, a temporary setup point that was used in lieu of an established control point lead to a miss-registration.
“I knew the points I target-scanned were accurate … I checked all points in with a total station to verify accuracy and point integrity, so I knew this wasn’t an issue,” Henderson stated. “The miss-registered scan was a 1-hour-and-40-minute scan with critical data for monitoring. I absolutely needed this scan/point cloud for deformation monitoring. The only way I was able to register the scan with a high degree of accuracy was with the cloud-to-cloud registration.“
Henderson continues: “Since I was able to trust the accuracy of the hubs/permanent points, as they were verified with a 3-second total station, and was able to perform the occupation and backsight scan from a few of these hubs, I set one of them as the active scan—the scan to register to—when using cloud-to-cloud registration. Once the registration process was completed, I was able to review the ‘residuals’ report. I found that all points sampled and registered via cloud-to-cloud fell well with-in the acceptable range/error tolerance for this project. Without registration via cloud-to-cloud, the scan session would have been wasted and key data would have been missing. Cloud-to-cloud really saved the day’s work.”
As the new wet weather management reservoir in Lemont enters its final construction phase, the Chicago Metropolitan Water Reclamation District has restored confidence that the city will be safer from the harm that can occur from strong weather systems. ■
About The Author
Jeff Winke is a business and construction writer based in Milwaukee, Wisconsin. He can be reached through www.jeffwinke.com.
Modern Contractor Solutions, January 2015
Did you enjoy this article?
Subscribe to the FREE Digital Edition of Modern Contractor Solutions Magazine!
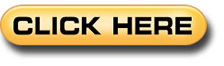