Construction equipment cannot be maintained while it is running safely and earning money, but it also cannot run safely and earn money if it is not properly maintained. Software applications for equipment maintenance, scheduling, and dispatching and field tracking provide contractors with powerful opportunities to address this inherent dilemma. However, utilizing all these applications together—connected in real time—is the key to unleashing their true potential to improve efficiency and profitability.
AVOIDING DISRUPTION
Equipment maintenance, resource scheduling, and field operations have interrelated—and sometimes conflicting—objectives when it comes to maintaining, deploying, and operating equipment. Using independent point solutions, regardless of how good they are, tends to leave the teams managing these three workflows operating in silos. Without real-time, online connectivity, equipment downtime, jobsite disruptions, and costs can soar.
Unified software applications, however, can dramatically improve communication and coordination, making it easier for contractors to balance their equipment repair, preventive maintenance, and production needs.
COORDINATED APPROACH
Definitive knowledge of where equipment is and where it is going to be is an important prerequisite of a coordinated approach. This is easier for smaller operations. For larger contractors, knowing where an asset actually is may not always be obvious. Relying on phone calls and offline, manual processes to manage equipment moves across multiple projects can lead to confusion and oversights.
Sending a mechanic to a jobsite to service a piece of equipment only to find out that it is no longer there happens more often than contractors admit. Telematics technology is a fool-proof solution, validating location through GPS coordinates delivered to scheduling and maintenance software applications.
Telematics data also helps contractors minimize “equipment hoarding,” the tendency of some managers in the field to keep idle equipment on a jobsite in case they might need it. With ironclad evidence of when and how often a piece of equipment is actually running, schedulers and maintenance teams have more leverage in convincing those field managers that they need to service the equipment or that it is needed on another site.
A single, shared operational database helps too. With this approach, a list of a company’s equipment assets is maintained and updated in one place. Individual software applications used to manage maintenance, scheduling and dispatching, and field tracking all have real-time visibility and can update this data. This eliminates miscommunication and discrepancies that can occur when the same equipment is referenced differently in each of the three systems.
Moving and maintaining equipment at times that are least disruptive to day-to-day production schedules has obvious advantages. That requires a level of visibility that only connected software can provide.
When maintenance software is integrated with the scheduling and dispatching application, for example, maintenance managers can see where equipment is and when it is scheduled to be running. They can also see in advance when it will be moved and where it is going.
OPTIMAL SCHEDULING
This insight can help them plan preventive and non-emergency maintenance work at the most opportune times, such as when an asset is not scheduled to be in production. They can also schedule and sequence work to maximize mechanic efficiency.
Similarly, when work is scheduled in the maintenance application, the date, location, and expected duration are visible immediately to managers using the scheduling and dispatching application. This real-time intelligence allows dispatchers to avoid unforeseen conflicts and to fulfill equipment needs, coordinate assignments, and schedule moves around these maintenance events.
Project managers, superintendents, foremen, and other leaders in the field also benefit when the field tracking application they use daily is linked with their company’s maintenance and scheduling software. Directly from the tracking application, they can enter requests for equipment needed on the jobsite. Those requests are then visible and actionable immediately in the scheduling application.
ISSUES ADDRESSED
Managers in the field can also generate equipment repair requests right in their field tracking application as soon as a defect is detected. These requests document the need and can include detailed descriptions and even photos or videos that could expedite the repair work. Importantly, these needs are communicated directly to the maintenance application. Immediate visibility means the maintenance team can address the issue more quickly and efficiently. Small problems can often be corrected before they become bigger and more costly issues or create safety risks.
Field managers can also monitor the status of repair requests in real time through their tracking application. This is a clear efficiency and productivity advantage. They do not have to wait and hope for a paper form to get from the field to the office to the shop. They are not left wondering whether someone got their voice or text message and when they will respond. Instead, they can plan production around the repair schedule and make better decisions about the need to request replacement equipment.
Resources, including individual employees, crews, equipment, and materials can also be requested from the field via the field tracking software. As with repair requests, these resource requests are visible and actionable right away, this time in the scheduling and dispatching application.
CLOSING THOUGHT
Heavy equipment is essential for heavy construction, and there is a lot riding on how efficiently contractors maintain and deploy their fleets. Specialized software applications to manage maintenance, scheduling and dispatching, and field tracking are important improvements over manual systems and spreadsheets, but these point solutions will only take contractors so far. Connecting these applications in real time increases exponentially their potential to minimize repair and rental costs and jobsite disruptions while maximizing uptime, utilization, safety, and profitability.
About the Author:
Greg Norris is communications director at B2W Software, a Trimble company. The B2W platform connects people, workflows, and data and includes unified applications to manage estimating, scheduling, performance tracking, equipment maintenance, data capture, and business intelligence. Greg can be reached at greg_norris@trimble.com. For more, visit www.b2wsoftware.com.
Modern Contractor Solutions, December 2023
Did you enjoy this article?
Subscribe to the FREE Digital Edition of Modern Contractor Solutions magazine.
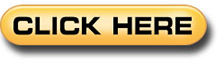