Heat Stress is Critical Safety Issue
After the horrendous winter that many parts of the U.S. experienced, the coming of summer is certainly welcomed by most of us. But less desirable is the potential for heat-stress-related illness on the job. Why is this a workplace concern? Simply put, heat can make workers ill or even kill them, and OSHA will hold the employer responsible. The construction industry has many job tasks that could put workers at risk, especially if they are engaged in roofing, framing, trenching and excavation, paving activities, or even operating forklifts to load trucks.
[h3]THE HEAT IS ON[/h3]
Factors that may cause heat-related illness include: high temperatures and humidity, low fluid consumption, direct sun exposure with no shade, limited air movement (no breeze), physical exertion, use of bulky clothing and equipment, poor physical condition, pregnancy, some medications, lack of previous exposure to hot workplaces, or a history of heat-related illness.
Exposure to excessive heat can cause heat stroke, where the worker’s body temperature rises to levels above 104 degrees and can result in death if not treated promptly. Signs include confusion, loss of consciousness, and seizures. Workers suspected of having heat stroke should be moved to shady, cool, areas, wet down with cool water and cold cloths or ice around the body, and wet clothing with cold water. Lesser conditions include heat exhaustion, heat cramps, and heat rash, but all such conditions require treatment and should be taken seriously.
Heat stress is one of the main issues cited by the agency under Section 5(a)(1) of the Occupational Safety and Health Act—the “General Duty Clause” (GDC). The fines for willful violations can reach $70,000 per affected worker, and if a heat stress citation relates to a worker’s death, criminal sanctions can also be imposed on the employer. The GDC requires all employers to provide a workplace free from “recognized hazards” that cause or are likely to cause death or serious physical harm.
OSHA has posted examples of its enforcement actions for heat stress in construction:
In 2012, OSHA cited LH Mauser & Sons, a Maryland-based milling and paving company following a heat-related fatality, which occurred while a worker was paving a church parking lot in Washington, D.C. The violation involved failure to provide a program addressing heat hazards related to outdoor work in direct sunlight. The employer did not maintain a work/rest regimen, train employees on prevention of heat stress, or ensure that employees consumed adequate amounts of water. The company also was cited for failing to report the fatality to the agency within the required 8 hours (some “state plan” states have even more stringent reporting requirements than federal OSHA).
In 2013, a Pennsylvania roofing company, United States Roofing Corp., received the maximum OSHA penalty for exposing employees to heat hazards while engaged in roofing activities at a middle school. On the day of the inspection, the workers were in direct sun while the heat index was 105 degrees. The fact that they worked with hot tar magnified the hazards. As in the previous case, the employer was faulted for lack of a protective regimen and failure to train workers on precautionary measures against heat-related illness. Unlike some other GDC heat stress cases, no fatalities occurred, but the maximum penalty was still imposed.
[h3]HEAT STRESS MANAGEMENT[/h3]
OSHA promotes having a heat stress management program that includes: (1) a work/rest regimen that includes a provision to allow workers to become acclimated to extreme heat conditions; (2) scheduling outside work during the cooler portions of the day, where feasible; (3) providing cool water and encourage water consumption of 5 to 7 ounces every 15 to 20 minutes; and, (4) establishing a screening program to identify workers with health conditions aggravated by exposure to heat stress (some medications can also place workers at higher risk of heat-related illnesses). Moreover, all workers should receive training on heat stress prevention, including temporary workers that may be retained through employment agencies or union hiring halls. Training must be conducted in a language that workers can understand, and if work instructions are (for example) given in Spanish, then safety training must also be provided in that language.
There are other OSHA standards that can be cited relative to occupational heat exposure. The personal protective equipment standard, 29 CFR 1926.28 requires every employer to conduct a hazard assessment (which should be documented in writing) to determine the appropriate PPE to protect workers engaged in various tasks. There are many items on the market that can help cool workers, including headbands and work vests with cold packs. Employers can also provide controls, such as shaded areas, frequent rest breaks, or worker rotation. OSHA’s sanitation standard, 1926.51, also requires employers to provide potable water (safe for drinking). Heat stress illnesses that result in medical treatment, restricted work activity, or lost workdays must be recorded on the OSHA logs and failure to do so will result in citations under 29 CFR 1904.7. Lack of heat stress training can also be cited under 1926.21, the safety training and education standard for construction.
Some simple steps that can help reduce risks include reducing physical demands by using mechanical devices or assigning additional workers, monitoring weather reports, and rescheduling jobs with high heat exposures to cooler times of day, or postponing projects to cooler seasons if feasible, and monitoring workers who must wear PPE that can increase heat levels, such as Tyvek or rubber items, when outdoor temperatures exceed 70 degrees.
OSHA has launched a campaign to prevent heat stress illness and death, and more information can be found at www.osha.gov/heat. The agency also has a free application for mobile devices to enable workers and supervisors to monitor the heat index at their workplaces. It is available for both Android and iPhone devices and can be downloaded at www.osha.gov/heatapp. This summer, play it cool and keep workers safe!
■ ■ ■
[divider]
About the Author Adele L. Abrams, Esq., CMSP, is an attorney and safety professional who is president of the Law Office of Adele L. Abrams PC, a ten-attorney firm that represents employees in OSHA and MSHA matters nationwide. The firm also provides occupational safety and health consultation, training, and auditing services. For more information, visit www.safety-law.com.
Modern Contractor Solutions, MAY 2014
Did you enjoy this article?
Subscribe to the FREE Digital Edition of Modern Contractor Solutions Magazine!
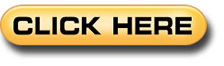