By Paul Bragan
Ground engaging tools are specially designed metal tools that are attached to excavators, loaders, bulldozers, and other earthmoving machines. This article examines how the market for ground engaging tools, the wearable metal attachments that make contact with the ground during construction and excavation, is changing rapidly as new manufacturing technologies evolve.
After spending six figures on earth-moving machinery like excavators and loaders, it is easy to view ground engaging tools as an afterthought. Wear and tear on earthmoving equipment is a substantial cost factor in both the construction and mining industries, and is particularly pertinent where machines have to handle abrasive materials. The most vulnerable parts of the equipment are those in direct contact with soil or mined materials, including, for example, dozer blades and bucket lips and corners. That’s where ground engaging tools (GET) play an understated, but vital, role.
GET have often been overlooked as a standardized ancillary item, but the market for these attachments is undergoing change as their value gains recognition. Wakefield Research estimates that the market is currently worth $1.1 billion and will reach $1.6 billion by 2024. It is not a new market, but advancements in the GET manufacturing process and the arrival of more high-quality, job-specific products is bringing about a welcome change for users.
GET vary in their size, shape, and purpose. The most prominent types are:
While the categories of GET are universally recognized, product quality can vary greatly. The lifespan and performance of GET are largely dependent on the manufacturing process, which involves either forging, casting, or fabrication.
Forging: Forged GET are the most durable. Made from chrome-moly alloy steel, the continuous fiber structure and grain flow of the steel offer high tensile strength while maintaining hardness and ductility. After forging, the tools are heat-treated for maximum wear and impact resistance.
Casting: Cast GET typically have a shorter lifespan than forged GET, but are still a viable, cost-effective alternative. Formed from medium-carbon, chromium, nickel, and molybdenum steel, they offer good resistance to abrasion and wear.
Fabrication: Fabricated GET generally have the shortest lifespan. They are made of two pieces, the blade and the clip. The blade encounters and penetrates soil more than the clip and is thus more prone to wear. It is made from chrome-nickel moly alloy steel and heat-treated for hardness.
While the manufacturing process is key to product lifespan, it is not the only consideration. Lifespans of GET can vary greatly even on the same site. Some standard bucket teeth may only last one week at mining sites, while they may last years at other sites. However, lifespans are typically measured in machine hours, and generally range from 400 to 4,000 hours. This is why GET are so important for users and why manufacturers and sellers of GET can achieve a real competitive advantage if their products reduce machine downtime. Given the frequency with which bucket teeth may have to be replaced, GET replacement strategies are crucial for budgeting as unexpected change-outs can result in costly downtime.
Aside from the manufacturing process, key factors influencing GET lifespan include:
Type of mined material: Abrasiveness has a high impact on how quickly a GET component wears out. For example, a gold mining site is generally the most abrasive, coal mining is the least, while copper and iron ore are in the middle range.
Terrain and climate; GET are likely to wear out faster on rocky terrain in humid climates than they would on soft soil in more temperate locations.
Operator skill: Technical mistakes made by machine operators can cause needless wear to GET, shortening the lifespan.
Depending on the above factors, it is important to choose GET carefully. Manufacturers and wholesalers offer a wide variety of GET types, and typically provide a warranty against breakage during the usable life of the item. Moreover, GET can be sourced from manufacturers of the machinery or from specialized companies that focus on GET production.
CLOSING THOUGHT
Competition in the market will increase as a positive construction outlook and advancements in tool design will see demand grow steadily over the next 5 years. This is good news for users and manufacturers. The greater visibility and quality of the products will benefit GET sales, while users can now make smarter decisions about their attachments to reduce machine downtime and improve overall performance.
about the author:
Paul Bragan is a senior partner at Wakefield Research. For more visit www.wakefieldresearch.com.
Modern Contractor Solutions, January 2020
Did you enjoy this article?
Subscribe to the FREE Digital Edition of Modern Contractor Solutions magazine.
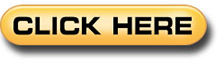