By Preston Ingalls
Equipment has rotating and reciprocating movement subject to friction. To minimize that friction and wear, grease is applied on a routine basis. But the field of greasing is a science—not an art. That science is called tribology.
THE ART OF GREASING
My favorite story about greasing goes back to the late 1800s.
A teamster, Francis Smith, affectionately known as “Borax Smith,” would always grease the hubs and axels of his wagons before launching off on a 160-mile trek through the desert carrying borax ore. Every trip, he religiously packed the hubs of the wagons with tallow (animal fat). Francis and his brother never had a single breakdown in their many years of hauling borax from Teel’s Marsh to Wadsworth, Nevada. What became known as the 20-mule team, pulling 30-ton loads, was a durable and reliable process (no wagon ever broke down in the many years starting in 1877 until it was replaced by rail in 1891). Think of those harsh conditions of the Mojave Desert heat and sand.
Smith attributed the 100-percent uptime and reliability to a mule, horse, and wagon care for its dependability. Francis had heard pioneers using tallow grease, thickened with ash, on the hubs of their Conestoga wagons on their long journeys cross country to minimize the friction of rotation. The practice had been around for centuries, dating back as early as Egyptian chariots.
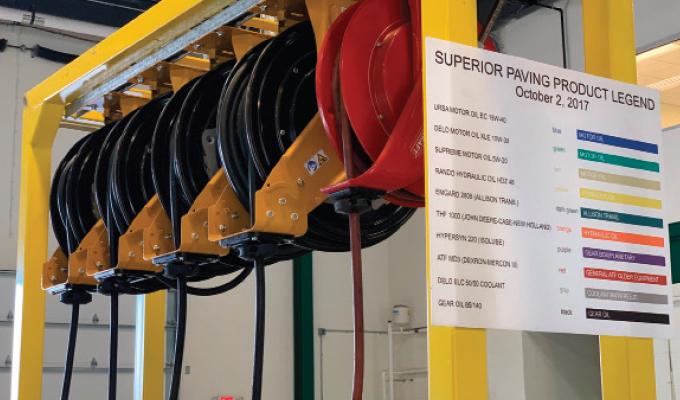
To minimize breakdowns, here are 20 techniques to help your lubricating efforts:
- Restrict the different types of grease guns by standardizing on one type and brand of the grease gun.
- Consider using a color-coding scheme, applied to oils and greases, from storage to fill to minimizes mistakes. Match the color from the bulk storage container to any fill container to the grease dispenser to the fill point. Color bands that snap around the grease gun can be purchased. Use a color code chart. (see example on next page)
- Wipe fittings before use to clear fitting of contaminants. Use a clean, lint-free cloth to avoid shedding cotton or poly fibers.
- Do not assume all fittings are in good shape. Inspect grease fitting and replace defective or damaged ones.
- Consider greasing at the end-of-day (EOD) because grease flows better when equipment and components are warm.
- For plant use with many grease applications over a wide area, consider using a foot pumper. They can be pulled and are foot-activated versus pumped by hand or arm swing.
- Slow strokes of grease guns (manual lever type) can minimize over-pressurizing seals. A manual lever grease gun can produce 10,000 to 15,000 psi, while many bearing seals can pop at 500 psi.
- Keep grease guns covered when not in use to avoid collecting contaminants.
- Avoid storing grease guns vertically because gravity will slowly cause the oil to leech out through the bottom of the grease gun.
- The amount of grease needed for a bearing is based on its dimensions and geometry. There is a common misunderstanding that excessive or over greasing helps to purge contaminants. The best approach is to apply the correct calculated amount at shorter time intervals. This helps to purge contaminants without over greasing.
- A new coupler sliding sleeve may possess a certain amount of resistance when trying to engage. It may require assistance to slide forward and lock onto the fitting. Just grip the sleeve and forcefully push it forward while wiggling it clockwise and counterclockwise with a slight rocking motion until it engages.
- Standardize on one model of the grease gun. Studies have shown that output between various models and types can range up to 600 to 700 percent. So, two shots of grease from one grease dispenser could be totally different than another.
- To avoid over greasing, use the natural “pressure feel.” This means inserting grease into the bearing cavity until you feel slight resistance or back pressure against the trigger or lever. This means it is full—so stop.
- Remember, you will have a turnover of personnel, so training will need to be an ongoing activity versus a one-time event. There will be many aspects to greasing that they will not know without proper instruction.
- Accompany the training with laminated visual standards, explained in the last section, to minimize misinterpretation or reliance on recall or memory. The key is to provide small “one-on-one” or “one-on few” instruction sessions on lubrication tasks.
- Consider using plastic caps on the coupler nozzle for storing to restrict contamination on the tip.
- To control contamination, repack grease gun on a clean bench or work surface using a gun loader fitting.
- When faced with removing the coupler from a pressurized fitting, it may be challenging to remove the coupler with just pressure from your thumb. To assist in depressing the thumb lever, use a pair of pliers on the thumb lever.
- Avoid over greasing electric motor bearings. Over greasing can cause the grease or oil to get into the windings, causing the insulation to weaken and deteriorate. This could lead to arcing and shorting inside the motor. The results are excessive heat and wear on the stator and rotor.
- Avoid laying grease guns down on dirty surfaces. Remember, grease is sticky, and contamination, like grit, will adhere to it.
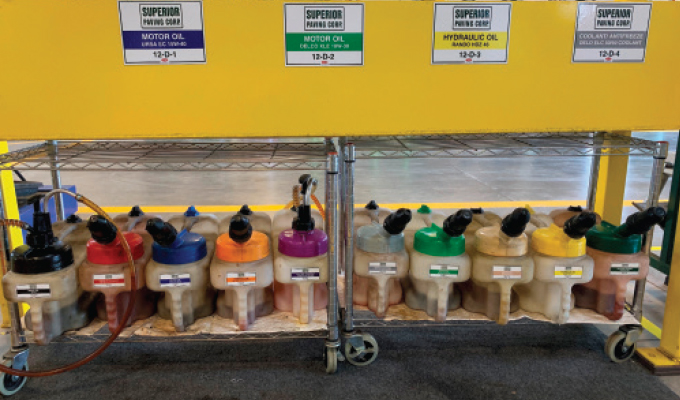
CLOSING THOUGHT
At the end of the day, you may not be stranded in the middle of the Mojave Desert, but you could be stranded on the side of the road. Consider improving the quality of your greasing efforts.
About the author:
Preston Ingalls is president and CEO of TBR Strategies, LLC, a Raleigh, North Carolina-based maintenance and reliability firm specializing in the construction and oil and gas industries. Preston can be reached at pingalls@tbr-strategies.com.
Modern Contractor Solutions, July 2020
Did you enjoy this article?
Subscribe to the FREE Digital Edition of Modern Contractor Solutions magazine.
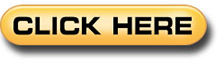