Site Masters specializes in laying asphalt for large commercial parking lots. Established as a true family business by Lee and Linda Mosley and their son Jeff in 2002 in Pheba, Mississippi, today the paving contractor’s service territory covers everything east of a line from about Fargo, North Dakota, down to West Texas.
During the construction and paving season’s peak, Site Masters employs 50 to 70 personnel who complete up to 14 projects a year, with anywhere from four to eight projects going on simultaneously. The company has about 70 pieces of equipment in its fleet to meet its customers’ needs. Site Masters had tended to favor one manufacturer in particular. Yet with the construction market coming back strong, the company purchased a couple Dynapac rigs after trying them out in late 2011: the Dynapac F1000T tracked paver and a Dynapac CC424HF tandem asphalt roller.
DYNAPAC PAVING LINE
The Dynapac F1000T Site Masters purchased is a rubber-track paver-finisher designed specifically for the North American market. It lays up to a 12-inch paving thickness of bituminous mixed material, roll-down or lean-mixed concrete. It will also manage track-laying ballast and unbound mineral aggregates for foundations for paving. One of the most unique benefits of the F1000T is the outboard auger drive and slat conveyor system that is designed to eliminate center line segregation.
The CC424HF is a 25,000-pound articulated drum roller whose design not only increases maneuverability but features enhanced operator view of the drum surfaces and edges, as well as the sprinkler nozzles.
After a month of using the equipment, Site Masters project manager Jeff Mosley was pleased with the Dynapac models and made the decision to buy the paver and one roller.
REVIEW FROM THE ROAD
Mosley says, “My operators really liked the rollers. They perform a little better. There’s a lot better visibility and greater ease of operation.”
The rigs had come with operator training from the store. Mosley says everything was familiar right away to those operators who already had a lot of experience. The main difference was that the control panel was entirely electronic, with capabilities for selection and monitoring of vibration and compaction modes. Mosley says, “They learned it fairly quickly. Some had no experience at all. We put them on it and gave them a crash course.”
John Givins, Site Masters crew chief for a job about 50 miles northwest of San Antonio, Texas, was on the F1000T running the screed. He preferred the rubber tracks to wheeled pavers for this job, which was on gravel. “It’s got power and traction. When we push up against the dump truck with wheels, they will sometimes dig holes. Not with tracks.” Today, though, they were loading the paver’s 207-cubic-foot-capacity hopper by a front-end loader and placing about 100 to 150 feet a load.
One selling point of the high-tech paver was that it wasn’t difficult for Givins or his driver to learn the rig, since it was not completely unfamiliar to them. Givins says, “It’s just like an older-style paver. Screed is pretty much the same. The paver is tracked but has a steering wheel. And it has electronics.”
Givins gave the Dynapac the edge on maintenance compared to other makes. “Time for maintenance is a little bit better. Takes about 30 minutes at the end of a shift. About 15 to 20 of that is greasing it and the rest is to clean off excess asphalt, as you would any machine. Accessibility to grease points is pretty fair, actually.”
QUALITY PERFORMANCE
Mosley says he’d had no problems at all with the equipment. The rigs are serviced to the recommended maintenance schedule. The CC424HF roller manuals have been updated to reflect the model’s increased service intervals. Longer time between servicing has further increased productive uptime. In the first 4 months, the rigs had already completed projects in five states, from Indiana down to Florida and Texas.
The contract for a truck stop and travel center project in Indiana required paving a 40,000-square-yard parking lot. Pavement was to consist of a 4- to 6-inch asphalt binder course with 2 inches of asphalt surface. The paver handled 20,000 tons of hot-mix asphalt for this project. Mosley says his crew averaged 2,200 tons per day, not only completing the project on time, but well exceeding the high-installation quality requirements that his customer had set. “We are amazed at the performance that we are able to get out of these machines on a day-to-day basis,” Mosley says.
In short, you could say that so far, throughout the U.S. east of the Rockies and in the expert hands of Site Masters’ crews, Dynapac’s paving line has made … a very good impression.■
About The Author:
Atlas Copco Road Construction Equipment is part of the Construction Technique business area. The division is a leader in asphalt and applications, committed to customer performance worldwide. Products and solutions are marketed under the Dynapac brand. Headquartered in Wardenburg, Germany, the division has production facilities in Europe, USA, South America, and Asia. For more information, visit www.dynapac.us.
_________________________________________________________________________
Modern Contractor Solutions, May 2013
Did you enjoy this article?
Subscribe to the FREE Digital Edition of Modern Contractor Solutions magazine.
Good Impressions
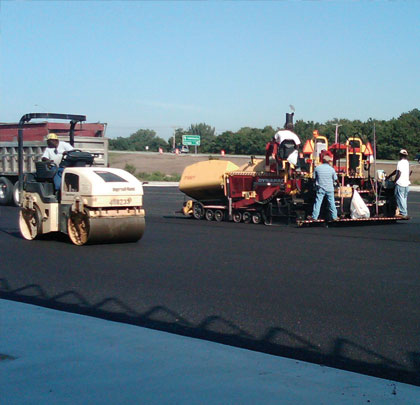