Improve jobsite safety with digital solution
By Kyle Slager
From lifting heavy objects to working on scaffolding 40 feet in the air, those who work out in the field subject themselves to a wide variety of hazardous physical conditions on a daily basis. Construction has consistently ranked as the industry with the most workplace associated fatalities in the United States year after year, even as machine safety mechanisms and protective equipment continue to improve.
Nearly all of these accidents are preventable. In fact, jobsite safety incidents are caused by seemingly harmless errors, like paperwork mixups, more often than people may realize. Going paperless will do more than streamline project efficiency—it can actually help save lives.
TOOLBOX TALKS
Toolbox talks help educate crews and increase jobsite safety. By teaching field teams about risks and hazards, they can avoid incidents and proactively create safer environments onsite. When a toolbox talk and sign-in sheet are printed on paper, it is harder to keep track of who attended the meeting and when the meeting was held. An employee could slip through the cracks and miss an important meeting about ladder safety or personal protective equipment (PPE) and end up making a fatal mistake.
Utilizing a digital toolbox talk system helps safety managers and superintendents maintain organized, searchable records without needing to hold onto paperwork from multiple projects. The ability to store information about project safety in one centralized location means it’s easier to find out which crew members have been informed on certain hazards.
DAILY DOCUMENTATION
Daily reports have always been used to keep track of a day’s progress onsite, but paper dailies have proven to be inefficient when it comes to the flow of communication. From missed reports to illegible handwriting, the traditional paper method of recording dailies gets pretty messy. If hazardous conditions are not included in one day’s report, a worker onsite could find themselves in a dangerous situation the next day.
With a system for mobile, digital daily reporting, site supervisors can instantly make notes of any abnormalities or risks they spot while they walk the jobsite. The faster an issue is reported, the faster it can be taken care of before anyone gets hurt.
PREVENT BACKLOG
When there are endless mountains of paperwork to sift through at the end of the day, it’s not uncommon for a project manager to get backlogged on documentation. Backlog can lead to miscommunications in the field and potentially cause fatal accidents. If an urgent alert about a dangerous situation onsite gets lost in the shuffle, mitigation falls by the wayside.
Field-focused tech improves safety through intuitive risk prevention methods, which includes improving workflows that used to cause major document backlog. Streamlining communication through digital reporting tools helps alleviate the burden of paperwork that has traditionally caused backlog, so hazards are handled quickly and efficiently.
CLOSING THOUGHT
It’s time to ditch paperwork in the field and move toward adopting digital solutions for safety management. The miscommunication and backlog created by paper document management can lead to greater risks on jobsites, less safety awareness, and more accidents. By going paperless, teams in the field can easily maintain organized accounts of risks and safety education to make sure that jobsites are as safe as possible.
About the author:
Kyle Slager is CEO and founder of Raken. Raken was created to help construction teams succeed and grow with robust insight from the field. The jobsite-focused field operations platform helps construction teams digitally manage manpower, progress, and safety, while providing robust insight for the office
Modern Contractor Solutions, January 2020
Did you enjoy this article?
Subscribe to the FREE Digital Edition of Modern Contractor Solutions magazine.
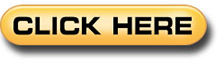