Portland cement, in addition to being a large user of energy in processing, is the second greenhouse gas contributor (CO2) in the world today. In many years, no advancements in concrete technology have optimized its usage or chemistry until recently.
CoolCure, developed by New Technology Solutions, LLC (a subsidiary of Silicone Solutions in Cuyahoga Falls, Ohio) is a major development that could potentially change the global environmental and productivity footprint of concrete technology.
CoolCure significantly reduces or eliminates the heat of hydration. While reducing heat, major increases in compressive strength and working and placement time are enabled.
CoolCure balances the chemistry and results in a more efficient reaction, creating more bonds that generate more strength. Increases in strength have realized from 40 to 100 percent. The heat is reduced by minimizing the calcium hydroxide byproduct generation. Its exotherm is well known in chemistry. The calcium hydroxide is better utilized by creating more CSH (reinforcing bonds) instead of creating troublesome heat.
CURRENT CONCRETE CLIMATE
Technology utilized in today’s mass pours of concrete (thermally managed concrete) makes the width of concrete greater than 3 ft, 10-inches thick and requires intensive cooling plans and processes that must be employed. This is due to the gross exotherm generated as calcium hydroxide forms and is wetted out during the cure, typically described as the heat of hydration. The exotherm expands the concrete during cure and cracks typically form when cooled.
Traditional cooling techniques employed in mass pours are unsuccessful at mitigating all of the heat management problems. Excessive energy is utilized for cooling in many pours for bridges, dams, facilities, and embankments. Concrete is often scrapped due to large cracks, as well as exceeding placement and maximum temperature designs.
Current technology utilizes silica fume and other silicas to increase strength. However, these silicas do not reduce the heat of hydration. Cure retarders are also well known to increase working time/delivery range. However, these do not increase strength or eliminate the excessive heat that causes so many problems. CoolCure combines these benefits and eliminates the problems.
Reduction of Portland usage is also often utilized to reduce exotherm; however, significant time (60-120 days) is required to attain full strength. Diluents like slag and fly ash are also often used to reduce the Portland level. Strength reductions, material shortages, and unsuccessful thermal plans result in many industry issues.
COOLCURE CONCRETE CLIMATE
CoolCure is ideal for large mass pours and can be implemented in existing cement mixing facilities and trucks. Its eco-friendly composition simply balances the chemical reactions and minimizes the by-product and resultant heat generation while simultaneously increasing compressive strength.
CoolCure also greatly reduces the potential for delayed alkali–silica reaction (ASR), which occurs whenever concrete pH exceeds 12.5 and some Portland is not fully wetted-out in the mix. Conventional concrete pH typically varies from 12.5 to 13.5, whereas CoolCure results in a pH of 12.4. In addition, CoolCure fully wets out the Portland. Reduced delayed ASR makes for longer usage life.
BENEFITS OF COOLCURE
CoolCure is 80 percent stronger over conventional concrete and creates more bonds through better wetting-out of Portland cement. CoolCure reduces shrinkage, internal stress, metal corrosion, and concrete porosity. With CoolCure, there is no thermal cracking or cold joints with multiple pours. CoolCure also improves freeze and thaw resistance.
There are also economic benefits for choosing CoolCure. Less Portland is needed with CoolCure, and it requires no cooling, resulting in lower-cost mass pours. The absence of thermal cracking eliminates the need to make crack repairs. There is no need to buy diluents like ash or slag, a reduced energy, and lower construction cost. In addition, no cooling or management plans are needed.
CoolCure is a much safer solution than Portland cement—which is caustic and can damage the skin. Workers in contact with wet Portland cement are at risk of chemical burns and developing skin problems. CoolCure does not burn the skin.
There is an environmental impact, too. Cement plants are a significant source of sulfur dioxide, nitrogen oxide, and carbon monoxide which are associated with a myriad of health and environmental impacts. Reducing the environmental footprint of Portland cement production/usage and meeting future emissions regulations is of paramount concern to all concrete producers.
CONCLUSION
The CoolCure chemical cure system represents attaining a higher level of technology in practice. While obtaining a progressive leap forward,
For more information:
For more information on CoolCure and New Technology Solutions, LLC, visit www.siliconesolutions.com.
Modern Contractor Solutions, December 2018
Did you enjoy this article?
Subscribe to the FREE Digital Edition of Modern Contractor Solutions magazine.
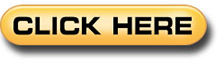