Part 2: Selecting The Right Crusher For An Operation
In last month’s feature, the first part of this article explained the differences between a jaw crusher, cone crusher, and horizontal impact crusher. The article also discussed why tons per hour are critical to calculate, and why it’s important to have a good grip on the application and materials the crusher will be used for.
Another factor that significantly impacts the crusher selection process is the number of end product specifications required. Is the operation producing and selling just one size of product, or are two, three, or even four different specs required? The number of screens available on a crusher unit will dictate the number of different size products a machine can produce in one pass.
Closed-circuit machines equipped with a two-deck screen can produce up to three different sizes of product. The top deck might be screening materials 2-inch minus, the bottom 1-inch minus, and the oversized material can either be fed back to the hopper for additional crushing or, with the installation of flop gates, can be kept for a third product for sale. Similarly, three-deck plants feature three screens and can produce and separate four different sizes.
TO MOVE OR NOT TO MOVE
Most contractors require highly mobile machines that are easily dismantled and moved from one site or job to another. Wheeled mobile crushers offer maximum convenience for transport. These units can be hooked up to a truck and hauled to different locations, meeting all DOT requirements. They can also be relocated on site with the help of a truck. These units are commonly self-contained, eliminating the need for additional diesel engines. While these units are compact and made to meet DOT regulations, they were also designed with maintenance in mind.
Tracked mobile crushers are ideally suited for applications that require movement within a jobsite as they can move under their own power. They are easily transported from one site to another by simply loading them on a trailer. However, the convenience of these machines comes with a cost. If an operator wishes to run multiple pieces—such as a screening plant and conveyors—they would need to also run three to five diesel engines, depending on the additional pieces. Further, because they’re built for constant relocation on a trailer, they’re more compact and lightweight than wheeled crushers, making maintenance more challenging.
DOT regulations are obviously a large factor of portable units. Due to the weight of portable units, operators transport the hopper feeder separately to meet weight regulations, which requires additional lifting and transporting equipment. A unit with a hydraulic system for the hopper can reduce the headache for the more mobile operators. The hydraulic power pack, designed for removal or installation in minutes, makes for convenient transportation and feeder setup by one person.
OVERALL DURABILITY
Crushing is demanding and grueling work and the machine must be durable enough to withstand the daily abuse. It’s accepted industry wide that operators who invest upfront in quality equipment and components save money in the long run by reducing the costs of upkeep and future maintenance. The crusher’s engine, hopper, and wear liners are just as important in ensuring the best fit and keeping maintenance to a minimum.
A powerful well-known engine is the backbone to a good crusher unit. Directly related to crushing, the horsepower ultimately dictates whether the engine will meet the operation’s output needs. Strong brand name engines provide a proven track record and the network required to ensure service and support when and where the contractor will need it.
Another main component, the hopper, should be sized to the operation. The hopper size dictates the amount of in-feed the machine can handle at one time. Although an oversized hopper doesn’t technically equate to a boost in production, it can accommodate larger equipment used to feed the unit.
Transfer points on a crusher endure a tremendous amount of wear and abuse. Some manufacturers have begun to offer AR-400 liners, which significantly increase durability and product life. Abrasion-resistant transfer points throughout the machine will provide extra strength, greatly reduce costly replacements, and prevent downtime.
A high-quality machine will feature additional designs that lessen or even eliminate maintenance. The quality of components, such as conveyors, bearings, rollers, shafts, and drives, are easily identified upon visual examination. The more robust designs will extend life and prevent failure. Take, for example, a crusher’s discharge chute. This area of the machine is under a lot of stress, and, as a result, requires regular maintenance. To eliminate extra costs, look for the specially designed discharge rock box. The specialized design uses a shelf system with an abrasion-resistant wear bar that allows crushed material to build up and act as a wear liner. The result is zero-maintenance, which translates to dramatic savings in labor and wear parts.
Clearly, there is no shortage of options to consider when selecting a mobile crusher. Fully evaluating the needs of an operation will help ensure the proper selection is made, meaning optimal usage of the right features, and resulting in the highest production possible. The goal for all operators is quality production at a low cost. Selecting the right machine makes each job easier and more profitable. ■
About The Author:
Sean Donaghy, IROCK Crushers national sales manager, has been in the crushing and screening industry for 24 years, 7 of which with IROCK Crushers. IROCK works towards being the market leader in wheeled crushing equipment with a focus on customer values. For more information, visit www.irockcrushers.com.
_________________________________________________________________________
Modern Contractor Solutions, April 2013
Did you enjoy this article?
Subscribe to the FREE Digital Edition of Modern Contractor Solutions magazine.
From Flintstone To Finesse
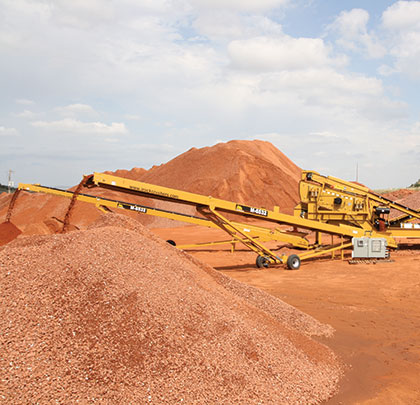