A backhoe on a rural jobsite was overheating. Unfortunately, no one realized it except the contractor—who was at another jobsite. The contractor had received a diagnostic alert and immediately contacted the site manager to stop the machine.
At the same time, the dealer also received the alert and called the contractor to schedule a tech. The alert’s diagnostic procedure let the tech know what was happening with the backhoe, so when he left for the site visit several hours away, he took the necessary parts with him and repaired the backhoe the first visit.
What made this extraordinary outcome possible? Telematics.
As part of an equipment manufacturer’s connected services, telematics gathers valuable fleet data, such as equipment location, engine hours and fault codes, and puts it in user hands. Easy access to this intelligence makes it possible for contractors and fleet managers to address a wide range of jobsite challenges and improve productivity, efficiency, and safety.
REDUCE UNPLANNED DOWNTIME
When contractors have a clear picture of fleet health, they can make decisions that keep machines running in peak condition. Using telematics, they can see when it’s time to schedule maintenance or address potential issues before they become critical. This proactive maintenance model can prevent failure and significantly reduce unplanned downtime.
Some telematics providers give operators a generated report on a periodic basis, while others have long refresh times. To address in-the-moment issues, it’s important to look for telematics that give operators access to machine data in near-real time, like CASE SiteWatch.
EMPOWER OPERATOR CONFIDENCE
As talent on the jobsite retires, new operators are stepping into machines that are growing more complex. Telematics helps bridge skills gaps by providing hip-pocket support with near-real-time fault codes, fuel and DEF levels, and more.
Site managers and fleet managers can also access dashboards and receive alerts and stop running machines if needed. Having multilevel visibility can help prevent issues and improve jobsite safety. It also allows contractors to know where machines are without tracking down the operator.
Some telematics, like CASE SiteWatch, provide access flexibility. Contractors can decide who can access machine data—and that includes their dealer.
SIMPLIFY FLEET MANAGEMENT
Depending on the size of the fleet and number of jobsites, refueling can be tough to coordinate. With telematics, fleet managers can see fuel and DEF levels for every machine, prioritize sites, and quickly plan an efficient route.
When fleets are large and spread across multiple jobsites, one-screen access to every machine can significantly simplify fleet management. Equipment that comes standard with telematics—rather than as an add-on or subscription charged per machine—can be advantageous for big fleets.
IMPROVEMENT BUILDS SUCCESS
Telematics only works if it draws out insights and guides users to actions that improve fleet operation, utilization, and efficiency. Dashboards should be easy to engage with and understand so users can achieve the outcomes that matter most. CASE co-developed its telematics solution with dealers and continually updates its dashboard and capabilities to make data more useful through a machine’s life.
CLOSING THOUGHT
The benefits telematics provide make it clear why it’s becoming an industry standard. In the field, on the road or in the office, telematics keeps contractors connected to their equipment and business.
About the Author:
Troy GeiTed Polzer, director, product and customer support, North America, with CASE Construction Equipment. For more, visit www.casece.com/northamerica/en-us.
Modern Contractor Solutions, July 2023
Did you enjoy this article?
Subscribe to the FREE Digital Edition of Modern Contractor Solutions magazine.
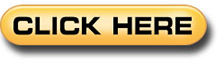