The impact of the pandemic, paired with lasting supply chain shortages and price fluctuations, dramatically add to the complexity of financial planning for increasingly advanced construction projects. The AGC 2022 Construction Hiring and Business Outlook reports concerning numbers—84% of contractors are reporting higher than anticipated costs and 72% are reporting longer than expected project lead times as a result of ongoing supply chain disruption.
And this in an industry with a low productivity growth rate of only 1% annually for the past two decades and with overall profitability remaining at about 5%. It is clear construction and engineering firms urgently need to rethink their project execution, control processes, and fiscal management strategies. Construction managers need real time and periodic project control processes that allow them to be proactive rather than reactive.
Control over all aspects of a project’s performance including cost, revenue, variations, risk and opportunity, cash, quality, planned deliverables, progress, safety, and compliance is necessary to meet client expectations and keep projects running on time, all while remaining profitable. Here solid management strategies reinforced with disruptive construction technologies will enable project managers to maintain complete financial control over even the most complex construction projects. From reactivity to proactivity—here’s how to take back control.
1. GET AHEAD OF THE GAME–ACTION OVER REACTION
The construction and engineering industry needs to redefine the meaning of project management. Effective project control is not just about measuring what has happened at each period end, it is being able to forecast where the project is heading to accurately predict the final cost, revenue and project margin, future cash requirements, and take early actions to mitigate project risk—essentially shifting from a reactive mindset to a proactive mindset.
Proactive management can be achieved with the integration of real-time data to provide project managers with a constant flow of information and the use of predictive analytics to foresee potential risks. This equips managers with the best tools and insights to act before it is needed and avoid unexpected delays and budget overruns. This in turn improves the reliability of construction projects and could help avoid project crises altogether. Better informed projects are more efficient ones, as greater insight means greater control.
2. LIMIT THE UNKNOWN WITH ONE VIEW OF THE TRUTH
Construction projects involve coordination of many business functions, suppliers, and subcontractors. Resources need to come together at the right time to keep projects on track so if you don’t have a joined-up view, the result will be resource shortages and reactive firefighting becomes the norm, not the exception. This is where managers need to set a standard practice for every process to ensure the same outcome is achieved each time. In short, a more integrated approach is needed where everyone is working to one standardized plan using the same shared data with one view of the truth. With these new processes in place, we can improve project delivery performance.
The standardization of operations reduces the element of uncertainty, increases the predictability of project delivery, and makes it easier to plan timelines, budgets, and forecast revenues and profits. It enables improved resource management, especially where supply chain disruption can significantly damage construction project progress. Standard practices create predictable project delivery outcomes and deliver high project performance, and ultimately profitable projects.
3. DUMP THE EXCEL SPREADSHEET–GO FOR PURPOSE-BUILT CONSTRUCTION SOFTWARE
Excel is certainly a useful office tool, but it was never designed to be the main business system to manage project processes such as contract management, variation control, project planning and control, risk management, and project cost control. For years the industry has been pushing spreadsheets beyond their suitability and in doing so, at the expense of the organization.
Excel spreadsheets are not designed for or specific enough for the complex nature of construction & engineering nor financial reporting and risk mitigation. Spreadsheets can contain high levels of inaccuracy and have limited functionality. With many formulas, data entry points and people accessing and editing one document the chances of errors occurring are very high—a recent survey found that as many as 90% of spreadsheets used by construction companies contain clinical errors. This creates a lack of visibility and an increased risk of making decisions based on information that is inaccurate and out of date, with the impact being poor project control.
Successful project management and control requires accurate and detailed real-time data to facilitate enhanced visibility and predictive analytics. Project monitoring cannot be maintained with multiple disconnected Excel spreadsheets. The level of accuracy, visibility, and control needed to manage complex construction projects requires a dedicated industry-specific software solution that can collate the many complex data sets involved in the management of largescale and high-stake construction projects into a reliable, single source of truth.
4. SIMPLIFY COMPLEXITY WITH ALL SYSTEMS AND TECHNOLOGY IN A SIMPLE SYSTEM ARCHITECTURE
As the complexity of projects and businesses grow, so too must the systems for project and financial management. As the adoption of new methods and techniques become necessary for businesses, new technologies will need to be integrated into existing operation systems. However, adding on different types of software technologies that are not designed to be integrated with one another through patchy API integrations can create a complicated web of disconnected tech, making it very difficult to manage systems and make necessary updates.
For this reason, construction firms should deploy a simple, purpose-built system architecture that is not only designed for the industry but will evolve with it. An effective system architecture should seamlessly integrate different technologies within it and allow functions and processes to evolve as the industry changes. This will future-proof construction and engineering businesses from the disruption of future digital transformation as technology continues to advance.
CLOSING THOUGHT
The steps outlined here are just starting points that address some of the key pain points in construction project management. However, gaining complete financial control requires more than adopting best practice processes and updating your system architecture. It takes a complete change in mindset and optimizing your entire business to focus on delivering projects on time, on budget, and at high quality—a shift to a data-driven, proactive management style.
About the Author:
Kenny Ingram is vice president of C&E at IFS. For more, visit www.ifs.com.
Modern Contractor Solutions, September 2022
Did you enjoy this article?
Subscribe to the FREE Digital Edition of Modern Contractor Solutions magazine.
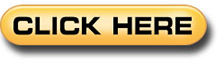