By Brian Bellile
Welding and repair work in the field can throw different challenges at you every day. When your truck is home base for tools and equipment and the work is in another spot or hard to reach, getting jobs done efficiently can be one of those challenges.
Your current welding setup may be driving several habits that you consider business as usual—but that are actually costing time and money and may be affecting quality. How do you know if you would benefit from a different welding solution? Ask yourself these questions:
1. ARE YOU “MAKING DO”?
Are you using weld parameters that are already set to avoid walking back to the machine to make changes? Your days on the jobsite are varied and so are the jobs you must complete. You likely need to switch between MIG, stick, and gouge, or dial in your arc control for different types of welds.
Most welding remotes have limited options for adjusting these parameters and processes, or you may not have a remote at all. It might seem more convenient to stay in your current workspace and make do with less-than-ideal parameters, but this can result in time and money spent on poor weld quality or rework.
Look for a remote that gives you full process and parameter control from wherever you’re working on the jobsite. With the ArcReach® Stick/TIG Remote from Miller, you can easily adjust amperage and arc control to fine tune arc characteristics—eliminating the need to walk back to make adjustments or make do with less-than-ideal parameters.
2. HOW LONG DOES YOUR WELDER/GENERATOR RUN?
When you get to a jobsite, do you turn your welder/generator on and let it run all day, turning it off only when you’re about to leave or during a break? While this seems convenient, you likely have periods when there is no load being applied and the welder/generator doesn’t need to run.
The average welder/generator is used about 30 percent of the time it’s running, meaning that up to 70 percent of the time it could be turned off. A machine that runs all day can quickly drive up your fuel costs and decrease time between maintenance cycles.
The new Remote Start/Stop on Bobcat™ 260 and 225 welder/generators from Miller lets you easily turn the machine on and off with the push of a button from wherever you’re working. With this capability, you can run your machine only when it’s needed and save up to $1,500 in fuel and maintenance costs per year compared to letting the machine idle while not in use.
3. DO YOU HAVE TO YELL TO BE HEARD ON THE JOBSITE?
When you get to the jobsite, there are often welders, generators, air compressors, and tools being used all around you. This may seem like business as usual and just part of the job, but all this additional noise can make it hard to communicate, especially if you need to take calls from customers.
And, on some jobsites, such as those in residential areas or near schools, reducing noise may be required to stay within local restrictions.
Just as turning the machine off helps save fuel, it also helps reduce noise on the jobsite. To help control noise, look for remote solutions that easily let you turn the machine on and off.
4. HOW MUCH ARE YOU SPENDING ON MAINTENANCE AND REPAIRS?
Maintenance is an important part of keeping your equipment running smoothly. But if you’re running your machine more than necessary or leaving it running out of convenience, you’ll significantly increase service intervals and end up doing maintenance more often than you need to.
This is time and money you could be spending on other things—not to mention the increased wear and tear on your machine from the additional run time. Turning the machine off remotely can reduce service intervals by up to two and a half times and save you up to $1,500 annually in fuel and maintenance.
CLOSING THOUGHT
New remote solutions give you more control over how much your welder/generator runs, how much fuel you use, how often maintenance is needed, and how much time you spend adjusting weld parameters. Look for remote technologies for your welder/generator that deliver more control right where you’re working—to help you improve efficiency and results in field welding and repairs.
About the author:
Brian Bellile is a product manager, engine drives, with Miller Electric Mfg. LLC. For more, visit www.millerwelds.com.
Modern Contractor Solutions, June 2020
Did you enjoy this article?
Subscribe to the FREE Digital Edition of Modern Contractor Solutions magazine.
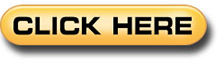