Complying with applicable OSHA standards for safety
By Michael Rubin, CSP and Kelly O’Connor
The duty to have fall protection in construction (OSHA section 1926.501) regularly tops the list of most frequently cited OSHA standards following workplace inspections. When it comes to the roofing industry, however, fall protection—though of paramount importance—is not the only requirement for an effective safety program. This article will address some critical considerations for roofers when it comes to ensuring compliance with applicable OSHA standards and, more generally, keeping their workers safe.
COMPLIANCE WITH PROVISIONS
In 2016, OSHA published its “Recommended Practices for Safety and Health Programs in Construction.” The seven core elements of the recommended practices include:
- management leadership
- worker participation
- hazard identification and assessment
- hazard prevention and control
- education and training
- program evaluation and improvement
- communication and coordination for employers on multi-employer worksites
OSHA’s description of these practices as “recommended” is not entirely accurate—indeed, many construction standards expressly require certain of these core elements. For example, OSHA section 1926.20(b)(2) requires that employers initiate and maintain a safety program which provides for “frequent and regular inspections of the jobsites, materials, and equipment” and that the inspections be conducted by “competent persons” (defined by OSHA as “a person who is capable of identifying existing and predictable hazards in the surroundings or working conditions which are unsanitary, hazardous, or dangerous to employees, and who has the authority to take prompt corrective measures to eliminate them.”) Furthermore, section 1926.21(b)(2) requires that employers “instruct each employee in the recognition and avoidance of unsafe conditions and the regulations applicable to his work environment to control or eliminate any hazards or other exposure to illness or injury.”
In short, roofers must (not should) implement an effective safety program to protect their workers—one that includes training, inspections, safety equipment, and (perhaps above all) an understanding and appreciation of the risks.
MORE THAN HARNESSES
When considering the risks associated with roofing work—including fall hazards occasioned by uneven sheathing, wind, loose roofing materials, and wet surfaces (just to name a few)—effective fall protection measures are critical. And, not to mention, OSHA requires them. But, before turning to address fall protection options, section 1926.501(a)(2) requires that employers assess the structural integrity of the work area. If any indications exist of compromised structural integrity, a competent person must evaluate the area to confirm the surface is safe. Next, an employer must select an acceptable fall protection system.
Section 1926.501 sets forth the general rule: guardrail systems, safety net systems, or personal fall arrest systems (PFAS) must be used to protect employees from falling 6 feet or more to a lower level. For roofing work, however, a distinction exists between low-slope and steep roofs. For steep roofs—having a slope greater than 4 inches of vertical rise for every 12 inches horizontal length (4:12)—1926.501(b)(11) follows the general rule but adds that any guardrail system must have toeboards to prevent any tools or equipment/debris from falling below.
For low-slope roofs (with a slope less than or equal to 4 in 12), section 1926.501(b)(10) provides more options: i) guardrail system, safety net system, or personal fall arrest system; ii) combination of a warning line system and any one of the preceding three [guardrail system, safety net system, or PFAS]; iii) warning line system and safety monitoring system; or iv) for roofs 50 feet or less in width, a safety monitoring system alone.
If an employer can demonstrate that it is infeasible or creates a greater hazard to use any of these systems, the employer must develop a fall protection plan which meets the requirements of section 1926.502(k). Notably, paragraph (k) identifies 10 requirements for a fall protection plan, including that the plan be prepared by a qualified person, document the reasons why conventional fall protection systems are infeasible, and describe the other measures that will be taken to reduce or eliminate fall hazards.
TRAINING AND RETRAINING
Section 1926.503 requires that employers provide training to all workers who might be exposed to fall hazards. In roofing, this very well could include everyone. Any training must be given by a competent person who is qualified in the following six areas: i) the nature of fall hazards in the work area; ii) the correct procedures for erecting, maintaining, disassembling, and inspecting the fall protection systems to be used; iii) the use and operation of guardrail systems, personal fall arrest systems, safety net systems, warning line systems, safety monitoring systems, controlled access zones, and other protection to be used; iv) the role of each employee in the safety monitoring system when the system is used; v) the limitations of the use of mechanical equipment during the performance of roofing work on low-sloped roofs; and vi) the correct procedures for the handling and storage of equipment and materials and the erection of overhead protection.
Employers are required to verify compliance with the training requirements by preparing a written certification record. Also, if an employer has reason to believe that an employee who has already been trained lacks the required understanding, retraining is necessary. This is not just an “attorney tip”—this is required under section 1926.503(c). As a result, while “unpreventable employee misconduct” can be a defense to an OSHA citation in certain situations, the argument that the employee was trained and should have followed the rules might not be so convincing (or valid) if the employer solely conducted new-hire training and there were clear indications that the employee needed to be retrained.
CLOSING THOUGHT
The above touches upon some—but not nearly all—of the important safety requirements for those in the construction roofing industry. Roofers are encouraged to invest significant time and effort to ensure their compliance with OSHA and protect their workers.
About the authors
Michael Rubin is chair of Goldberg Segalla’s national OSHA and Worksite Safety Practice Group. A Certified Safety Professional (CSP), Michael focuses his practice on issues involving occupational safety and health law. He can be reached at mrubin@goldbergsegalla.com.
Kelly O’Connor is a member of Goldberg Segalla’s OSHA and Worksite Safety Practice Group. OSHA 30 credentialed, Kelly focuses her practice on construction, workplace safety, and NYS Workers’ Compensation law. She can be reached at koconnor@goldbergsegalla.com.
Modern Contractor Solutions, August 2019
Did you enjoy this article?
Subscribe to the FREE Digital Edition of Modern Contractor Solutions magazine.
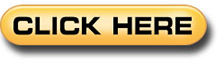