The Watts Reservoir was built by the Pueblo Board of Waterworks just outside of Pueblo, Colorado, in 1931 as a cast-in-place tank that measured 188 x 224 feet and covered over 42,000 square feet. The reservoir holds up to 5 million gallons of potable drinking water, which feeds the surrounding community, much of which continues to be heavily focused on farming and agriculture.
In the mid-1970’s, a roof was added to protect the reservoir’s use as a drinking source, which stood the test of time until 2021 when part of the roof collapsed into the reservoir. Held up by over 100 precast twin tees, corrosion caused the collapse, compromising the entire structure.
Industrial Constructors/Managers, Inc. (ICM) was asked to evaluate the issue since the company specializes in industrial construction, including heavy moving and rigging. We soon realized that extracting and replacing the roof would be no easy feat given its size and the fact that no one would be able to get underneath the roof given the dangers involved.
“Oddly, only one of the 100 precast tees failed, but that was enough to make the entire roof unsafe and capable of collapsing at any time,” says Dave Montoya, safety director for ICM. “Given that, we had to immediately start brainstorming to determine not just how to extract the roof but also replace it during the time allotted, which was within just a few months’ time so that the reservoir could be utilized in the summer months.
Working with Printz Engineering Services, ICM was able to quickly develop a one-of-a-kind rigging system to extract the damaged portion of the roof. A distinct fall protection and arrest plan was also built to help replace the roof, which provided 100% tie off for a span of over 200 feet in width, which was longer than ICM had ever accounted for.
“We’re known for ‘loving a challenge,’ and this project definitely lived up to that based on the sheer size of the tank and the roof’s unique dynamics,” says Montoya. “After putting our heads together, we developed a fall protection system that anchored independently from the reservoir so that we could safely stabilize the men while they extracted and replaced the roof.”
COLLABORATIVE BRAINSTORMING
Thankfully, ICM already had a freestanding fall protection system that had been designed in house for pre-engineered metal buildings, which served as a guidepost for developing the new system.
Using this as their model, ICM turned to Printz Engineering Services to help brainstorm some new ideas and ensure that these ideas would work on paper and in the real world. “We went into the project with a few possibilities, which were checked by Printz Engineering to ensure they made sense,” says Montoya. “This was critical given the inherent risks of the project and the fact that the roof would have to be extracted without an existing anchor in place to attach to.”
The resulting system consisted of two blocks of concrete that served as support anchors, which could be moved by a forklift as the project progressed. The blocks were tethered to a freestanding stanchion that was in the middle of the tank using a 200-foot cable that tied all three pieces together.
Two employees could be tethered to the system at any point in time, fastened using self-retracting lanyards. ICM ended up creating two separate fall protection systems to enable four workers to be working at the same time, helping to speed up the timeline.
“The system was designed so there was no swing fall exposure, and the maximum height anyone could free fall was 6 feet, with 2 feet being more likely,” says Montoya. “It was also developed to meet all of the existing requirements for 100% fall protection, including being mobile and capable of withstanding 5,000 pounds per employee.”
After a few weeks of pre-planning, the roof membrane was removed and the damaged twin tee was rigged out. 116 total panels were removed in just 2 weeks despite a number of rain, sleet and snow delays. ICM completed the roof removal 2 weeks ahead of schedule, causing the next phase of the project to be paused until the new twin tee material arrived.
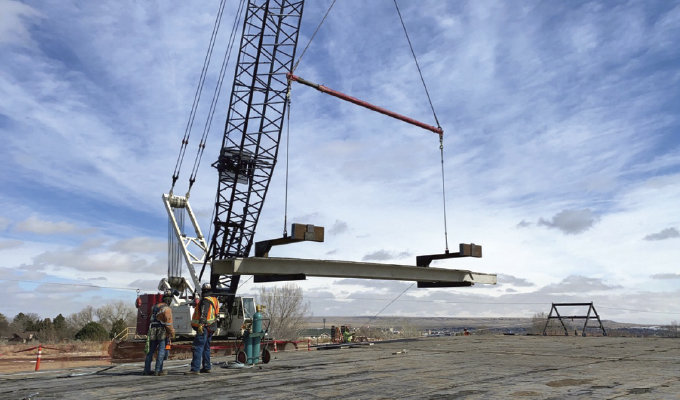
FALL PROTECTION SYSTEM
Not every project requires new thinking but should you run into a project that requires an outside-the-box fall protection solution, be sure to keep the following tips in mind:
Fact-check your ideas with engineers. While brainstorming is critical for unearthing new ideas, it’s important that ideas are grounded in reality, which requires testing them against calculations drafted by engineers. Use your engineers often and when any design change is made.
Up the safety factor when developing new systems. Having a new system in place means not everyone will be as familiar with it, making safety training and safety diligence all the more critical. For ICM, this translated to providing fall protection training to every jobsite employee and starting each day with a daily briefing to discuss top-line safety issues and doing daily site and equipment inspections during all phases of work.
Always be prepared for unexpected weather. The anchors were purposely built to sustain extremely high winds and wet conditions, which are common in Colorado in the winter and spring months. However, they would have been built the same way even if the project was undertaken in the summer given how unpredictable weather can be any time of year.
CLOSING THOUGHT
When a new challenge comes your way, be sure to brainstorm often, rely on your engineers, double down on safety and plan for the unexpected because it’s a guarantee that not everything will go according to plan. Taking risks usually opens up new thinking and generates innovative ideas, helping further differentiate you from the competition while also advancing the industry forward.
About the Author:
Devyn Novak is a project manager at Industrial Contractors/Managers, Inc (ICM), a Colorado-based industrial contractor specializing in steel and concrete structures, heavy moving and rigging, machinery installation, modification and maintenance, and more. For more, visit www.icminc.net.
Modern Contractor Solutions, February 2023
Did you enjoy this article?
Subscribe to the FREE Digital Edition of Modern Contractor Solutions magazine.
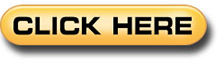