By Jason St. George
Whether storing heavy equipment and machinery, raw materials or finished products, it’s critical that valuable investments are protected. Among the most important decisions is choosing the storage construction material. While wood and metal are traditional options, when built correctly, a fabric-covered structure can be the best solution for protecting assets and investments for decades.
QUICK RETURN ON INVESTMENT
When thinking of building, a lengthy process involving concrete, brick, and rebar might come to mind. This is not the case with fabric structures, which can be built quickly in about half the time as traditional structures with more cost-effective materials. According to Visual Capitalist, over the past year, the price of lumber has increased by 377% in the United States – reaching a record high of $1,635 USD per board feet. Fabric provides an economical and durable alternative to expensive metal and wood construction. The material also lets more natural light filter through, helping to alleviate the expense of energy costs. Overall, fabric structures boast low operation and maintenance cost in comparison to traditional buildings, while offering a large, secure and well-ventilated storage solution.
ENGINEERED TO LAST
It might seem like common sense, but it’s important when building a fabric structure to work with a company that truly understands fabric. As a critical part of the investment, fabric that is fire resistant, able to withstand harsh weather, and treated for protection against the sun’s ultraviolet rays should be a basic expectation. Starting out with a high-quality fabric will help to prevent the fabric membrane from weakening or breaking down and add years to the fabric cover’s life.
There’s also an important step to be mindful of when it comes to protecting the metal framework of the structure for years to come. All steel trusses and truss components should be galvanized with a zinc coating to protect against corrosion. But it’s critical that the steel is coated inside and out. It’s a common misconception that all fabricated galvanized steel has an interior coating, when in fact most just have a coating of zinc rich paint applied to the outside. Hot dip galvanized steel should be the industry standard, as the dipping process covers the framing materials down to the smallest crevices, inside and out, to help maximize structural integrity and crate a tough barrier against corrosion. Not only does this help prevent the building from buckling from within, but the additional strength allows the structure to withstand high winds, temperature fluctuations, and heavy rain or snow falls.
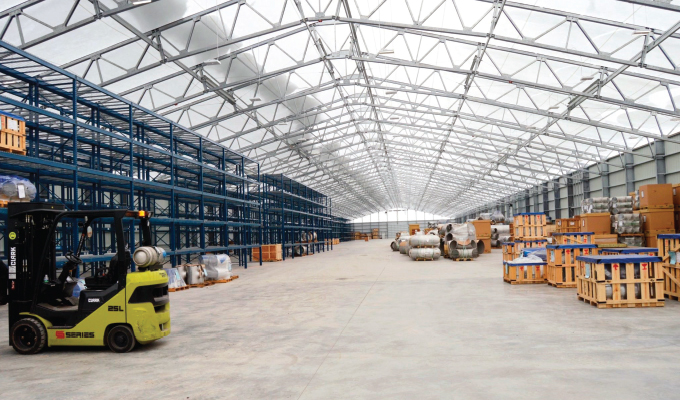
FULLY CUSTOMIZABLE
Fabric structures typically come in a variety of designs and configurations to choose from, allowing the structure to be custom engineered in any way that might be needed to accommodate bulk materials, overhead equipment, conveyors, catwalks, shipping and receiving equipment, and more. The various offerings of widths and heights offer ample clearance for easy access and movement so workers can safely and easily load, unload, and handle valuable assets. The flexibility also allows for a number of extra features, such as HVAC systems or insulation for complete climate control if needed.
Many fabric structures can also be built without any center poles, pillars or other interference, allowing for a nice clear span interior. This makes it easier and safer to maneuver trucks and machinery like cranes, conveyors, or catwalks that might be necessary when handling material assets. And depending on the fabric structure company, custom-engineered fabric structure can be as small as 16 feet wide to as large as 250 feet wide and built for any length.
Unlike other types of structures, fabric structures are scalable and able to grow alongside the business. And the structures can even be relocated to other locations if required.
Some fabric structure companies can offer site-specific customization for new buildings. Calhoun Super Structure, for example, uses a proprietary 3D Finite Nonlinear Analysis to model the true shape of fabric under load. The process considers the snow, rain, wind, and seismic conditions at the building site to offer an optimized foundation design to deliver the strongest building design for each unique location.
CLOSING THOUGHT
When it comes to selecting what type of storage building is right protecting valuable assets, fabric structures are a clear winner when it comes to ROI—especially when we consider the current cost of wood. But it’s critical to work with a company that specializes in fabric structures and has the engineering experience to back it up. When they do, contractors will benefit from a strong structure that can grow with them and their business for decades.
About the Author:
Troy Geisler is the vice president of sales and marketing for Talbert ManufacturingJason St. George is a business development manager with Calhoun Super Structure, a pioneer in the fabric structure industry with nearly 30 years creating the strongest, safest, and most reliable series of structures on the market. Located in Tara, Ontario, Canada, Calhoun values your investment. For more, visit calhounsuperstructure.com.
Modern Contractor Solutions, August 2021
Did you enjoy this article?
Subscribe to the FREE Digital Edition of Modern Contractor Solutions magazine.
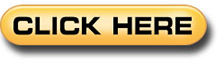