In late August 2012, a pair of Super 2100-2 pavers from Vögele was attaining astonishingly smooth placements of hot-mix asphalt on segments 5 and 6 of the new State Highway 130 central Texas toll route south of Austin. SH 130 recently received national attention when a top speed limit of 85 mph was permitted on these southern sections. Now open after a ribbon-cutting in late October 2012, the 41-mile toll route runs from I-10 just east of San Antonio to S.H. 45 on the south end of the Austin metro area.
SH 130 is Texas’ first concession agreement, representing a $1.3 billion private investment by the SH 130 Concession Company to build the remaining 41 miles of SH 130. Per the agreement, the SH 130 Concession Company, LLC provided the funds necessary to complete segments 5 and 6 of SH 130 from Austin to Seguin. It also will pay millions of dollars for right of way costs, thus lifting the financial burden from Caldwell, Guadalupe, and Travis counties.
SMOOTH REQUIREMENT
But America’s highest speed limit will require a supersmooth wearing course, and that’s where two Super 2100-2s with AB 600-2 TP2 screeds were doing their jobs.
“For the final course, we’re putting a Texas Type C aggregate mix with PG 76-22 binder,” says Luke Gries, quality control manager for Industrial Asphalt Inc., Austin, paving subcontractor for the prime contractor, Central Texas Highway Constructors. “Type C top size aggregate is 3/8-inch.”
The 2-inch wearing course mix was being placed by the two pavers in echelon. Bottom-dump trucks were placing two parallel windrows of hot-mix asphalt, which were being picked up by two material transfer vehicles, which fed the two pavers operating side-by-side.
“We’re using the pavers in echelon to get a hot joint between the two lanes,” Gries says. “The hot joint was specified by the owner and we are paving 40 feet wide, with a 22-foot pull outside and an 18-foot pull on the inside, including a 6-foot inside shoulder and 10-foot outside shoulder.”
Below the wearing course is a 7-inch-deep leveling course with ¾-inch top aggregate size and PG 64-22 binder. “On the upper end of the project, because of sulfates in the soil, that lift is 8 inches deep,” says Jerry Jaeger, field manager for Industrial Asphalt. Below that lift is a lime-treated stabilized subgrade of various depths, depending on the presence of deleterious materials.
The Super 2100-2s were getting extremely smooth placements, Jaeger says. Specs required an IRI of 60 or below, but the Vögele’s were well below that threshold. “I don’t think we would have got it with other pavers, but these Vögele pavers are getting 20s and 30s IRI [International Ride Index] readings,” Jaeger says. “I’ve seen that before with quarter-mile stretches, but we’re at 41 miles of continuous overlay. It’s exceptional.”
Smoothness was being augmented by the Vögele Niveltronic system utilizing 50-foot skis. Two skis were used on the 18-foot paver, and one on the 22-foot paver.
“We could not have gotten this level of smoothness without these pavers,” says Gary Doty, vice president, Central Texas Constructors LLC. “I have never seen anything like it. Just before we opened to traffic, a driver from Hennessy Performance attained 220 mph attempting to set a new land speed record for street-legal cars. He did not set the record as the car he wanted was not available, but said it was the smoothest pavement he’d ever driven.”
ELIMINATING ROLLERS
The compaction devices in the screeds were attaining such density—compared to other pavers that Industrial had used—that the contractor was able to eliminate three rollers from the compaction train. At the screed, on the coarse Type C wearing course, Industrial Asphalt was obtaining 88 to 90 percent density, with the breakdown roller taking it to 93, with a target of 91 to 95.
“You can see the density when you walk on it,” Jaeger says. “After a while, we were able to eliminate two breakdown rollers and a finish roller. Any time you are able to drop equipment you save on diesel fuel, labor, and wear-and-tear.” When visited, for the two pavers, Industrial Asphalt was using two breakdown rollers and three pneumatic rollers.
“I like these pavers,” Jaeger says, “especially for interstate work. We can pull two lanes at once, which we don’t normally do. We’re doing 4,000 tons per day, 16 feet per minute. ■
About The Author:
Tom Kuennen is principal of ExpresswaysOnline.com in suburban Chicago, where he plays a lead role in construction and industrial writing for trade journals, corporations and national associations, photography, Internet concept and writing, and publication launches. He can be reached at expwys@expresswaysonline.com.
_________________________________________________________________________
Modern Contractor Solutions, July 2013
Did you enjoy this article?
Subscribe to the FREE Digital Edition of Modern Contractor Solutions magazine.
Exceptional Surface: Pavers create supersmooth pavement on Texas highway
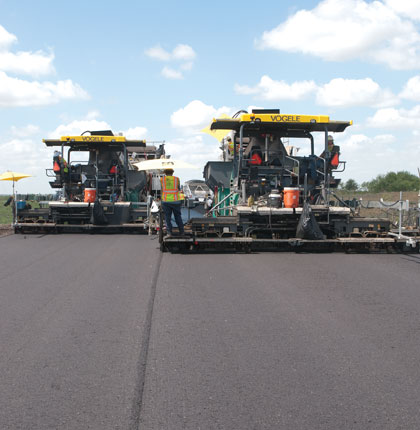