Chicago, Illinois-based Pan-Oceanic Construction is in the midst of upgrading the sanitary sewer system on the city’s Lower West Side along West Cermak Road and West 18th Street. Pan-Oceanic is adding four new junction chambers to connect 54-inch RCP sewer pipe, plus many other upgrades; all in the effort to relieve the large amount of flow passing through the aging, existing sewer system.
Any type of excavation project in a heavily urban area is fraught with challenges; even more so when dealing with original infrastructure that may be centuries old. In order to install new sewer pipe and structures, a contractor may need to excavate and work around existing utilities that are currently active, but also utilities that may have been inactive for decades.
Adding to the difficulty of the excavating project, contractors must assure that workers in the excavation are kept safe at all times. That means having the proper shoring system in place. However, traditional shoring systems, such as trench sloping or trench boxes, may not be possible when the working pit looks like a bowl of spaghetti of crossing pipes and conduits.
Pan-Oceanic needed a non-traditional shoring system for this project, something designed specifically to shore around crossing utilities and existing structures.
CROSS-TRENCH UTILITY SHORING SYSTEM
Through the bidding process, Pan-Oceanic connected with Efficiency Shoring & Supply, one of the leading trench shielding and shoring supplier in the Chicago area. “It was simple, really,” says Blake Stevens, Efficiency Shoring & Supply’s shoring specialist. “There are very few shoring systems that are designed to handle multiple crossing utilities, and we suggested the best—a Shore-Trak™ Cross-Trench Utility Shoring System manufactured by Efficiency Production.”
Shore-Trak consists of a series of sheeting guide frames that sit level on the ground or in an excavated pilot hole and connect together in a four-sided configuration typically by sliding the ends of the guide frames into Slide Rail System corner posts; or, as Pan-Oceanic did it, connecting the guide frames with specially designed corner brackets that pin over spreader collars welded onto both ends of the guide frame. In this configuration, Slide Rail posts are not used, which simplified installation.
Next, KD-6 sheeting is stood up and overlapped in the 7-inch slot in the guide frame, and then the individual 18-inch-wide sheets are pushed individually to grade which allows the sheeting to closely shore around any crossing pipes, conduits, or other utilities.
“Compared to H-Beam and Lagging, the Efficiency Shore-Trak was faster to put in and there was also a cost savings,” says Pan-Oceanic’s project superintendent, Erik Kohman. “Overall, the Shore-Trak worked pretty well; I liked it. And we got great service from Blake and (Chicago Branch Manager) Mark Mitchell at Efficiency Shoring,” Kohman adds.
DIFFICULT EXCAVATION SPOT HANDLED
At one particularly difficult excavation location—at the intersection of Cermak Road and Hoyne Avenue—Pan-Oceanic needed to dig down 19 feet and expose a 9-foot-diameter brick sanitary sewer pipe, which has been in use since 1844. Once uncovered, the sewer pipe was cut open horizontally for 30 feet and a new concrete personnel-access junction chamber poured-in-place over the exposed brick sewer pipe and connecting pipe running into the junction chamber from a 45-degree angle from the northeast.
The entire working pit was 36 feet by 26 feet, and needed to be dug to 19 feet deep. However, at 15 feet deep, Pan-Oceanic hit bedrock which prevented them from driving the sheets to the complete depth. At that point, Stevens called in assistance from Efficiency Production’s Special Operations Shoring Division who sent out senior slide rail installer Rod Austin.
“When the contractor hit bedrock, we needed to pause and reassess the engineering for the shoring system,” explains Austin. “What we decided to do was weld i-beam walers across the sheeting at about 15 feet—the depth the contractor hit bedrock—which basically prevented the sheeting from kicking in to the open excavation,” he says. “Then the contractor could chisel out the bedrock to the required depth for them to pour the structure,” Austin concludes.
“The system worked perfectly, no problems at all,” says Marty Mele, Pan-Oceanic’s general superintendent who oversaw the installation of the shoring system. “If it didn’t work great, we wouldn’t use it again,” he insists. “And we’re using it again.” ■
Editor’s Note: Efficiency Production’s vaunted Special Operations Shoring Division is staffed by the nation’s most experienced team of slide rail experts and installers. The division’s goal is to act as an extension of a contractor’s estimating department or rental operations, including: reviewing project plans and selection of shoring equipment, providing written quotation and requested submittals, providing P.E. stamped 3D submittal and proposal drawings, as well as offering pre-construction on-site consultation and special engineering.
About The Author:
James McRay is the director of marketing and media for Efficiency Production, Inc. He can be reached at 800.552.8800 or jmcray@efficiencyproduction.com. Efficiency Production, Inc., “America’s Trench Box Builder™,” provides the widest selection of standard and custom trench shielding and shoring systems in the industry. www.efficiencyproduction.com.
_________________________________________________________________________
Modern Contractor Solutions, April 2015
Did you enjoy this article?
Subscribe to the FREE Digital Edition of Modern Contractor Solutions magazine.
Excavating The Past
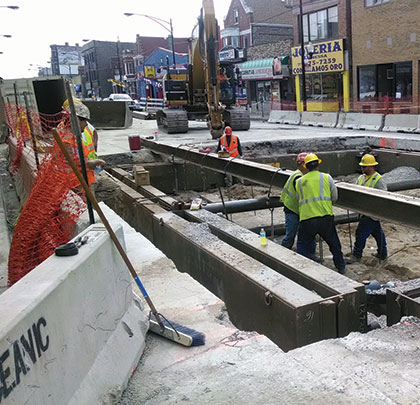