By Raghi Iyengar
Estimating and bidding go hand-in-hand. It’s the previous job experience that informs the resume. The ingredients that make up the recipe.
To have a successful, best-in-class bid, you first must have the needed insight from data you can trust to create the well-rounded, accurate result that keeps people coming back for more, not unlike a family-secret recipe for cherry cobbler that you guard for your life. No one can steal your secret sauce when you realize that estimating is both a science and art that truly informs the bid.
The scientific component of estimating includes determining the precise quantities needed for each material. For those contractors ready to optimize processes, this most likely includes utilizing technology to develop a Building Information Modeling (BIM) model and automate the quantity takeoff function.
The art of estimating goes far beyond quantities. It means including logistics, crew, and time estimates that factor potential difficulties, risks, and waste into decisions, painting a complete picture of what the project might look like far beyond just materials. This art form is what sets apart the estimating experts from the pack, resulting in more winning bids.
After combining the science and art components of estimating, contractors can feel assured they are submitting accurate estimates that will deliver on time and budget, including potential external factors with the easy-to-determine quantity numbers.
IMPROVING WITH TECH
Historically, contractors completed the estimating and bidding processes within spreadsheets, submitting bids in Excel. Traditional estimating software includes variations of spreadsheets disconnected from actual work performed. It’s high time this was disrupted, and new technology is here to evolve these processes, helping to make estimates more precise and saving teams time and resources.
Similarly, contractors can utilize this technology to review findings and data from similar past projects, meaning they’re not starting from scratch with every estimate. This also helps better inform the understanding of potential risks based on actual data. And it provides visibility that impacts the construction site layout. At the same time, teams can save time, all thanks to the wealth of historical information from previous and current projects.
In turn, all of this is making the industry interesting as we effectively industrialize construction by leveraging AI and simulation to support better decision-making.
TECHNOLOGY EVOLUTION
Offsite construction software remains the top-tier option for the industry in industrializing the construction process. This technology can provide real-time insights, visibility, and control into who is building what components, assemblies and modules, and where and when for the largest construction projects.
These end-to-end construction technology platforms allow you to look at buildings from the product perspective. It informs time and costs estimates while also providing insight into relationships between specific suppliers and manufacturers to give better estimates. At the same time, it helps further establish supply chain relationships where it is beneficial.
For example, the industry can rely on machine learning to make sense of all the data presented and identify trends and lessons learned across previous projects to reduce and identify risk factors, providing a much richer data set that truly optimizes decision-making.
And, when this technology is paired with visual intelligence (VI) software, things become even more intuitive. VI technology, in the context of digital twins, provides an immersive experience powered by AI for complete visibility into products, processes, people, and more.
CLOSING THOUGHT
Technology is truly revolutionizing the construction industry starting from the very beginning: estimating. And, as the fourth Industrial Revolution becomes more real for the industry, it’s time we think about how technology can evolve and improve the industry, elevating the role of our teams while also equipping the sector to make construction projects faster, cheaper, better, and greener.
About the author:
Raghi Iyengar is the president of Manufacton, a SaaS (mobile/web) platform that helps construction firms plan, track, and manage both prefabrication and regular material handling. For more, visit www.manufacton.com.
Modern Contractor Solutions, July 2021
Did you enjoy this article?
Subscribe to the FREE Digital Edition of Modern Contractor Solutions magazine.
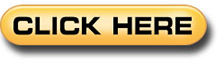