By John Kane
Mechanics are among the most valuable employees at construction companies that operate heavy equipment. Adding software capabilities that are powerful, easy to use and mobile to their toolboxes is emerging as a high-ROI option for maximizing their efficiency.
The essential work mechanics do, their relatively high compensation and difficulties of finding, training, and replacing them make it imperative for executives and managers to focus on increasing “wrench time”—the time spent actually servicing equipment, as opposed to getting to where it is and doing administrative work.
Poor scheduling and excessive time spent preparing work orders and traveling are the leading threats to the efficiency of mechanics. Maintenance management software drives significant improvements in all three areas. Linking that Computerized Maintenance Management System (CMMS) with a real-time, online application for resource scheduling and dispatching can compound the efficiency gains.
MORE WRENCH TIME
There are two main challenges with scheduling mechanics. The first is planning preventive maintenance (PM) in an organized and orderly manner. Without an automated software solution, PM is typically scheduled on a catch-as-catch-can basis. Service intervals tend to sneak up on mechanics and managers, and work gets assigned at the last minute. This can result in mechanics scurrying around in a very inefficient manner.
With maintenance software, each piece of equipment is set up with a PM schedule that is tied to meter readings, dates, or both. Shop managers get automatic alerts for impending requirements. They can even determine how far in advance they want to receive the notices. Seeing well ahead of time the upcoming PM work that needs to be performed allows them to schedule it for optimum mechanic efficiency. Also, when a mechanic is sent to a worksite to perform emergency repairs, the software can identify other equipment on the site or nearby that will require PM in the near future, so a mechanic could do it in advance and get it out of the way while he or she is already there.
The second scheduling challenge involves people. Even when a manager knows exactly what repair work is coming up, scheduling the assignments of multiple mechanics on paper, whiteboards or spreadsheets is ineffective. Requirements change continuously and often suddenly. With maintenance software, assignments can be created and modified with drag-and-drop simplicity on an easy-to-follow grid. Importantly, that schedule, including up-to-the-minute updates, can be visible across the organization and on mobile devices.
The next time sink for maintenance teams is preparation of work orders. In a manual environment, the mechanic typically takes a standard form and fills it in by hand. Beyond the writing or typing time, they also have to think of what work needs to be performed and which parts are required. This is time consuming and it results in inconsistent PM.
Maintenance management software systems, by contrast, can be set up to generate standard work orders. A mechanic enters the PM or emergency repair that needs to be performed, and the system automatically generates an electronic work order that can then be modified if necessary. This can be done on a desktop or mobile device.
Software can also cut down the administrative time mechanics spend entering their hours manually on paper timecards or stand-alone systems. Automated processes can systematically create a “timecard” based on hours added to a work order.
LESS WINDSHIELD TIME
Most larger or mid-size heavy construction companies have multiple jobsites over a wide geographic footprint. Mechanics can spend a lot of time driving to various sites to perform work. Software-assisted capabilities like scheduling PM work and assignments more efficiently and performing upcoming work on multiple assets in advance to eliminate return trips to the same site can reduce some of this “windshield time.”
Inaccurate knowledge of equipment location is another cause of excessive windshield time. A mechanic driving an hour or two and finding out that the piece of equipment they are scheduled to work on is no longer at that worksite is not unusual. Visibility into maintenance and resource scheduling applications greatly reduces the chances of this occurring. GPS tracking in one or both of those applications virtually eliminates it.
Equipment maintenance and resource scheduling software that works in concert provides contractors with a final advantage when it comes to efficiency. Schedulers and dispatchers, by seeing the upcoming maintenance requirements, can plan equipment assignments and moves around that schedule. Likewise, maintenance managers can coordinate repair work, when possible, at times that will least disrupt production.
Heavy equipment mechanics are extremely important resources. Their efficiency is critical to getting preventive maintenance and emergency repairs performed in a timely and cost-effective manner. They are also hard to come by and retain, especially in the current labor market.
CLOSING THOUGHT
Supporting mechanics with the software capabilities outlined above can optimize their time and job satisfaction while also reducing maintenance costs and equipment downtime. In some cases, using software technology to cut “windshield time” and increase “wrench time” could even reduce the number of mechanics a company requires.
About the Author:
John Kane is a product manager for B2W Software. He has had a leadership role in the development of the company’s specialized B2W Maintain application for equipment maintenance and repairs. John has more than 15 years of project management, program management, technical data analysis, and troubleshooting and reporting experience. He can be reached at jkane@b2wsoftware.com. For more, visit www.b2wsoftware.com/products/construction-equipment-maintenance-software.
Modern Contractor Solutions, November 2021
Did you enjoy this article?
Subscribe to the FREE Digital Edition of Modern Contractor Solutions magazine.
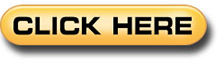