On July 12, 2019, cracks appeared on the eastbound lanes of U.S. 36 between Wadsworth and Church Ranch Boulevards, a heavily trafficked thoroughfare that connects Boulder with Denver, Colorado. The cracks soon gave way to a full-blown sinkhole, according to a Colorado Department of Transportation (CDOT) press release. While fortunately no one was hurt in the collapse, significant damage led to the partial closure of U.S. 36.
SECURING FILL OPTION
In order to rebuild the damaged roadway as quickly and safely as possible, CDOT and its design team, which consisted of RJ Engineering and Consulting, Inc. and David Evans and Associates, Inc., conceptually developed a lightweight geofoam fill option to replace the wall. Based on other successful geofoam projects that Ben Arndt of RJ Engineering had designed for CDOT in the past, Arndt suggested a geofoam fill to meet the timeline requests from CDOT. CDOT awarded the contractor portion of the project to Kraemer North America to rebuild the roadway section. Kraemer North America looked to Insulfoam’s Geofoam EPS22 product to meet CDOT’s requirements. Based on press releases from CDOT, the expanded polystyrene (EPS) geo-synthetic fill is “very strong, which means it can safely support highway loading and also lead to improved slope stability. Of the different options considered, (…) (EPS geofoam) provides the best factor of safety.” Matt Hogan, project manager for Kraemer, further explains, with EPS “geofoam, we could fabricate quickly and not need all the deep foundation work to support the load of the new wall system.”
Working within a tight deadline to get the roadway open and fully operational, it was all hands-on deck at Insulfoam to manufacture more than 6,100 eight-foot blocks of material fill. Six multi-operational manufacturing plants in Aurora, Colorado; Mead, Nebraska; Phoenix, Arizona; Lakeland, Florida; Puyallup, Washington; and Dixon, California, rallied to meet this great need and pull the freight numbers together, says Kris Essex, territory sales manager for Insulfoam in Colorado. The plants also remained fully operational, conducting regular business. Essex continues: “This was a great opportunity to work as a team on the production side. We went from 0 to 100 mph in an instant.”
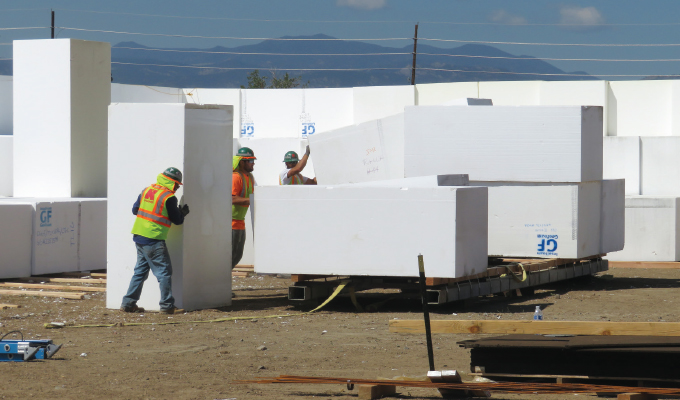
WORKING AGAINST TIME
Hogan also cites timing as a critical factor: “Being able to use six different plants across the country helped. We were able to find, honestly, the fastest producer to be able to meet the needs of this particular project.”
Unprecedented in scope, Insulfoam’s large-scale, multi-site effort was necessary to meet CDOT’s October 2019 reopening deadline. Additional time-savings came from the manufacturer’s ability to create 40-inch x 48-inch x 96-inch customized EPS geofoam to meet CDOT’s exact requirements. These large block sizes can be produced to fill huge voids, saving crucial time and labor on the Colorado jobsite. What’s more, should a block’s dimensions need to be adjusted for any reason, road building teams can quickly and easily cut EPS geofoam to the proper size with hot wire tooling or saws. EPS geofoam further saves construction schedules by taking surcharging and preloading out of the equation, freeing crews up to focus on other tasks.
INSTALLATION SAVES TIME
For Hogan and his team, the ease of installation was particularly noteworthy. With Insulfoam’s EPS geofoam, “The nice part is being able to train people quickly, because it’s literally stacking blocks. We’re able to slide the foam right into place, (add) a little bit of detail on the edges, (identify) out-of-line blocks, and slide them into place. Once you get the material up on top of that foam, it slides relatively easy, and it’s able to go right in,” Hogan says. “We couldn’t be happier with the simplicity of how to install the foam.”
Long term, CDOT also stands to benefit on both the time- and cost-saving fronts, as EPS geofoam requires minimal to no maintenance for the duration of the fill system’s life.
GEOFOAM BENEFITS
EPS geofoam’s physical properties also lent themselves well to rebuilding the major highway. Controlled during manufacturing, the fill’s typical densities range from 0.70 to 2.85 lb/ft3. As a result, EPS geofoam is significantly lighter than soil (approximately 120 lb/ft3). It’s so light, in fact, that the material almost completely eliminates the need for heavy earth moving and compaction equipment during void fill.
According to the EPS Industry Alliance, EPS geofoam’s lighter load decreases stress, while sidestepping deformation-related construction problems. Or, as CDOT put it in a U.S. 36 Weekly Update, “since geofoam is lightweight, it reduces pressure and stress to the underlying soil.”
The geo-synthetic fill also consists of blocks that are uniform. However, this is not the case with soil and other fill materials, whose variable, inconsistent compositions can lead to non-uniform load transfer and differential settlement. This type of settlement can cause dangerous, uneven structure settling and lead to further damage. On the other hand, EPS geofoam uniquely disburses or spreads the load out across a wide area, minimizing post-construction settling and creating a more stable foundation.
CLOSING THOUGHT
As Essex explains, “Insulfoam’s (EPS) geofoam is a stable compound right away, as you can engineer the right density. There’s settlement compaction with soil, and there’s not time for that with the main U.S. 36 thoroughfare currently closed down.”
In just 20 days, six Insulfoam plants manufactured and coordinated logistics for more than 200 truckloads of EPS geofoam during the busiest month of the year, helping CDOT’s emergency road repair stay on track.
For More Information
For more about this project, visit www.insulfoam.com/US-36.
Modern Contractor Solutions, March 2020
Did you enjoy this article?
Subscribe to the FREE Digital Edition of Modern Contractor Solutions magazine.
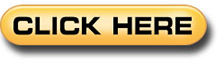