A recent research study by Coyote Logistics, “Sustainable Supply Chain Management: Driving a Smarter, More Sustainable Future,” found that 81% of companies are more focused on sustainability today than they were 3 years ago. Corporations are under pressure to operate more efficiently, spurring growth in sustainable warehousing/distribution centers. With consumer interest in green practice growing, businesses are evaluating everything from packaging to transportation of goods to optimization of warehouse space. One less obvious way to reduce their carbon footprint is by replacing a traditional concrete slab floor with a DUCTILCRETE® engineered slab system.
These systems significantly reduce their environmental impact through the use of more sustainable materials. For example, when a Cincinnati-based auto parts manufacturer wanted a 154,000-foot plant expansion, they used a DUCTILCRETE engineered slab instead of conventional concrete for the floor. These specially engineered systems usually require less concrete than traditional slabs, while maintaining the same strength or higher. On this project alone, the contractor was able to reduce the amount of concrete needed by more than 1,914 cubic yards, resulting in a savings of nearly $200,000—and a reduction in an estimated 600 tons of CO2 emissions.
RETHINKING FACILITY DESIGN
Historically, warehouses and manufacturing facilities were built with traditional concrete slabs. The manufacture of cement is tough on the environment, according to the EPA, emitting roughly 0.9 pounds of C02 into the atmosphere for every pound of cement produced. A batch of concrete is made up of roughly 7-15% cement. This means that manufacturing just one cubic yard of concrete results in 400 lbs of CO2 going into the atmosphere.
Installing a DUCTILCRETE engineered slab significantly lowers this environmental impact in a number of ways.
Reducing the floor profile cuts the amount of concrete used.
DUCTILCRETE engineered slabs typically only require a 6-inch slab, compared to a conventionally designed 7-inchconcrete slab. Using a DUCTILCRETE system for a one million square foot warehouse could potentially eliminate the release of roughly 1.2 million pounds of CO2 into the atmosphere. A reduction in profile thickness also results in less aggregate used in the concrete and fewer trucks (i.e., less fuel consumed) to deliver concrete to the jobsite.
Replacing steel reinforcement with macro fibers.
DUCTILCRETE engineered slabs use macro-synthetic fibers to strengthen the concrete as opposed to traditional reinforced steel. This is another way to lessen the environmental impact of the floor. A study by the University of Akron in Ohio evaluated the impact of replacing conventional steel rebar with fiber reinforcement in a 150,000 ft2 concrete floor and found this could reduce the carbon footprint by 56%.
CLOSING THOUGHT
Since there are far fewer joints and fewer resulting joint problems with a DUCTILCRETE engineered slab system, there is much less need for epoxies and other joint filling materials, which can contain harmful chemicals.
About the Author:
Jorge Garcia is the director of the Ductilcrete business within GCP. Dedicated to the end-user, he is passionate about creating a positive customer experience that highlights the benefits of the company offering. Jorge has over two decades of experience in the concrete construction industry. A strong believer in the power of positive thinking in the workplace, Jorge is proud to contribute to improved efficiency and satisfaction company-wide. For more, visit gcpat.com.
Modern Contractor Solutions, May 2022
Did you enjoy this article?
Subscribe to the FREE Digital Edition of Modern Contractor Solutions magazine.
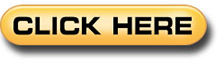