By Sarah Colley
Construction and technology aren’t exactly synonymous. It’s an industry known for its ruggedness and continued grasp on a perceptively “old-fashioned” labor landscape. In fact, the development of truly exceptional technologies for the construction industry rests entirely on equipment, and even then, the construction industry is slow to pick up. Productivity boosting, efficiency optimizing, and cost-reducing technologies are more of a recent development.
Truly business altering construction technologies have really only emerged in the last 5 years, but the pace of their adaptation and diversification is rapid. Tools like telematics, apps, drones, 3D printing, live view asset trackers, and geofencing may have seemed like technology of the future a decade ago, but they’re emerging assets in the construction industry today. Below are some of the most accessible, scalable, and adaptive technologies that the construction industry should be (and in some cases already are) taking advantage of.
FLEET TECHNOLOGY
One of the most dramatic changes to every industry across the board is the development of IoT technologies. IoT, or the Internet of Things, allows you to connect to, control, collect data from, and send data to, separate devices or machinery from a remote location. The simplest way to image it is by picturing Alexa or other smart home devices, which now allow you to turn on your coffee maker, change the temperature in your home, etc., just by voicing the command to a single device.
This may seem more like a modern convenience for consumers, but it’s just as altering (if not more so) for the construction industry. You’ll see this more clearly as we discuss the technologies below.
GEOFENCING
Geofencing is the placement of a virtual perimeter—drawn remotely—around a physical location. Geofencing has a lot of applications. Marketers use this to send push notifications when you enter the perimeter of a store. Smart cities use it to gain insight into its city’s roads, such as how many and which trucks cross a certain bridge with unlawful weight, causing structural damage. And, construction fleets use it to evaluate jobsites.
Geofencing technology allows fleets to monitor a jobsite and the productivity of workers in several ways. First, it will alert you to deliveries as they arrive, so your team is prepared to offload equipment, tools, etc. right away. You’ll also receive alerts when equipment, tools, or personnel leave or enter the perimeter, which is beneficial for the prevention of theft and misuse of equipment.
If your geofencing tool is integrated with a telematics system, it will also prove instrumental in evaluating the utilization of your equipment. In other words, it will show you the patterns of use, times and duration of use, and whether or not the job could be done more efficiently with another piece of equipment. Geofencing is a complex tool with many uses, and one a general contractor should not be without.
ASSET TRACKERS
Traditional asset trackers utilize barcodes (RFID codes) and scanners to account for inventory. When you scan, it provides details on the product, such as weight, catalog number, etc. This system, while valuable for manufacturers, doesn’t transition well across industries. Recent developments in asset tracking change this.
Asset trackers for construction take around a hundred steps beyond the technology of traditional methods of tracking like barcodes. Instead of data embedded in an image, modern asset trackers provide live updates on assets. Consider the amount of equipment you leave on a jobsite at any given time, or even items like road signs or generators deployed for 6 months or more. Asset trackers allow you to see where those assets are at any given time. Some even allow you to see when they’re turned on/off and how they’re utilized.
This not only helps you boost productivity by ensuring your assets are used properly, they also ensure you’re using the right assets in the right places. Essentially, you’ll have eyes on all of your assets at once, across jobsites, and be able to calculate that each jobsite has what it needs.
Another added benefit is that your equipment becomes less susceptible to theft when you’re constantly aware of where those assets are. And, in the case of theft, recovery of those assets is far more likely. In other words, if you’re not tracking your assets, you’re losing money.
TELEMATICS
Earlier we discussed IoT technologies, and how they allow you to send and receive data to various devices from a single, remote point. IoT technologies utilize the cloud, which is why they integrate so well with fleet management software. When you’re using the right software, with the right integrations, you’re able to update devices all at once, automatically, create optimized schedules that take into account all of your assets, employees, equipment maintenance needs, and more.
Fleet management solutions allow employees to create timecards through apps, keep track of their hours, receive rewards, and score their performance. It allows you to monitor jobsites from a remote location when integrated with communication apps, geofencing, and other tools. The right software can even use algorithms to plan better routes, create more efficient dispatching, create reports, and show trends for everything from maintenance and fuel costs to productivity and utilization.
CLOSING THOUGHT
Implementing new technologies is something general contractors often neglect because they’re thinking work on a jobsite is rather cut and dry. However, there’s a way to increase productivity, communication, and visibility … and these emerging assets fit the bill.
About the author:
Sarah Colley is a freelance copywriter for hire, who specializes in sales pages, website copy, landing pages, and blogging for construction and home improvement companies. Connect with her on LinkedIn @sarahcolleypr.
Modern Contractor Solutions, October 2020
Did you enjoy this article?
Subscribe to the FREE Digital Edition of Modern Contractor Solutions magazine.
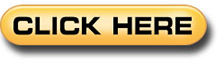