By Greg Norris
COVID-19 didn’t create the need for effective health and safety programs, but the current climate heightens awareness of how paper-based safety processes can hold contractors back.
OSHA, state and local authorities, and construction companies themselves have ramped up pandemic-specific protocols and safety requirements to prevent exposure and reduce the spread of the virus. At a minimum, many companies are checking and recording the temperature of employees every morning and requiring them to complete a daily questionnaire about COVID-19 exposure and symptoms. General contractors are often doing the same for any subcontractors that work on their sites. Most are also adding daily toolbox talks covering the latest recommendations.
Those efforts have resulted in a substantial increase in the volume of new forms, documents, and training materials specific to the pandemic that are in circulation. Moving that information to and from the field with speed and agility is more important than ever to keep employees safe and to stay in compliance with guidelines and reporting requirements that may be evolving daily. Paper creates lag time and limits data quality and reporting. Handling physical documents is even a challenge to physical distancing.
STREAMLINED PROCESSES
Creating paper safety forms can be a tedious and time-consuming job. As a result, many contractors rely on generic forms, which limit the amount and value of the data they can collect. Getting those paper forms from the office to jobsites is equally inefficient, usually requiring a lot of driving and time. The more sites a contractor has, and the more dispersed they are geographically, the more difficult the challenge.
Abandoning paper in favor of electronic forms and reporting gives contractors the ability to build and revise customized forms in minutes with drag-and-drop simplicity. This flexibility is particularly valuable in managing form requirements related to COVID-19, as new requirements or changes may occur frequently and quickly. Contractors, for example, can rapidly design and publish customized forms—or update an existing form—to highlight specific data points that they need leaders in the field to capture.
Most electronic solutions also come with pre-built form templates for a wide range of construction health and safety requirements, including forms specific to COVID-19, and reports to track completion of those forms.
These electronic forms can be published for online access with a click. Up-to-the-minute documents like the latest recommendations or requirements regarding COVID-19 can be included as PDF attachments. Employees can then access the forms and materials on their own devices, allowing them to maintain physical distancing.
BETTER DATA IN REAL TIME
Once a paper safety form does make it to the jobsite, its ability to capture information is limited compared to that of an electronic form. Getting forms back to the office presents another opportunity for delays and lag time. Typically, a foreman will return forms at the end of the week. This obviously will not work for forms and data related to COVID-19.
Electronic forms make it easier to capture more and better data in a structured format and get that data back to the office right away. The forms themselves are easier to fill out on mobile devices in the field. That saves time and leads to better compliance.
Drop-down menus, check boxes, radio buttons, and other devices bring structure to the forms, making the forms easier to complete and helping to ensure that data is collected in a consistent, effective, and easily reportable format. Fields can even be required. This prevents an employee from submitting an incomplete form or leaving out information he or she may not want to report either accidentally or on purpose.
Approvals and submission of electronic forms are instantaneous. Forms don’t pass from person to person or sit in a truck for days. When a form is filled out and submitted, the information is visible instantly in the office, where it can be used to guide decisions or to populate reports. Fields within an electronic safety form can even be set up to trigger automated alerts and notifications delivered by email or text message to specified recipients.
Richer data like time stamps, GPS information, photos, or videos can also be included with or built into the forms. That’s just not possible with paper. Electronic signatures are equally important. They allow forms to be approved, signed, and submitted quickly by several people, without passing around a physical form. The e-signatures add validity too, confirming where and when a form was signed and preventing any alterations after the signature.
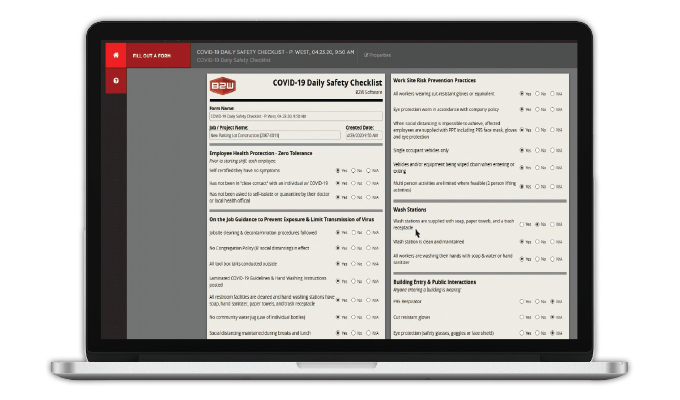
POWERFUL REPORTING
When safety data is trapped on paper forms, extracting it to build reports is difficult. The forms must be returned to an office, where someone has to pour over them and re-enter the data into another system manually. That adds administrative costs, introduces opportunities for errors, and delays the flow of potentially vital analysis and intelligence.
Faced with this labor-intensive process, many contractors simply file the forms away in a drawer and never use the data.
One of the biggest arguments in favor of electronic forms is the ability to automate and enhance the reporting process. The systems can be set up so that data from forms automatically populates standard reports and dashboards. Users can also build custom or ad-hoc reports with ease.
CLOSING THOUGHT
Information may be the most important health and safety tool a construction company has. That is especially true when facing the unprecedented challenges of the current pandemic. By taking paper out of the process and adding the advantages of e-forms and enhanced reporting, contractors can get more agile and effective in educating employees, preventing immediate and ongoing threats, and responding to evolving guidelines.
About the author:
Greg Norris is director of marketing communications for B2W Software (www.b2wsoftware.com). The company’s ONE Platform connects people, workflows and data, and includes advanced, unified applications to manage estimating, scheduling, field tracking, equipment maintenance, data capture, and business intelligence. Greg can be reached at gnorris@b2wsoftware.com.
Modern Contractor Solutions, September 2020
Did you enjoy this article?
Subscribe to the FREE Digital Edition of Modern Contractor Solutions magazine.
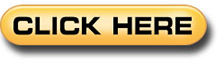