By Ben Froland
The pandemic continues to impact the construction industry as more contractors search for ways to improve efficiency and make up for time lost on projects. New technologies can provide critical efficiency gains as contractors face increased pressure to stay competitive and win bids.
FINDING EFFICIENCIES IS A PRIORITY
Along the lines of the Need for Speed program from the American Institute of Steel Construction (AISC), many construction fabricators and contractors are looking for more efficient ways to do business and new technologies that save time and money. While efficiency has always been a priority, it’s especially critical now as the industry looks to rebound from the pandemic slowdown.
A member survey by Associated General Contractors (AGC) of America shows that construction is essentially less productive now than it was before the pandemic. Increased safety measures that have been implemented on jobsites due to the pandemic—such as restricting how many people can work in a tight space together or how many workers can be shuttled to a remote jobsite together—protect worker safety but have made the operation less efficient.
“What people don’t appreciate is how much more expensive it is to operate during the pandemic,” says Brian Turmail, vice president of public affairs and strategic initiatives for AGC.
As a result, many contractors are looking for ways to improve efficiency and reduce costs.
“The pandemic has almost worked like an accelerator on existing trends,” Turmail says. “A lot of contractors have been exploring technologies, like using robotics or using drones to do inspections. All of a sudden, what was an interesting curiosity before to see if it was worthwhile becomes a necessity.”
AISC member feedback echoes this, says Brian Raff, vice president of market development. More of their steel fabrication shop members are using robotic welding, for example.
IMPROVING PRODUCTIVITY
As contractors look for ways to improve efficiency and productivity on projects, new technology and a shift in processes or techniques can deliver results. Here are some changes that can help save time and money.
New technology for the jobsite: In the search for more efficient technology, the ability for welders to make adjustments remotely can deliver significant time savings. Walking between the weld joint and the welding power source to change parameters and processes can add up to hours wasted every day. This is especially true on larger jobsites where the welder may be hundreds of yards or several stories away from the machine and needs to make frequent adjustments. If a welder makes the trip four times a day and takes an average of 15 minutes each time, that’s 250 wasted hours per year—totaling $11,250 in lost productivity. ArcReach® technology from Miller Electric Mfg. LLC provides operators with complete control at the weld joint using a wire feeder or stick/TIG remote, which allows them to reduce or eliminate this wasted time. Wireless Interface Control on Trailblazer® and Big Blue® welder/generators provides full front panel access from wherever operators are working on the jobsite, so they don’t have to go back to the welder/generator to turn it on or off, change welding processes or adjust parameters.
A change to processes: Converting to wire welding processes is another change that contractors can make to improve productivity and efficiency. More companies are transitioning from stick welding to wire welding on construction jobsites, due in part to the significantly higher deposition rates and travel speeds that wire processes can deliver. These gains can be realized while still meeting high weld quality requirements and improving jobsite safety.
Streamlining steps: The ability to complete parts of the construction or welding process with the workers on the jobsite—rather than hiring a third party for those tasks—can help contractors reduce costs and gain better control over the schedule. For example, many welding applications on construction jobsites require welding preheat. If the contractor is paying a subcontractor to come to the site and use resistance heating for this task, it can add significant time and cost to the process. Preheating contractors can charge up to $2,000 per joint, and setup time can be up to 3 hours per weld joint. New ArcReach Heating Systems from Miller eliminates the need to bring in more subcontractors by enabling welders to do the welding preheat.
CLOSING THOUGHT
As the construction industry rebounds from the slowdown spurred by the pandemic, it’s more important than ever for contractors to use solutions that help make up lost time and keep them ahead of schedule.
About the Author:
Ben Froland is a market development manager, Power Systems Division, with Miller Electric Mfg. LLC. For more, visit www.millerwelds.com.
Modern Contractor Solutions, November 2021
Did you enjoy this article?
Subscribe to the FREE Digital Edition of Modern Contractor Solutions magazine.
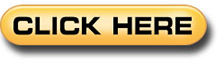