As the global market continues to be pressured from recessions, increased supply chain complexity brought by geopolitical conflicts, material price increases and labor shortages, a new layer of uncertainty is making its way throughout the Construction and Engineering (C&E) industry.
“There is huge potential for those looking to adapt and become more resilient,” explains Kenny Ingram, vice president of construction & engineering, and Chris Knight, global industry director of construction & engineering, at IFS.
1. THE RISE OF THE INDUSTRIALIZED CONSTRUCTION MODEL—BECOMING THE NEXT-GEN CONSTRUCTION COMPANY
Increasingly we are seeing the industrialization of construction processes, in fact, by 2025, 30% of companies will change their construction processes to an industrialized construction model. However, we also see that the long-standing challenges of improving productivity, while reducing cost and waste, remain. Plenty of companies have struggled to successfully evolve their operating model use, for example, modular construction. So, how can they transition more successfully?
A recent McKinsey report commented on low productivity in the industry and produced a comparison to show that if the construction industry were able to keep pace with other industries like manufacturing, it could reach a value of $1.6 trillion per year. The industry’s traditional challenges have been amplified by the global financial pressures and disruptions caused by inflation, parts and material availability, and transport challenges, as well as price increases for materials and equipment. All of which are heightened by labor costs and shortages brought on by an aging and retiring workforce and subsequent widening skills gap—currently estimated to exceed a million workers by 2025.
But through watching other industries and their experiences, the construction industry is evolving to a new model of working, including standardization and platforms, design for manufacturing and site assembly, digital design (BIM), and increased emphasis on structured supply chain processes. Companies will have to transition to industrialized construction processes to drive performance improvements and succeed in the future.
2. IT’S TIME TO PUT PLANNING AT THE HEART OF PROJECT OPERATIONS
A recent article from ENR (Engineering News Record) stated that new construction projects will be flat in 2023, so growth is going to be a challenge. Against this backdrop, companies have recognized that they will need to improve company and project financial control processes and systems. The need to report on a project’s financial status and accurately predict the outcome of a project has never been more vital. Now, 20% of companies, will execute plans within the next 4 years to have more robust, timely and accurate financial control and governance processes and systems.
Yet many companies fail to realize that their current mix of disparate processes and systems with poor or no integration are compounding the reliance on an excessive use of Excel spreadsheets to produce financial project control information.
At present the most typical situation is one where financial accounting systems exist but have limited integration with the systems that process the cost and revenue transactions that impact the project. These are procurement (Materials, Services, Equipment Rental and Plant Hire), subcontract packages, labor costs from payroll, time recording and expenses, and occasionally manufacturing costs as companies transition to more industrialized construction methods. Without an integrated approach, the actual costs and revenue transactions are processed through manual journals which are manually entered into the finance system. These are very slow and error prone, and do not allow for any meaningful or real-time drill down analysis.
With this backdrop, we are seeing a strong trend emerging. Companies now want all the above processes and associated data to come from one complete project financial control solution that provides reliable, accurate, timely, trusted project financial status and reporting and more accurate project outcome forecasting. Companies now more than ever understand that they must make this transition to improve their project financial performance, reduce project and business risk, and make more informed business decisions.
3. SIMPLIFY AND STANDARDIZE: MOVE PROJECT PROCESSES TO A SINGLE, OPERATIONAL PLATFORM
We have established that there is increased urgency for companies to improve business performance. For C&E companies this starts with improving project performance, meaning project margins, reduction in financial risk, driving up productivity, quality and sustainability while at the same time reduce the total asset lifecycle cost.
Embedded in this performance goal is the need to deliver projects using standard repeatable processes and achieve predictable, repeatable results. We can expect to see a quarter of companies move to simplify and standardize their project processes with a single operational platform.
To achieve this, business processes and systems that support these processes need to be challenged, reviewed, and improved to shift to a lean construction model.
Having the right technology is now acknowledged as a vital foundation to achieving improved project and business performance. ERP has been hailed as the solution for many years but for most companies it has failed to deliver. Too often ERP is seen as an accounting software solution, with everything else requiring a specialized system.
This trend is thankfully starting to change as the need for end-to-end integration and visibility increases. Construction and industry specific ERP solutions will allow back-office finance and Human Capital Management solutions to be satisfied, as well as the owners of more operational processes such as estimating, contract management, project management, risk management, and construction site execution processes. One integrated ERP platform is now accepted as the basis to allow companies to adopt standard repeatable processes that positively impact and improve project performance.
CLOSING THOUGHT
Resilience is what has kept the industry moving and it is what will evolve companies into industry leaders with a more lean, profitable, and technological operating model that will not only weather the uncertain times ahead but provide a more reliable platform for success.
About the Authors:
Kenny Ingram is vice president of construction & engineering and Chris Knight is global industry director of construction & engineering at IFS. Together they have 60+ years of experience. For more, visit www.ifs.com.
Modern Contractor Solutions, March 2023
Did you enjoy this article?
Subscribe to the FREE Digital Edition of Modern Contractor Solutions magazine.
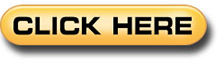