As the bar continues to be raised by external pressures, such as rising costs for fuel and materials and increasing governmental regulations, it becomes increasingly important for contractors, construction companies and service truck operators to complete jobs on schedule and on budget.
A diesel engine-driven welder/generator with dual-operator capabilities is one tool that could be part of the solution in meeting these demands. Dual-operator engine-driven welder/generators offer versatility to help accomplish a wide range of jobs in today’s working environment—with the power and capabilities to function as a multi-operator work platform—while also improving efficiency and fuel savings.
Dual-operator engine-driven welder/generators allow multiple workers to use one machine simultaneously for welding, cutting, or operating lights or grinders, which saves space and maximizes equipment capabilities on a crowded jobsite or work truck.
A dual-operator machine can also help companies and operators reduce the need for additional capital equipment purchases, because a single machine can now do the work of two. Companies can see additional financial payoff, since one engine uses less fuel and requires less maintenance when compared to operating several single-operator engine drives.
POWERFUL CAPABILITIES
Diesel engine-driven welder/generators with dual-operator capabilities provide enough power not only for the two onboard welding arcs, but also enough power to operate additional inverter-based welding power sources, such as an XMT® 350, CST™ 280, or PipeWorx 350 FieldPro™.
The increased output offered in some dual-operator machines on the market eliminates concern about reduced weld power while a second user simultaneously welds or powers another tool. These capabilities and advanced weld controls allow multiple operators to work with no arc interaction.
Technology available in Miller dual-operator engine-driven welder/generators on the market today allows two independent weld outputs. This makes the machine much more efficient—operating at a higher frequency so that the arc noise from one weld output does not affect the output of the other.
This can help companies maximize resources in the field.
The ability of some dual-operator machines to weld and offer three-phase power at the same time makes them more of a work platform. One available machine can be used by as many as six operators at once, at about 120 amps each. This can help companies boost productivity, often without the cost of adding machines or renting large power generators.
Manufacturers also are building engines that last longer and require less maintenance. A machine with dual-operator capabilities requires reduced time and cost for oil changes and routine maintenance, when compared to having multiple single-operator machines to maintain and service.
BUNDLE OF BENEFITS
An engine-driven welder/generator with dual-operator capabilities can offer productivity gains because it meets the needs of many applications and doubles the amount of welding arcs when compared to a traditional unit that only facilitates a single operator.
When compared to a dual-operator unit, operating multiple single-arc machines creates a noisier jobsite that can impact worker comfort, productivity, and safety. Additionally, multiple units burn through fuel more quickly and increase the amount of exhaust emissions compared to one dual-operator welder/generator. The cost-per-arc associated with each option is something to consider when looking at the return on investment of a machine.
The flexibility and power to plug plasma cutters, grinders, lights—and additional welding power sources—into an engine-driven welder/generator is key on cramped jobsites where saving space is an important consideration. Some units even have built-in air compressors for additional productivity and space saving gains.
The ability to reduce the amount of equipment on a jobsite or work truck—while maintaining or increasing productivity—also plays a role in the return on investment of dual-operator machines. Less equipment equals reduced logistical costs and planning, and also less clutter, which promotes efficiency and can help improve jobsite safety.
Since many dual-operator engine-driven welder/generators have low-speed diesel engines, they operate at a lower rpm, typically 1,800 rpm, which results in reduced noise generated. Low-speed diesel engines only operate at a higher rpm when they are under load, and they operate at lower rpm (idle) when not under load, adding to jobsite comfort and safety.
34 PERCENT COST SAVINGS
One engine that provides multiple arcs equals a lower cost-per-arc when compared to multiple single-arc machines. The amount of savings is based on use and the size of the equipment, calculable based on current expenses.
For example, if typical use is 1,000 hours per year, fuel and regular service expenses of one dual-operator machine versus two single-operator machines will result in 34 percent in annual savings. More hours of use will equal more dollars saved.
The ability to do as much as possible with one machine saves money and space on the service truck or the jobsite, and helps get work done more efficiently.
A diesel engine-driven welder/generator with dual-operator capabilities is a tool that can offer fuel efficiency for a range of jobs and options for multiple users—all without sacrificing arc quality or productivity. ■
About The Author:
Joe Gitter, product manager, and Ben Froland, technical product specialist, engine drives, are with Miller Electric Mfg. Co. For more information, visit www.millerwelds.com.
_________________________________________________________________________
Modern Contractor Solutions, February 2015
Did you enjoy this article?
Subscribe to the FREE Digital Edition of Modern Contractor Solutions magazine.
Dual-Operator Capabilities
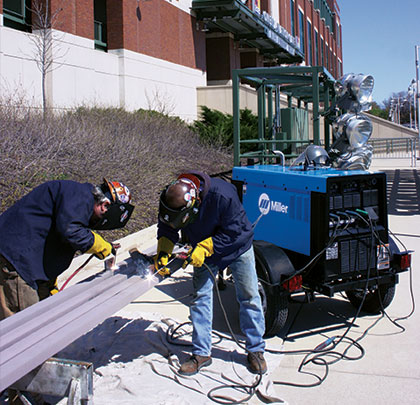