Company takes care of Ohio’s infrastructure
By Debby Keegan
Dennison Bridge Inc. has been completing highway and slide repair work for the Ohio Department of Transportation since the 1950s. Slope stabilization is a niche specialty, but with more than 43,000 lane miles of highways representing the fourth-largest portion of the Interstate system in the nation and an infrastructure report card of D+, Dennison Bridge has the resources that can deliver success on most ODOT projects.
THE PROJECT
The slope repair project outside of Alexandria, just up from the Ohio River and State Highway 7, was slated to start last fall but, at the last minute, a water main was discovered that had to be relocated before the work could start. This delayed the project until March 2019.
The project called for a total of 221 drilled shafts in two phases: 25 in one location and 196 in another. The predominant soil conditions included areas with clay on top but rock underneath, so they needed a more powerful and efficient drill rig than the dangle drill they’d been using. Dennison Bridge selected Bay Shore’s TR60. The dangle drill only has a one-piece kelly bar and no crowd-pressure system or side-tilt capabilities. It also weighs only a fraction of what the TR60 weighs, and that extra weight helps the auger battle whatever is in the ground.
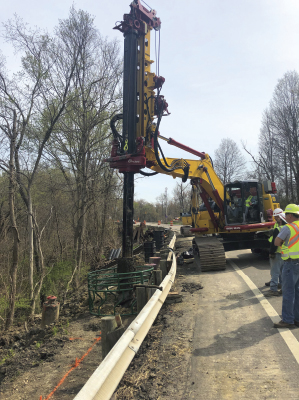
THE CHALLENGE
With the slope continually sliding, it was imperative the reinforced concrete pilings be installed as quickly as possible. The first 25 holes were done with the dangle drill and took 2 weeks, averaging two holes per day. The second phase with 196 holes and using the TR60 completed six holes per day with an expected finish of 6 weeks.
The 24-inch diameter holes are drilled 30 feet deep. After drilling the shaft, a 26-foot I-beam is inserted to provide slope stability before cement is poured in. After 20 to 30 minutes, the cement has dried, and a form is placed over the hole so additional cement can be poured to create an above surface column of approximately 2 feet.
THE SOLUTION
The most challenging aspect of this project and all of Dennison Bridge’s projects is the sloping conditions on which the machinery and employees must operate. The hillsides can have slopes of 25, 30, even 45 degrees or steeper. The employees are working on the slope where footing is difficult. The drill rig needs enough reach to be able to reach over the barrier and drill the hole, all while remaining stable.
According to Matt Nardi, president of Dennison Bridge, “This new drill rig is perfect for this application. It’s just what we needed. We are very happy we purchased it.”
CLOSING THOUGHT
One of the largest savings with this project, between the dangle drill and the TR60, is the cost of cement. With the dangle drill, 12 yards of cement were needed to fill two holes. Because the TR60 is able to drill a smoother and straighter hole, 10 yards of cement are needed to fill three holes. At a cost of $137 per yard, this represents a savings to Dennison Bridge of $2,192 for every six holes drilled.
BAY SHORE SYSTEMS
In a recent conversation with Adam Minatre, president of Bay Shore Systems, he spoke about the ongoing community involvement with a technical school to engage students as they pursue training. “The goal is to let students know about the jobs that await them in the real world. We know on the manufacturing side that the average age of a welder or drilling operator is 54. We need to keep an eye on how many skilled workers are leaving the workforce and do our part to ready the next generation of workers to step into a job within our industry.”
About the author
Debby Keegan is the marketing manager for Bay Shore Systems Inc. For more, visit www.bayshoresystems.com.
Modern Contractor Solutions, September 2019
Did you enjoy this article?
Subscribe to the FREE Digital Edition of Modern Contractor Solutions magazine.
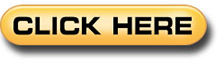