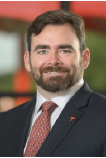
Travelers released its 2023 Travelers Risk Index on distracted driving recently, which revealed that the number of construction business owners who have implemented a distracted driving policy has nearly doubled since 2022, with 65% saying they’ve implemented one in 2023. The index also showed that the construction industry’s number of accidents seem to be trending in the right direction. In 2022, 24% reported an employee being involved in an accident while driving for work due to distraction, this year, that number is down to 20%.
With summer projects in high gear, Chris Hayes, assistant vice president of workers compensation and transportation, risk control, at Travelers, discusses what construction companies can do to continue this momentum and keep their employees safe while driving.
MCS: What are the top three strategies to curb distracted driving?
CHRIS HAYES: First, create a policy that states your organization’s position on mobile device use while driving, regularly communicate this policy to employees and remind them to be mindful of their behavior while driving. For instance, a policy could require employees to stow away their phones whenever they’re behind the wheel. While many contractors have rules in place already, the 2023 Travelers Risk Index found that the construction industry is slightly behind others: Some 65% of construction businesses surveyed reported that they have an official policy about employees using phones while driving, compared to 74% of businesses across all industries.
Next, train employees on safe driving best practices so that all drivers understand vehicle safety policies and procedures. Make sure that managers are reinforcing the expected behaviors.
The third strategy is to invest in technology, such as telematics, that monitors employees when they are driving. According to the Travelers Risk Index, 45% of construction companies do use technology to track employees’ behavior when they are driving company vehicles for work purposes. Contractors can review the data collected and use it as part of an ongoing safe driving feedback and coaching program, addressing any potentially dangerous actions and acknowledging safe behaviors.
MCS: What types of training are best, other than classroom sessions?
CHRIS HAYES: Classroom training should be used to reinforce skills, further your safety message and reinforce your expectations. By the time someone works for you, they should already know how to drive. Be sure to run a check on their license to make sure it’s valid. In addition, checking for violations is a best practice.
Leading by example and modeling desired behaviors can help reinforce classroom training and your organization’s commitment to safety. For instance, avoid texting or calling employees when you know that they are driving. If they are behind the wheel when you call, ask them to ring you back once they are safely parked. And when you are behind the wheel, don’t make phone calls or send text messages.
2023 INJURY IMPACT REPORT
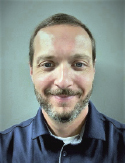
Do you know how many days an injured construction worker is off the job? On average, it’s 99 days, according to data from Travelers, the country’s largest workers compensation carrier. The 2023 Injury Impact Report, found that average lost workdays in construction led other industries including manufacturing, wholesale and small business and are far above the all industry average of 71 days. Further, the data shows that construction workers compensation claims were the most expensive, more than double the average among all industries.
Nick Wayne, managing risk control consultant, construction, energy & marine at Travelers, shares three suggestions for commercial contractors on how to reduce injuries on jobsites.
MCS: What are three recommendations for commercial contractors on how to reduce the risk of injury on jobsites?
Nick Wayne: With proper precautions, many injuries can be prevented. Travelers recommends that its construction customers start by establishing and maintaining a strong safety culture. This means weaving safety into your company’s mission, policies and procedures, and planning for the unexpected. It’s never too early to address potential safety concerns, including during the bid phase. Discussions on potential safety-related controls, equipment needed or changes to processes can help minimize risk.
Ongoing risk management efforts can be enhanced by looking at potentially hazardous situations and taking steps to address them. For instance, if you identify an exposure to falls from heights, consider installing guard rails as a preventive measure. Or it might be better to use Personal Fall Arrest Systems (PFAS). In that case, it’s critical to train workers on their proper use. If electrical hazards are present, implement lock-out-tag-out (LOTO) or other means of isolation. If a job requires employees to lift heavy objects, determine ways to redesign the job to reduce the physical burden of the task.
Additionally, encourage everyone to speak up if they see something concerning so that it can be addressed promptly. When possible, engage front-line workers to assist with developing solutions, which helps promote effective implementation.
Focus on hiring qualified candidates, and onboard and train them as they come on board. When hiring, create a detailed job description that clearly identifies job-related functions, including physical capabilities and safety expectations to help make sure you are attracting qualified applicants.
After recruiting qualified employees, remember that onboarding is not a one-size-fits-all activity. Since jobsites vary, develop site-specific training to help keep employees engaged and safe. Orientation can include an overview of the jobsite, job-specific roles, and a review of the company’s overall culture of safety. Assign new employees a mentor who demonstrates your company’s safety culture and can guide them through this phase. It’s also important to train employees on the tools and heavy equipment they will be using. These efforts can help reduce the likelihood of a new employee getting injured, which is common in the construction industry. In fact, the 2023 Travelers Injury Impact Report found that almost half (47%) of all construction workers compensation claims occurred within the first year of employment.
CLOSING THOUGHT
Investigate accidents when they occur to identify the root cause and take action to help prevent future ones. Use these insights to update your training and risk management practices, and consider using technology as an additional tool to help you address worker safety concerns. We regularly research various technologies that are available to contractors and share what we learn, including potential uses, benefits and risks, with our customers through the Travelers Innovation Network for Construction. For instance, wearables with proximity sensors can help mitigate risks related to the utilization of machinery, forklifts or heavy equipment.
About the Author:
For more information about Travelers, visit www.travelers.com.
Travelers.com/distracteddriving
Travelers.com/injuryimpactreport
Modern Contractor Solutions, August 2023
Did you enjoy this article?
Subscribe to the FREE Digital Edition of Modern Contractor Solutions magazine.
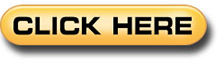