By Alex Moody
Digitization is happening in our industry—but the bad news is that it’s not in all areas. We still live in a world of manual processes: re-keying data, signing documentation in the field, giving invoices to the accounting department, waiting forever for reconciliation, and more. The result is a lot of paper, handoffs, and data re-keyed.
The digital tools that are most common today support a one-to-many relationship. A collaborative platform supports a many-to-many relationship and can digitize and connect the entire construction materials supply chain.
MOVING FORWARD
First, let’s consider a few statistics that exemplify the struggles that many jobs face:
- 98% of megaprojects face cost overruns or delays
- The average cost increase of a construction job is 80% of the original value
- The average slippage is 20 months behind the original schedule
- Productivity levels in manufacturing have nearly doubled, but in construction, it has stayed flat
Two significant factors that play into this equation is the timeframe of the project. Most jobs are short-term projects, and managers often feel like there isn’t any time to implement change; most employees don’t have the desire.
Another big reason is because of the time it takes to track materials and reconcile invoices. Most employees who work on a job are out in the field, moving around instead of sitting at a desk. Given that mobile devices have just taken off within the last decade, there hasn’t been as much of a chance to boost productivity levels compared to other industries whose workflows enable them to have information available to them at all times.
NEW TECH SOLUTIONS
So, if a company realizes the opportunity to optimize and boost productivity, they have to go about it in innovative ways; and that innovation has to start from the top and trickle down.
Like a ship’s navigation system in a storm, a clear strategy is the only way companies can stay on a successful course. Yet, the hardest part is making the changes needed, and it helps to have one leader to inspire the actions that will drive those changes.
It’s imperative to have one leader to implement new technology successfully. For each new system that is added to the workflow, there needs to be one project leader to establish camaraderie across the team for that particular solution and to ensure that it’s successful and helps the team rather than hurt it.
New technologies can be embedded into processes to enable a digital supply chain network that keeps the jobsite in sync.
Digital networks are the backbone of a truly optimized construction firm. They reduce or remove the wasted time and motion, lack of accuracy, and resulting overruns that almost inevitably arise when jobs are not effectively synchronized.
Well-run digital networks employ tools, techniques, and best practices to create a collaborative space, where all necessary parties involved in a construction project are apprised of the status of different parts of the job and can quickly adjust to required changes.
BEST PRACTICES
So, how do construction firms keep on top of their construction jobs and keep projects running smoothly? Below are five ways construction firms keep moving forward.
They monitor digital signals. If concrete is delivered early, no one will be around to make sure it goes to the right spot. If it is delivered late, workers waste time sitting around doing nothing. If the materials are not at the required specification, time is wasted adjusting slump. If the materials result in a “bad pour,” it costs the supplier money (and possibly legal troubles), and the job is no longer on schedule. Digital monitoring and instant alerts help to eliminate wet loads, simplify calibration, minimize process heating and cooling costs, and achieve consistent results.
They pay attention to data from the Internet of Things (IoT). IoT data is embedded in construction project lifecycles and gathered from a myriad of sources, including remote and wireless sensors. It lets companies sync equipment, materials, asset usage, and worker productivity in real time. It even allows companies to track expensive equipment or tools more effectively, aids materials management and inventory control, minimize project delays, and will enable managers to stay on top of required equipment maintenance.
They use a single point of management. This single point of management lets companies manage materials, mixes, tolerances, documentation, and testing and analysis in a single location. As an added benefit, a single point enables construction firms to show customers that incoming raw materials conform to supplier and customer requirements.
They optimize concrete mixes to comply with strength, durability, and aggregate grading requirements. By monitoring batches in real time, companies can reduce out-of-tolerance loads, produce concrete mix submittals in a fraction of the time they took before, and craft professional reports and documentation to build trust and authority.
They boost productivity on the jobsite. Productive construction firms use digital tickets to ensure data flows seamlessly from suppliers to contractors and owners, so the jobsite stays in sync. By digitally capturing information from paper tickets, buyers can see ticket data in real time, throughout the ticket’s lifecycle. Solutions like these can deploy notifications for when a load is on the way, allow the user to view records of load status times, and automatically match incoming delivery tickets with hauler pay sheets and invoices. Further, tools that let construction firms collect both real time and historical data on the properties of fresh concrete—from load to pour—help ensure better decision making to ensure quality, avert risk, enhance production, and increase delivery efficiency.
CLOSING THOUGHT
Digital networks connect concrete producers, aggregate suppliers, jobsite managers, contractors, construction firms, DOTs, and more for better collaboration and communication within their supply chains.
About the author:
Alex Moody is a senior product manager at Command Alkon for CONNEX Jobsite. CONNEX Jobsite is a paperless ticketing supply chain management system designed to transform the way contractors, suppliers, and haulers interact to increase performance and reduce costs. For more, visit www.commandalkon.com/connex.
Modern Contractor Solutions, July 2020
Did you enjoy this article?
Subscribe to the FREE Digital Edition of Modern Contractor Solutions magazine.
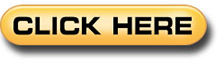