By Seth Ulmer
Contractors wear many hats during their life—mechanic, electrician, and heavy equipment operator, just to name a few. Having the knowledge and proper tools to easily pivot between tasks is what keeps operations running smoothly. Contractors know that investing in specialized tools, even just for occasional work, can provide a great return on their investment with efficient, long-lasting results that benefit future generations. To achieve a lasting foundation, contractors should evaluate their options, recognize the drawbacks, and choose equipment best fit for their scenario.
BEGIN WITH THE BASICS
Circular concrete pours most often start with a pivot kit, which minimally consists of a metal stake fixed to a weighted base. The stake is affixed to the center of the work area and can be used as a guide to frame out the circular pad. A pivot kit gives users the ability to attach one end of a concrete screed to the center stake and control the screed from the other end, screeding off concrete in a clockwise motion. Any number of concrete screed options can attach to a pivot kit. The most popular methods include hand screeding, using an A-frame screed or working with a roller screed, but each come with their own limitations.
OPTIONS AND LIMITATIONS
Hand screeding utilizes a long aluminum or heavy wooden board which is extended to the center stake and pulled by hand around the circular form. This can be a strenuous, time-consuming task and may result in structural flaws due to a warped board and uneven concrete dispersion. With structural flaws rarely justifying savings, this option leads many to explore the methods implemented by professional contractors, like an A-frame or roller screed. These methods have varying levels of usability, with some more user friendly than others.
A-frame screeds consist of multiple sections and can be more cumbersome than alternatives. Fins and vibratory attachments hang off the back of the main bar to provide a compacted and smooth finish as the screed pulls, vibrates and spreads the concrete. However, this design limits screeding to one direction. A roller screed, on the other hand, consists of a drive head and pipe that spins in the opposite direction it is being pulled to level concrete. Roller screeds can be electric, hydraulic, or gas motor powered and are typically lighter and easier to maneuver than an A-frame. However, a gas motor can be a limiting factor as it restricts the direction of the spin, a shortcoming similar to the A-frames. But what’s wrong with only screeding in one direction?
UNIDIRECTIONAL SCREEDING
Unidirectional screeding is often acceptable for conventional concrete flatwork but less favorable with circular pours. A circular concrete pad can take several hours to pour, and unidirectional screeds are committed to screeding one direction for the duration of the project. For efficiency and minimal wasted movement, the pad is usually poured in continuous sections with, for example, the first being from 12 to 2 o’clock. A contractor screeds that section and then the next is poured from 2 to 4 o’clock, and so on.
This might seem effective, but once the pour is nearing completion and arriving back to the first section, the crew is now pouring and screeding wet concrete next to concrete that has been curing for several hours. This creates a cold joint which can cause a division in the uniformity of the concrete pad, preventing it from curing as one solid, smooth, level foundation. The visual irregularity from a cold joint may leave something to be desired for the concrete pad’s appearance, but it’s also a structural flaw that can result in future costly repairs or possible grain bin failure.
MULTIDIRECTIONAL SOLUTION
The best method to avoid a cold joint is by pouring each section of concrete and alternating left and right sides of the circle. For example, if a section is poured at the circle’s 12 to 2 o’clock position, the next section could be poured from 2 to 4 o’clock, but the third section should be poured from 10 to 12 o’clock. This alternating pattern ensures every section cures for the shortest amount of time before fresh concrete is poured next to it, leading to a more uniform cure.
This alternating pattern introduces the utility of screeds with a changeable spin direction. For all roller screeds to operate correctly, the screed pipe spins away from the operator. But, the ability of some screeds to change spin direction at the push of a button allows operators to effortlessly screed clockwise or counterclockwise, making these screeds capable of performing the alternating pattern efficiently. This means operators can alternate screeding sections rather than working in a full rotation and risking cold joints and wasted movement.
CLOSING THOUGHT
A contractor is no stranger to recognizing efficient solutions. Tackling a circular pour with equipment already available is possible, but alternative methods can offer time savings and lasting quality.
About the Author:
Seth Ulmer is the sales manager at Curb Roller Manufacturing, a world leader in shaped concrete roller screeds for more than 10 years. Curb Roller’s ergonomic machines not only make it easy to shape standard curb, gutter, and sidewalks, but also flume, v-gutter, swale, and other unique shapes. For more, visit www.curbroller.com.
Modern Contractor Solutions, September 2021
Did you enjoy this article?
Subscribe to the FREE Digital Edition of Modern Contractor Solutions magazine.
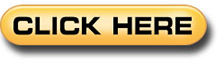