Minneapolis, Minnesota, is home to a population of more than 425,000 citizens. The largest city in the state, Minneapolis is supported through extensive underground infrastructure—most of which is decades old. The most pressing concern when it comes to this infrastructure is the deterioration of the stormwater tunnels beneath the city.
PCiRoads, a highway and heavy civil general contractor out of St. Michael, Minnesota, won the bid for the Central City Parallel Storm Tunnel Project to enlarge portions of the stormwater tunnel, construct a new parallel tunnel, and create new tunnel access in downtown Minneapolis. PCiRoads partnered with Brokk, a leading manufacturer of remote-controlled demolition robots, to rework more than 800 feet of stormwater tunnel underneath the heart of Minneapolis and mine 3,600 feet of new tunnel.
THE OLD SYSTEM
Originally built in 1939, the tunneling system below Minneapolis was designed to address the drainage needs of the time. However, rapid population growth combined with a 30-percent increase in rainfall per hour over the last 50 years mean the tunnels can no longer keep up with demand. The strain of excessive water caused cracking, breaking, and concrete deterioration, resulting in an urgent need for repair.
In 2021, the city of Minneapolis Public Works Department approved a $60 million overhaul of the stormwater tunnel system. The plan is to create a tunnel twice the size of the current system to move stormwater to the Mississippi River.
“When the stormwater tunnels start to fail, we see dangerous flooding and other damages to underground infrastructure,” says Nap Scott, estimator and project manager for PCiRoads. “The repair of the current system and addition of the parallel stormwater tunnel will be a huge step forward in handling the increased demands.”
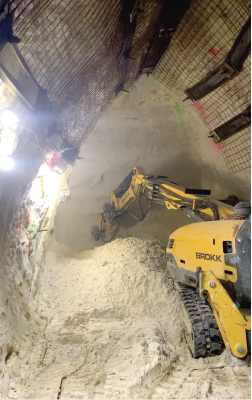
TIGHT SPACES
The PCiRoads crew found several logistical challenges with the Central City Parallel Storm Tunnel Project. The tunnels were so small that the equipment couldn’t pass one another. If a different piece of equipment was needed, the first piece would need to be removed from the tunnel and new equipment brought in, significantly slowing down progress.
Another challenge was that workers and equipment needed to be lowered by crane 80 feet into the system. Traditional equipment, like 5- to 10-ton excavators, couldn’t get into such tight spaces or work safely without the risk of falling debris and pinch points.
To complete the project, PCiRoads purchased two new Brokk 520D demolition robots and a used a Brokk 400 diesel model. They found that the power-to-weight ratio of these machines gave the best hitting power for the size. A 6-ton Brokk 520D is 5.25 feet wide, with a vertical reach of 23.4 feet. To get the same hitting power as a Brokk 520D, they would need to use a 10-ton excavator with a width of approximately 7 feet and a vertical reach of 8 feet. The lighter weight and smaller size of the robots made lowering them down the tunnel’s 80-foot shaft easier and safer than larger equipment.
“The Brokk diesel models don’t need a generator, but that means we needed to make sure there was proper ventilation in the tunnels before we could start,” Scott says. “Once it was set up, the diesel models offered unparalleled versatility because we didn’t need to worry about generators or cords.”
INCREASED VERSATILITY & SAFETY
PCiRoads took advantage of the Brokk demolition robots’ versatility by using multiple attachments throughout the project. With remote-controlled operation featuring a range of more than 950 feet, the operator and crew were removed from the danger zone while the equipment worked. For mining the new tunnel, they used the breaker attachment with the Brokk 520Ds to break the sandstone and shale.
The project required PCiRoads to carve a cathedral shape out of the sandstone. The tunnel comes to an arch at the top to provide additional support for the system. After realizing that the breaker wasn’t the best tool for precise shaping, the PCiRoads team chose the Brokk Drum Cutter 250 attachments with the Brokk 520Ds, which meticulously shaved away the sandstone and shale to create the arch shape.
After removal of the sandstone and shale, PCiRoads moved on to breaking through bedrock at the riverbed. The crew rented an additional Brokk 300 with a breaker attachment to tackle the bedrock, and they intermittently stopped to install ground control. They used a TEI 80 Rockdrill to install rock bolts, which held mesh in place to catch loose rock and debris, protecting the crew against rock falls and tunnel collapse.
Once PCiRoads completes this part of the project, new forms will be rolled out for the tunnel, concrete will be placed into those forms, and the new tunnel will be tied into the current system.
For More Information:
For more on PCiRoads, visit www.pciroads.com. For more on Brokk, visit www.brokk.com.
Modern Contractor Solutions, February 2024
Did you enjoy this article?
Subscribe to the FREE Digital Edition of Modern Contractor Solutions magazine.
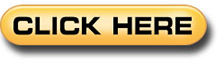