With space at a premium in many urban areas, developers are digging deeper foundations to increase the square footage of residential, commercial, and mixed-use building projects. In Dubai, for example, a new luxury retail and workspace is being built that includes a basement that’s seven levels deep. The lack of parking space in many cities is spurring developers to build multi-level car parks below ground. In other cases, a deep foundation may be needed due to large design loads or poor soil at shallow depths.
Digging deeper foundations has many advantages but also brings about many challenges that need to be addressed at the design phase. Let’s take a closer look at the challenges.
SOIL PRESSURE
There are tremendous external pressures on a deep construction hole. Typically, this requires horizontal piles to be drilled into the sides of the hole to shore them up and keep soil from falling in. High strength rock anchors are then drilled into sound bedrock and then connected to the structure to help the structure resist uplift forces.
HYDROSTATIC PRESSURE
If the soil around the foundation is saturated with water, this places immense hydrostatic pressure against the foundation. All of this pressure means that water will push its way through the foundation, even through miniscule cracks. Where local hydrology allows, drainage systems can redirect some of the water away from the foundation, but they are generally not enough protection for finished basement space. A fully adhesive bonded, pre-applied waterproofing membrane offers the highest degree of protection in these circumstances. By creating an integral bond with the poured concrete, the waterproofing barrier prevents water ingress, even at high hydrostatic pressure.
DEWATERING
In most cases once you dig 5-10 meters down, you hit water. This means you’ll need continual dewatering to keep the site dry enough to construct the foundation. Dewatering involves running pumps 24/7, which is very expensive. The contractor will want to accelerate project completion to minimize these costs. Choosing building materials that are simple to install will be beneficial, because it enables the contractor to get the concrete poured and the basement finished faster, helping to save them money. Some solutions like pre-applied waterproofing membranes can even be placed in damp conditions, helping to accelerate project completion.
CORROSIVE GROUND WATER
Digging deeper increases the chance of exposure to groundwater, which can have high concentrations of chlorides and sulfates in some regions. These conditions are highly corrosive to concrete. The structure can be protected from corrosion by using a waterproofing barrier that is resistant to aggressive soil/water conditions.
About the author:
Ozan Ozanturk is the North American product manager, waterproofing for GCP Applied Technologies. He has more than 10 years of market development experience in various advanced material industries, including building and construction materials technologies. For more information, visit www.gcpat.com.
Modern Contractor Solutions, December 2018
Did you enjoy this article?
Subscribe to the FREE Digital Edition of Modern Contractor Solutions magazine.
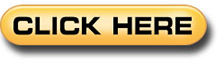