Contractor Mauldon Bros. Construction was recently the low-bidder to replace an existing lift station for the Township of Meridian, Michigan. The precast wet well was installed along Biber Street, between Pollard and Hardy Roads in East Lansing, Michigan.
The installation of a new precast structure with sewer tie-in was really nothing new for brothers Greg and Steve Mauldon, who have been working in sewer and water utility construction since taking over the family business from their dad, Glen, in 1996. What definitely was a new wrinkle for them in the Tower Gardens Lift Station project was the depth of the excavation.
“The 8-foot-diameter wet well we are installing is 28 feet tall,” explains Greg Mauldon. “Before this, the deepest we’d dug was 22 feet deep, so this was definitely uncharted territory for us.”
The biggest challenge was finding a shoring system that could go at least 30 feet deep. The excavation was right in the middle of a residential neighborhood, so open cut and sloping was not an option. Stacked trench boxes were impractical, given the weight and size of the trench shields that would be necessary to withstand the soil pressure at the required depth. With the Mauldon brothers looking at new depths and significant restraints, they needed to seek out a new type of equipment to get the job done.
Featured Image: The 8-foot-diameter wet well we are installing is 28 feet tall,” explains Greg Mauldon. “Before this, the deepest we’d dug was 22 feet deep, so this was definitely uncharted territory for us.”
Above: The biggest challenge to the project was finding a shoring system that could go at least 30 feet deep; Efficiency Production’s Slide Rail System fit the bill.
PERFECT SHORING SOLUTION
Fortunately for the Mauldon brothers, one of the country’s leading manufacturers of trench shoring equipment—Efficiency Production—is headquarted right in their hometown. After a quick review of Mauldon’s project specs, Tim Hurst, a shoring specialist in Efficiency’s Special Operations Shoring Division, was able to design a Slide Rail System that was the perfect shoring solution for Mauldon’s deep dig dilemma. Luckily, Efficiency is no stranger to the type of constraints surrounding the Mauldon’s project.
Efficiency’s Universal Slide Rail is a component shoring system comprised of steel panels (similar to trench shield sidewalls) and vertical steel posts. The highly versatile system can be used in a variety of configurations. Efficiency’s Slide Rail System can be configured into small four-sided pits; an obstruction-free ClearSpan™ configuration; or in a Multi-Bay™ configuration to install large tanks and structures, or lengths of pipe over 40 feet.
Slide Rail is considered “positive shoring.” It is installed by sliding the panels into integrated rails on the posts, and then pushing the panels and posts incrementally down to grade as the pit is dug. This process is commonly referred to as a “dig and push” shoring system. “That was really important on this project,” explains Hurst. “In addition to being very deep, the excavation was also in a very tight spot, right along a main neighborhood road. Mauldon couldn’t over-cut the excavation at all, the sides of the pit needed to be completely vertical, which is exactly what Slide Rail accomplishes.”
Mauldon Bros. Construction are brothers Greg (right) and Steve Mauldon, who have been working in sewer and water utility construction since taking over the family business from their dad, Glen, in 1996.
TOUGH UTILITY INSTALL
“This was the first time for us using Slide Rail and it worked very well,” says Greg Mauldon. “It was the deepest we’ve gone for an install, and we had heard a lot of good things about Slide Rail and were excited to use it and see how it preformed.”
Mauldon rented direct from Efficiency a 16 x 16 x 32 feet deep, four-sided configured Slide Rail System. They completed the excavation and installed the system with a Deere 550 excavator. Also on site, Mauldon had a Cat 314 mini excavator, a Deere 544J front loader, and a Cat 228 skid steer. They rented dewatering pumps from Patriot Pumps.
“We may look at a few more lift station projects in the future,” says Mauldon. “Before, looking at lift station projects, it’s always been, ‘well I don’t know. It’s going to be wet; it’s going to be deep.’ But with Slide Rail this was simple … a piece of cake.” ■
About The Author: James McRay is the director of marketing and media for Efficiency Production, Inc. He can be reached at jmcray@efficiencyproduction.com. Efficiency Production, “America’s Trench Box Builder™,” provides the widest selection of standard and custom trench shielding and shoring systems. Efficiency’s versatile products are designed specifically for safe and cost-effective installation of utility systems and infrastructure improvements. All products are P.E. certified to meet OSHA standards. For more information, visit www.efficiencyproduction.com.
_________________________________________________________________________
Modern Contractor Solutions, August 2015
Did you enjoy this article?
Subscribe to the FREE Digital Edition of Modern Contractor Solutions magazine.
Deep Dig Dilemma
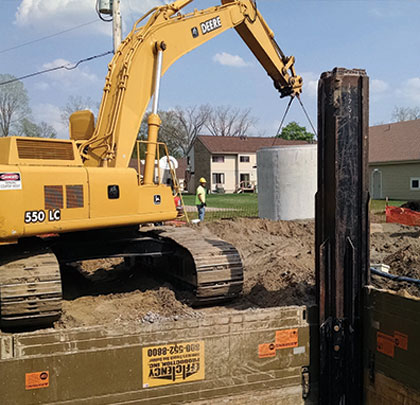