By Steve Getsiv
Americans spend millions each year building, replacing and repairing decks. At an average cost of $16,000 per HomeAdvisor.com, a 16- by 20-foot wood deck if well maintained and properly built with high-quality materials should last up to 20 years according to the National Association of Home Builders (NAHB).
But then again there are numerous elements involved in this equation. They start with the selection of the deck boards themselves. For some, this means specifying the latest low-maintenance composite deck boards from the wide selection of colors and wood-grain patterns. In other instances, real hardwood decking is still the preference among homeowners who relish the natural beauty, durability and hardness of Ipe, Cumaru, and Batu decking as well as the natural resistance to decay, rotting, termites, and bugs. A durable hardwood deck should last upwards of 50 years.
But, no matter the material, builders should make customers aware that nearly every deck requires some form of maintenance beyond the occasional power wash or cleaning to prevent algae and fungus growth as well as the inevitable discoloring that accompanies age. This is especially true for contractors working within wet, humid conditions and hot, dry climates, where wood, siding, decking and fencing are especially susceptible to graying, water damage, and harmful UV rays.
THE DECK MAINTENANCE PROCESS
The first step in the maintenance process begins with the careful inspection of the deck’s condition followed by a decision on the steps needed to refinish the deck, if necessary. If a high-end finish was used in the past, it may be possible to get away with finishing the deck every 2 years instead of annually. However, it can be extremely frustrating to put hours or even days into the deck only to have it look bad and need additional work within a few months.
Decks updated with lower quality stain products commonly require pressure washing or sanding on an annual basis. And yes, this means removing the old finish all the way down to the bright fresh wood. There’s just no point in coating over a grayed out or silvered-out deck. Plus, if the previously used coating didn’t contain a built-in fungicide then the beginnings of mold, algae and more have already likely started to grow within the wood itself.
Again, the goal is a bright, fresh surface that locks in the wood’s natural beauty and color, withstands the elements and looks good month after month. One of the challenges is that water-based finishes are a bit of a mystery since they do little to protect the wood and often necessitate the subsequent application of an oil-based stain the following year. Others contain resins that actually do a pretty decent job holding the wood’s color over time. The problem is that once the resins are absorbed, they seldom allow higher-quality, oil-based finishes to penetrate deeply into the wood during the next application.
Additional considerations surround the numerous quality and performance differences that exist within even leading oil-based stain brands. In most cases, this starts with the very composition of the stain itself and then extends to the assortment of UV blockers, pigments, dyes, fungicide, oils included in today’s products.
For example, many of the oils commonly used in wood stains tend to change color over time. Some even harbor mildew and mold, such as linseed oil, which can lead to the wood turning black or discolored. In fact, the only reason these oils are used by some companies is because they lower the product’s cost, no matter the inferior results.
When it comes to the choice of oils, Polymerized Tung Oil has proven its ability to preserve wood and outperform other products although many users are turned off by the lengthy amount of time it takes to dry. However, some manufacturers have overcome this problem through the addition of high-quality drying and hardening agents that have drastically reduced the time to dry from weeks to days. Plus, another advantage that makes Polymerized Tung Oil worth the wait involves the long-lasting capacity to retain color over time, while naturally resisting mildew and mold.
As for the dyes and pigments used in most stains, trans-oxide pigments are commonly viewed as the more color-stable of the two, which results in the stain maintaining its original color longer than those that contain dyes or solid pigments. But contractors should note that stains containing trans-oxide pigments are not cheap and often bear a higher price although the quality of the application makes them worth the cost in many instances.
In addition, builders should never purchase a wood stain without considering the wide range of ingredients. American-made fungicides, UV blockers and trans-oxide pigments generally combine to better resist water, acid and fading, while also actively increasing the wood’s ability to resist cracking or warping, enhance stability and showcase the wood’s natural luster and beauty. It should also be noted that the highest quality stains use the same UV blockers found in automotive paints, which is another reason these higher-end products tend to cost more but produce higher-quality results.
Other advantages surround the enhanced preservation of the wood’s natural beauty, greater wear resistance in severe climates and safer, easier use. That’s because there’s no need to strip or sand the previous coat before their application and the best products produce lower amounts of VOCs (Volatile Organic Compounds) to ensure user- and environmentally friendly results.
Subsequently, builders should be aware that there’s far more to the selection of wood stain than price. In most cases, the components and ingredients vary significantly, while playing an integral role in the wood’s weathering and the customer’s long-term satisfaction—all extremely important considerations that should always be a preference throughout the buying process.
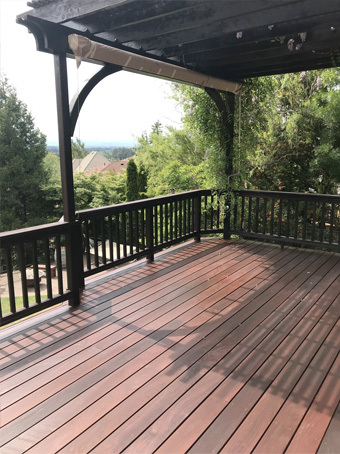
CLOSING THOUGHT
Deck cleaning & stain application tips & techniques
- While all oil-based finishes are not the same, differing brands are generally compatible and can be used from one year to another. Plus, you will not need as much finish if the deck is coated with high-quality stain products annually.
- Any type of film-forming finish such as a spar varnish, urethane or polyurethane must be sanded to achieve the best results.
- You can try a deck cleaner, but don’t be surprised if the deck still needs to be pressure washed or sanded with a belt sander. Hardwoods like Ipe, Cumaru, Batu, Brazilian Redwood, Tigerwood and Mahogany/Meranti are best served through the use of a high-powered, minimum 2800 psi pressure washer operated with a turbo nozzle. Softwoods such as Pine, Cedar, Redwood or pressure-treated woods can be cleaned with a high-powered pressure washer set at a lower setting and using a wide-fan nozzle to prevent wood damage.
- Decks can be safely coated the day after pressure washing when the weather is hot and dry. But, it’s commonly better to wait 3 to 5 days (or longer) so that the water inside the boards has had the chance to evaporate. Deck stain WILL LAST LONGER if the wood is totally dry when the stain is applied.
- Take your time when coating the deck, while carefully following the manufacturer’s instructions. Most finishes must be wiped down. The best results for wiping finishes are often achieved with an old beach towel within 20 to 30 minutes of the stain’s application.
About The Author:
Steve Getsiv is Nova USA Wood Products’ president and CEO. Nova USA Wood Products was founded in 2005 to supply superior, high-quality hardwood products and accessories at competitive prices to today’s residential and commercial building marketplace. For more, visit www.novausawood.com.
Modern Contractor Solutions, December 2020
Did you enjoy this article?
Subscribe to the FREE Digital Edition of Modern Contractor Solutions magazine.
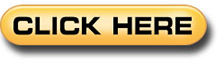