We are in a global climate crisis, as outlined in the latest IPCC report, which notes the world is now experiencing widespread changes in weather patterns and an increase in climate-related natural disasters. However, the building industry is finally at a place where we understand the major role that we play in contributing to global greenhouse gas emissions. As we now work to actionably reduce the sector’s climate impacts and as more business owners and building managers begin to join the conversation—placing sustainability at the forefront of business operations—it’s important to both understand the construction industry’s role in the larger issue and how to act on it.
A huge opportunity for decarbonization lies within the building and construction industry, as it currently contributes to nearly 40% of global greenhouse gas (GHG) emissions, with 13% coming directly from the manufacturing of building materials. It’s important for contractors and building managers alike to think long-term and prioritize the planet when procuring materials for new builds and retrofits to make a lasting impact on the sector. But where should they start, and why are materials so important?
IT’S ALL IN THE MATERIALS
When considering the steps needed to decarbonize the construction industry, contractors should begin by analyzing their materials. Contrary to popular belief, the carbon impact of a construction project starts long before a shovel hits the ground.
The manufacturing, installation, use, replacement, and end-of-life disposal of construction materials can be defined as embodied carbon emissions. The manufacturing emissions—typically the lion’s share of a product’s lifecycle emissions—are locked in during the material decision-making and procurement phases of a construction project. So, solving for embodied carbon emissions presents a huge opportunity for the construction industry. But contractors may not be aware of a material’s impact, or if they are, they may not know of an alternative, low-carbon option. That’s why it’s so important for contractors to understand the carbon impact of a certain material prior to procuring it.
KNOWLEDGE IS POWER
Within a construction project, contractors are focused on staying within budget, remaining compliant, and completing the build on time. Now, sustainability and a project’s overall carbon impact are beginning to be included in this list. So, where does material procurement fall in the sequence of decisions? For contractors, it should be right next to cost and thought of as an additional budget that must be managed.
The more a contractor understands the materials in the marketplace and their impact on the environment, the better decisions they can make to prioritize low-carbon options. This is where Environmental Product Declarations (EPDs) come in.
EPDs are third-party verified technical documents that communicate the lifecycle impact of a material, helping the industry analyze the carbon emissions associated with a procurement decision, new buildings, and retrofits. EPDs provide a product’s carbon intensity per declared unit (kgCO2e), enabling the accounting of embodied carbon emissions at a product and project level. This information is integral to the decarbonization of the construction industry as contractors can compare products with EPDs, making it easier to procure low-carbon options. Or, if a product does not even have an EPD attached, contractors can choose to rule them out from the very beginning of the procurement process.
An accessible tool that leverages EPD data and makes it easier to compare and select products is the Embodied Carbon and Construction Calculator (EC3), a free, easy-to-use, open-access tool that allows benchmarking assessment and reductions in embodied carbon per material category. Today’s contractors are increasingly utilizing this tool alongside procurement decisions and in overall construction operations. The tool has grown to include almost 35,000 users and over 120,000 EPDs in the 3 years since its launch.
Another important factor to consider is the price of low-carbon materials. A myth that continues to be debunked across industries is that building with low-carbon materials is more expensive. A recent RMI study explored the idea that low-carbon building practices were more expensive, finding that construction projects can, in fact, be completed with a 19%-46% reduction in carbon emissions at cost premiums of less than 1%. This is an energizing statistic for the construction industry, realizing that decarbonizing the built environment is actually more attainable than it seems.
For contractors, knowledge really is power. To understand the difference between carbon impacts of materials and the prices attached to them is a step in the right direction to lower the carbon footprint of projects. Contractors can then begin to advocate to their clients that using these low-carbon materials at little to no cost increase is a win-win as it also goes a long way in bettering the health of the planet.
CLOSING THOUGHT
More than ever, contractors have the opportunity to act as stewards for their industry and make a positive impact on the built environment by prioritizing decarbonization practices and procuring low-carbon materials.
It’s helpful to examine our current construction practices, making a note of those that do not put low-carbon decisions at the forefront to understand how the industry can make changes to impact the future positively.
About the Author:
Stacy Smedley is the executive director of Building Transparency, a nonprofit organization that provides open-access data and tools to foster a better building future and aid in reversing climate change. Building on her 20 years of experience in the architecture and construction professions, Smedley is keenly focused on the continuous development and refinement of the resources, education, and technological advancements needed to drive decarbonization strategies and investment in green procurement. She leads a growing team of experts driven to execute on the nonprofit’s mission with speed, quality, and efficiency.
Modern Contractor Solutions, May 2023
Did you enjoy this article?
Subscribe to the FREE Digital Edition of Modern Contractor Solutions magazine.
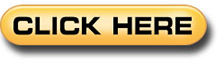