By Larry Trojak
The one common tie that seems to bind avid GNSS users is the abundant number of ways they find to put the technology to use. Companies now regularly use it for everything from material volume verification to recording the sag in power lines. Jobsites without a GNSS presence are becoming increasingly rare, while those on which the technology is playing multiple roles are more and more commonplace. For site development contractor, The Briar Team, a recent 800-acre home site development project on Daytona Beach’s LPGA Corridor became a literal GNSS showcase as the company-built roads, pads, retention ponds, and more for the 1,200-home “full-life community.” According to Briar officials, GNSS solutions helped them save time, keep crew sizes down, eliminate extraneous work, and streamline the workflow in almost every facet of the job. Since Briar considers technology a part of the everyday work picture for them, this truly was a “Team” effort.
AT HOME IN HOMES
Established more than 40 years ago by Fred and Eloise Good, Briar Construction and Paving, as it was known then, focused on construction of small commercial buildings and tennis courts. The company grew steadily and in 1984, was purchased by their son, Michael, and renamed The Briar Team. Today, the organization that started out so modestly has grown in both size and stature. Headed up by third generation family member Bobby Lee Good, The Briar Team employs more than 200 and has evolved into one of the region’s go-to site development companies. With area growth at a breakneck pace, the company has tackled some impressive projects, one of the most recent of which was the Homes at Mosaic project for ICI Homes mentioned above.
“The entire site is roughly 500 acres in size and we were doing two phases that were about 80 to 90 acres apiece,” says Tony Camacho, Briar’s senior survey crew chief. “In just those two phases, we moved more than 1.2 million yards of soil onsite. In addition to clearing, we did all the utilities, storm, sewer, water, reuse, we built at least ten different roads, poured all the curb, built the lot pads—it was total site development in every sense of the word.”
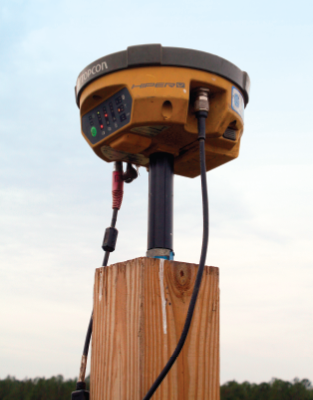
CHANGE IN ATTITUDE
Five years ago, a project workload of that size and complexity would have presented any number of challenges to The Briar Group. Most significant of those would have been the massive amounts of staking needed for the initial clearing and grading, for the curbs and roads, for each of the five ponds, and then for each house pad. Not so today.
Seeing the changes taking place with regard to GPS, machine control, and the like, roughly 4 years ago, The Briar Team, began what would be an ongoing relationship with GNSS technology. It hasn’t looked back since.
“We saw the immediate savings that could be realized in layout time alone and knew that was a route we had to take,” says Camacho. “Our projects are generally all mid-sized and larger—rarely anything smaller than 50 acres—so layout has always been a headache. Knowing that we could do jobs like this with few if any stakes, was exactly what we were looking for.”
AT A CROSSROAD
Working through geopositioning equipment specialists The Lengemann Corporation, The Briar Team made its move into GNSS-based machine control and, in doing so, arrived at a metaphorical place that today is known as “The Intersection of Infrastructure and Technology.” Here, at this conceptual crossroads, Topcon Positioning Systems provides industry professionals with the expertise to be at the forefront of technological innovation and reap the benefits via increased productivity and profitability. And, The Briar Team had those benefits on full display at the Mosaic project.
“We use GPS for a lot of different things, and at the Mosaic site we used it right out of the gate to set silt fence,” says Camacho. “Doing so with GPS is fairly uncommon, because we are generally dealing with wooded areas which can affect the instrument’s signal. But this site was wide open, and the silt fence line ran roughly 30 feet off the woods, so we had no problems.”
To illustrate how impactful that move was, he says that Colin Stiger, one of their survey party chiefs, staked about 6,000 feet of fence in one day, an effort that, done conventionally, would have involved a lot of calculations, turning, and traversing. “It also probably would have taken a three-man crew 9 hours to get what he did by himself in 6,” he said. “That, alone, was a nice savings.”
THE DIRT ON IT
Silt fence aside, the real impact the GNSS solution has had on Briar’s operation can be found in the production they get from their dozers in earthmoving and grading applications. According to Dan LaFlamme, the company’s equipment superintendent, those benefits extended to all facets of the job, from mass excavation, to pond construction, to the house pads themselves.
“At one point, we had as many as five John Deere Model 700K dozers onsite at one time—each running a Topcon 3D-MC system,” he says. “To get started each day, we would simply upload a file and our operators immediately started grading. Some of the retention ponds at the Mosaic site were 5 to 6 acres in size, which, to get top of slope, slope break, and toe, would have meant an easy 2 days of layout on each structure. With the dozers, not only is it all there on the model, we’ve noticed that we get much cleaner slopes using machine control. Having a stake at the top and the bottom increases the chance of the operator leaving a ‘belly’ in the slope; with GPS, the slope is nice and clean.”
While there was some initial apprehension on the part of some of The Briar Group’s operators about implementing GNSS technology, those attitudes have largely been replaced by an overwhelming sense of acceptance.
“Not only have they accepted it, most of our dozer guys freak out when they have to wait for updates to the file,” says LaFlamme. “Steve Terry from Lengemann warned us about this happening and he was right—they just can’t live without it now.”
NO LOAD LEFT BEHIND
At the heart of the Mosaic development, of course, were the 1,200 house pads that needed to be constructed and Comacho says they’ve realized benefits from using the GNSS solution there as well.
“We get much cleaner pads, there’s no doubt about it,” he says. “If we came out here and put five stakes on a lot pad: two in front, two in back and one in the middle, even the best dozer operator is either going to leave a bit of extra dirt on that pad or cut too much. With the Topcon system, our estimating department is getting precisely what they’ve bid.”
He adds that, were they to leave a quarter of a load on every lot pad, a project with 1,200 lots represents a good deal of material left behind. “This makes for a much more accurate product which directly impacts the bottom line.”
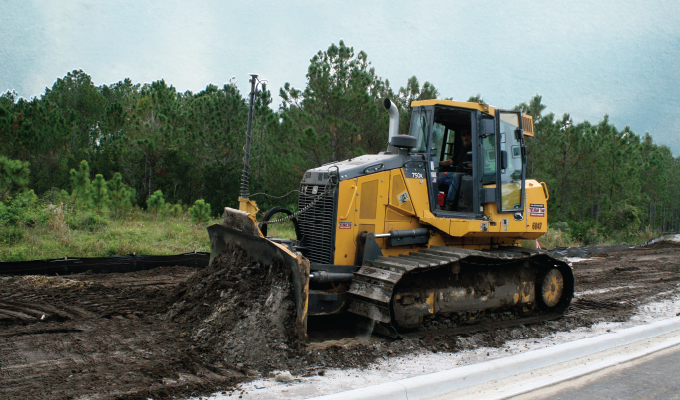
ROWS AND ROADS
Because the development’s curbs were already in place, The Briar Team took a somewhat lower-tech—but nevertheless effective—approach: using Topcon Grader System Five to grade the 10+ roads onsite. According to grader operator Sean Cote, using that system for slope control made grading both roads and right of way (ROW) a breeze.
“This system uses a Topcon Sonic Tracker to send a beam of light down to the curb indicating the blade position and keeping it at a specific grade,” he says. “The right of way had to be sloped at 2 percent and then changed to 4 percent from the back of the ROW to the utility easement. So, I simply ran the first blade width at 2 percent and bumped it up to 4 percent for the second pass. The crown of the road to the curb was all 2 percent, so that was a snap as well. Without this system we would have had to pull string line to check grade which takes time and three people to do. Although we will still run such a check it at the very end for county inspection—that’s the only time it’s done. Otherwise I do it all myself with the cross slope and that’s a huge savings in time and manpower.”
CLOSING THOUGHT
Both LaFlamme and Comacho agree that Lengemann Corporation was a key component in their successful migration over to GNSS and has continued to be a valuable ally as they’ve moved forward. “Lengemann has always been responsive to our needs, they maintain a solid inventory of replacement parts and have a good handle on changes taking place with regard to GPS equipment,” says Comacho. “That’s important to an organization like ours.”
About the author:
Larry Trojak is president of Trojak Communications, a Minnesota-based marketing communications firm. He has written for the construction, recycling, demolition, scrap, and aggregate processing industries.
Modern Contractor Solutions, September 2020
Did you enjoy this article?
Subscribe to the FREE Digital Edition of Modern Contractor Solutions magazine.
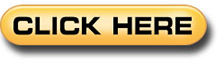