Reduce downtime with daily and weekly checks
By George MacIntyre
Today’s high-performance compact track loaders (CTLs) can provide several productivity advantages on nearly any jobsite. However, these competitive advantages can be lost if a CTL isn’t running at peak performance, and there are several things that equipment owners can do to improve productivity and extend service life.
By taking the following steps each day pre- and post-operation, equipment owners and operators can help to prevent bad things from happening before they turn into costly downtime events, and will ensure that fleet managers can address concerns in equipment health and upkeep at times throughout the day with the least impact on productivity.
FLUID LEVELS
Check fluid levels—engine and hydraulic oil, diesel and diesel exhaust fluid (DEF), and coolant. Fluids are the lifeblood of each machine and require specified levels to operate properly. A sudden drop in fluid levels may point to any number of problems with the machine that require immediate attention (blown hoses, leaking filter, etc.). Using OEM-spec engine oils helps to ensure that a machine will operate as efficiently as possible throughout its lifetime.
ENGINE COMPARTMENT
Clear any accumulated debris from around the radiator and other engine components. The engine is made of moving parts and belts that generate heat and friction—and systems designed to cool the engine compartment require room to breathe. It’s important to check and remove any clutter or material from the jobsite that may have found its way into the engine compartment.
FILTERS
Check the fuel, oil, air and other filters for signs of damage or leaking. Filters are often a quick and easy item to replace—and operating with properly working filters can prevent any number of problems with the machine.
Today’s machines are engineered to the highest performance standards—each machine is a highly engineered system of complex working parts, which should be maintained by only using genuine filters and lubricants to ensure continued optimal performance. Using non-OEM-specified filters creates a weak link in the system, and can compromise the performance of a machine.
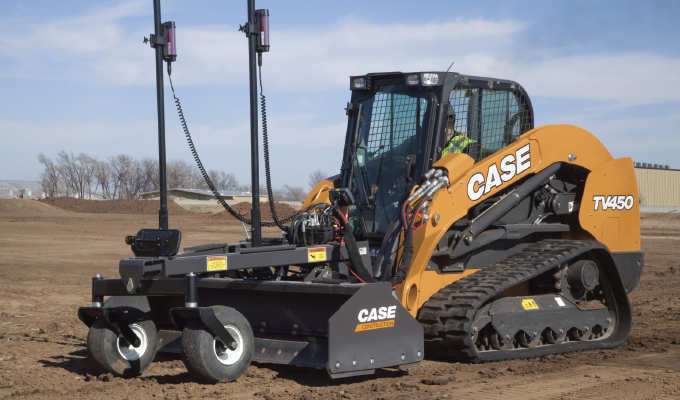
BELTS
Check belts (alternator, fan, etc.). A worn and frayed belt is another wear item that is relatively easy to replace. If noticed before it fails, then the operator can communicate with the maintenance team to replace during scheduled downtime or the next PM to ensure it doesn’t create unplanned downtime during the course of the work day.
GREASE POINTS
Identify greasing points and frequency. Every machine and every OEM are different—and keeping the machine properly greased is critical considering the power and friction created by these giant pieces of steel working together. It can also help keep out moisture and abrasive materials from the jobsite that can work into joints and friction points if not properly greased.
CHECK FOR LEAKS
Check for leaking or pooled fluid around and under the machine. This is an easy indicator that something isn’t right, and the source of that fluid should be identified and addressed/fixed before operation, and those fluids should be replaced.
HYDRAULICS
Check auxiliary hydraulic connections and pressure. Simply check the integrity of the coupling structure and that it hasn’t been damaged. Newer equipment often includes pressure relieving quick disconnects—take the time to relieve the pressure when disconnecting attachments.
STRUCTURAL DAMAGE
Check for new signs of structural damage, scratches, or dents on the machine. This is almost more important post-operation than it is pre-operation. Once done for the day, noticing and identifying any damage to the machine ensures that needed repairs are made before the next shift starts, and also allows the operator to identify how that damage occurred. Is there another structure on site that the machine came into contact with? Is there damage elsewhere on site that needs to be addressed? Similarly, if damage is noticed before a shift starts, and it was not there when the operator inspected it the day before, that pinpoints that something happened overnight or that there was possible unauthorized use of the machine.
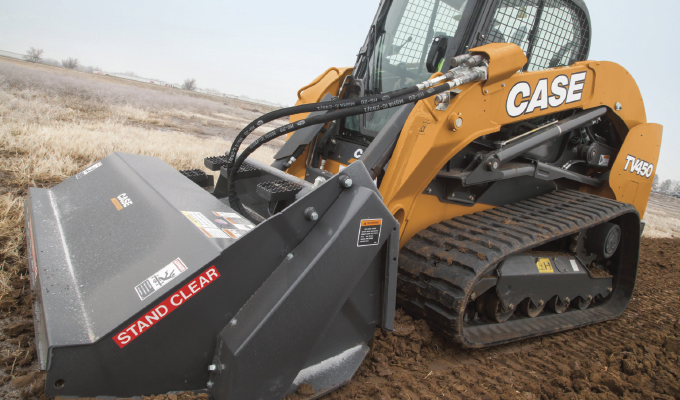
ATTACHMENTS
Check for damage on ground engaging tools (buckets, teeth, etc.). A machine’s performance is affected greatly by the efficiency of how its working tools engage with the material it is digging into and moving. Worn or broken buckets and teeth lead to inefficient operation, greater fuel use, and greater wear and tear to the machine as a whole. Identifying and addressing these elements of the machine before they become problematic will make the operator more productive and efficient.
INSIDE THE CAB
Inspect the operator compartment and clear away any debris or obstructions. Check and set mirrors. This might seem obvious, but visibility is critical to jobsite awareness, safety, and productivity. Start the engine and review console indicators and warnings. Today’s machines are built to give the operator more feedback on the workings of internal systems than ever previously available. Take note of any flashing symbols or warning lights, check the owner’s manual and consult with maintenance staff prior to operation. If equipped, check the rearview camera to ensure it’s working properly. Finally, review all external surroundings from the cab. Know your worksite, and the people and structures that exist inside your working envelope. This will ensure optimal jobsite safety and productivity.
CLOSING THOUGHT
The overall health and longevity of a machine often comes down to daily and weekly maintenance procedures. The operator and other jobsite personnel are often the first line of defense against costly equipment downtime, so it is critical for owners and operators to follow maintenance best practices to ensure that their CTLs contribute to a safe and productive operation, and a strong bottom line.
About the author
George MacIntyre is a product director, skid steers and compact track loaders, with CASE Construction Equipment. For more information, visit www.casece.com.
Modern Contractor Solutions, August 2019
Did you enjoy this article?
Subscribe to the FREE Digital Edition of Modern Contractor Solutions magazine.
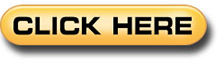