The requirement for employers to evaluate their operators was first introduced in the 2010 Cranes and Derricks in Construction rule, and was set to expire when the certification requirement came into effect in 2014. However, OSHA decided to extend the requirement, making it permanent in the 2018 revised rule, Cranes and Derricks in Construction: Operator training, certification, and evaluation.
For the first time, crane operator qualification was identified as a three-step process. Operators must be 1) trained, 2) certified, and 3) evaluated in order to be qualified to operate equipment. Certification provides an independent assessment of the baseline knowledge and skills of an operator, and acknowledges the individual’s ability to operate general types of cranes. Evaluations, however, are necessary to ensure that the operator is competent, and can safely operate a specific piece of equipment.
In the Preamble of the 2018 Final Rule, OSHA states that the reason behind this decision was because crane operator certification alone does not guarantee that an operator has acceptable knowledge and skill to safely use all equipment in a variety of circumstances.
CONDUCTING EVALUATIONS
Evaluations can be done by a third-party company or by the employer. If the evaluations are done in-house, the evaluator is required to be an employee or agent of the employer. However, the evaluation is conducted, it must be done by someone who has the “knowledge, training, and experience necessary” to assess equipment operators.
Many crane operators are hired as subcontractors and frequently transition from jobsite to jobsite. That does not allow employers to use evaluations from previous employers. Because weather conditions, crane type, and the type of work being performed changes from jobsite to jobsite, it is critical that employers ensure new operators are evaluated. Operators need to have the ability to perform tasks that are unique to the worksite.
When conducting evaluations, it is the evaluator’s responsibility to ensure the operator has the necessary skills and knowledge needed for the crane they plan to operate, its safety devices and operator aids, the type of work the crane is able to perform, and that the operator is able to recognize and avert risk.
Mot importantly, the evaluation must take into account the type and configuration of the crane that will be used, including the work the operator needs to perform. The evaluation must also cover the operator’s ability to perform the hoisting activities required for the work they are assigned, such as blind lifts, personnel hoisting, and multi-crane lifts.
Once an operator is successfully evaluated an employer may allow the operator to run other equipment that does not require a substantially different skillset. That call is the responsibility of the employer.
RECORDKEEPING
It is important to note that a new evaluation must be done and documented when the operation of a crane requires a level of operating skills, knowledge, or abilities that is significantly different from the crane that operator was originally evaluated on.
The 2018 rule also included additional documentation requirement for evaluations. Employers must maintain evaluation documents on-site for the entire duration the operator is employed. While there is no official template for evaluation documents that an employer must use, there is standard information it must contain.
The employer’s evaluation documentation must include, at a minimum:
- Operator’s name
- Evaluator’s name and signature
- Date of evaluation
- Make, model, and configuration of equipment used in the evaluation
CLOSING THOUGHT
In early drafts of the 2018 revision, OSHA explored the need for operators to be re-evaluated every year. However, the language was revised in the Final Rule. Under OSHA 1926.1427 (f)(7), employers are required to re-evaluate an operator whenever the employer is required to retrain the operator.
1926.1427 (b)(5) outlines a few scenarios that would trigger the need for retraining. This section includes, but is not limited to, feedback from an onsite supervisor or safety manager, contractor, or other person that the operator was operating equipment unsafely, OSHA citations, a crane near miss, or other incidents that indicate unsafe operation of the crane.
In these instances, the employer must retrain and re-evaluate the operator. The re-evaluation must include the lack of skills, knowledge, or ability to recognize and avert the risk that triggered the retraining.
For More Information:
Crane Industry Services, LLC provides safety and operation training, inspections and consulting. For more, visit centeredonsafety.com.
Modern Contractor Solutions, April 2022
Did you enjoy this article?
Subscribe to the FREE Digital Edition of Modern Contractor Solutions magazine.
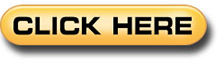