The construction industry continues to be buffeted by challenges, both longstanding and developing. Many builders are still struggling to find enough skilled labor, with the Bureau of Labor Statistics reporting in November 2023 that there were 459,000 job openings across the construction industry. At the same time, construction supply chains remain impacted by disruptions and cost pressures, while sustainability needs are growing with 2030 benchmark deadlines looming.
One increasingly popular building methodology, offsite construction, can help construction firms address these challenges. Last year, Maximize Market Research estimated the offsite construction market is expected to grow at a 5.8 percent compound annual growth rate from 2022 to 2029 to reach $369.72 billion.
This approach, in which components are manufactured remotely and then delivered to the construction site for assembly, offers several benefits. Project timelines can be reduced, and safety improved. In addition, offsite construction can eliminate some of the waste associated with building, and jobsite labor needs can be also reduced. Proponents also see quality gains as well as minimized disruption to areas surrounding worksites.
However, for the efficiency gains to be realized, it’s critical that schedules be synchronized across all teams, including offsite fabrication facilities.
SUSTAINABLE, EFFICIENT WAY TO BUILD
There are different forms of offsite construction. Each of them is slightly different and achieves slightly different ends.
“Minimal offsite or kitting,” when the materials needed for a particular scope of work are palletized and shipped to the jobsite, is the least divergent from the traditional construction model.
When components such as entire sections of walls or rooms, with electrical outlets and plumbing hook-ups included, are sent to the construction site for incorporation in the final product, it’s known as “mid-level offsite.”
Finally, “complex offsite” involves larger portions of a structure being prefabricated offsite and assembled into a truly modular building on site.
Because only the precise amount of materials needed for a given project will be used, each level of offsite construction helps reduce waste on projects. Further, because of the repetitive nature of offsite construction, quality can be better monitored with fewer skilled workers required to be on site.
However, offsite construction methods also add complexity to a project, as the master schedule needs to be coordinated with an offsite fabrication schedule. In addition, offsite production forecasts need to be coordinated with supply chain lead times to ensure the proper inventory is maintained.
COORDINATION
For offsite construction to really be a more sustainable and efficient way to build, the offsite and jobsite construction teams need the right processes in place to coordinate the demand of the construction components, keep track of the various shipments arriving to the build site, and predict any major supply chain setbacks that could present a problem down the line.
Teams looking to utilize offsite construction should adopt a modern project portfolio-management and scheduling solution that can address the complexities of offsite construction. The right management system will help teams maximize the added efficiency of the approach and keep them in constant contact with the third parties that are fabricating components. An open and robust scheduling tool enables the automated bidirectional linkage between project master schedule and offsite/factory production schedules. This type of platform helps ensure the offsite and jobsite teams remain in sync, even when they face unexpected scheduling changes.
Additionally, a reliable project-management solution should improve collaboration between the teams for better quality control of offsite-manufactured assemblies, helping to track the status of production orders and ensure quality before assemblies arrive on a jobsite.
If one of the prefabricated pieces needed to complete construction is being delayed at the source or is facing shipment difficulties due to severe weather, advanced project-management software would instantly send a notification and cross-examine the project plan to identify related scheduling issues.
OPTIMIZED SUPPLY CHAIN SUPPORT
Teams can use technology to monitor supply chains to best manage the efficient procurement of materials, ensuring the manufacturing process is not delayed.
To accomplish this, production managers must establish strong relationships with reliable suppliers. Then, with a holistic management platform, production managers can forecast inventory demand, reduce the likelihood of untimely deliveries, and implement strategies to mitigate supply chain risks.
Offsite construction can be a powerful way to the many challenges confronting projects. It offers enhanced standardization to both project-management processes and with the modular components that can contribute to efficiency, consistency, and a smoother flow within construction projects. With the right project-management solution to help teams navigate the many moving parts and potential supply chain disruptions, offsite construction can help turn a complex web of deliveries into a navigable set of to-dos.
About the Author:
Frank Malangone is executive director, industry strategy and innovation, for Oracle Construction and Engineering. For more, visit www.oracle.com/construction-engineering.
Modern Contractor Solutions, March 2024
Did you enjoy this article?
Subscribe to the FREE Digital Edition of Modern Contractor Solutions magazine.
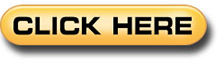