By Troy Dahlin
The construction industry is undergoing a digital revolution, and new approaches are improving traditional tools and processes. With this comes the opportunity for contractors to adopt easy-to-implement technology to elevate their work to deliver projects on time, to specification, and within budget.
Solutions such as machine control are more accessible than ever before, and deploying them to existing teams is a lot easier, and less time-consuming, than even a few years ago.
Machine control can reduce costs and empower teams to execute at a higher experience level. Contractors and builders are taking notice and responding accordingly.
According to The Civil Quarterly (TCQ), a new publication launched in July 2020 by Dodge Data & Analytics, 47 percent of contractors use machine control, while even more are looking to move in that direction. Of the contractors that use machine control, they use it on the majority (61 percent) of their projects.
In the wake of COVID-19, machine control has again proven its worth on the jobsite. A more recent poll from The Civil Quarterly revealed nearly one in three (32%) contractors cite machine control as one of the most widely adopted new technologies helping them minimize negative business impacts amid the COVID-19 pandemic.
While larger companies tend to use machine control two-to-three times more frequently than smaller operations, more and more it’s the smaller companies that are adopting these digital solutions to grow their business and effectively compete.
“Machine control in this day and age is really the only way to go in construction, especially when you start factoring in different efficiencies,” says Jacob Daniel, GPS data manager at construction company, RV Associates. “It almost wouldn’t be possible for a company our size to do a large jobsite without spending thousands of dollars in hubs and stakes.”
MOVE MATERIALS ONCE
Besides labor and equipment, materials pose the most significant potential for added cost on most projects. Contractors have one chance to do it right or risk racking up potentially high costs to correct avoidable mistakes.
Machine control essentially enables a one-and-done approach, eliminating the guesswork, and ensuring work is performed correctly.
Plus, it eliminates the need to hire surveyors to verify work against the site’s plans, and empowers contractors to correctly place materials to grade the first time. The real benefit of this technology is that it can potentially reduce a job’s cost by 30-to-50 percent.
“NO” EXPERIENCE NEEDED
When technology is easy to deploy, and intuitive for both novice and experienced operators to use, it’s not surprising to see a rising trend in adoption. Such solutions enable any team member to effectively contribute, perhaps as much as the most tenured team member.
Manufacturers are making it easier to adopt a single solution for use with mixed fleets, and operators can use a single panels for multiple machine types.
Solutions like the iCON GPS rover release the limitations of working with the pole in vertical positions and increases productivity over conventional methods. Additionally, the offering collects as-built field data and stakes out designs faster, while ensuring accuracy to minimize errors.
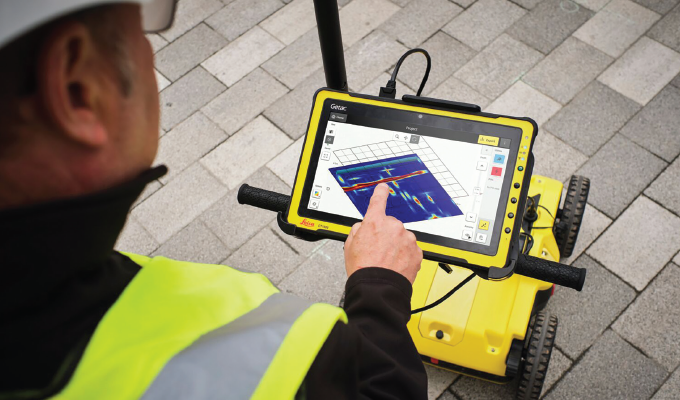
ON-TIME, ON-SPEC, WITHIN BUDGET
Easy-to-use solutions, like 3D machine control, are ideal for teams that need real-time jobsite intelligence, as they communicate between the field and the office. Not long ago, design changes required someone to drive the updated details from the office to the site, a potentially time-consuming prospect.
Because machine control solutions work with Leica ConX, a cloud-enabled solution, companies can manage, monitor, and share jobsite data in real-time from anywhere. Using the most up-to-date plans reduces the likelihood of errors and the need to redo work, thereby reducing the costs of mistakes.
Machine control also allows contractors to mitigate problems stemming from the ongoing labor shortage and reduce overall time on the jobsite by 25 percent. The savings snowball and extend beyond labor to include lower fuel costs and savings resulting from lower wear and tear on machines.
JUST THE START
Organizations need easy-to-understand and deploy tools that empower them to work smarter and more efficiently, while not putting their teams at risk, or sacrificing quality. Because it seamlessly and rapidly harmonizes and simplifies data handling, machine control reduces downtime, enabling higher utilization.
Machine control complements other solutions currently employed on the jobsite, such as underground utility detection, to further reduce costs stemming from mistakes.
Underground utilities pose a significant risk to projects, and stopping work for a utility strike can cost companies thousands of dollars. In 2018, workers reported more than 330,000 underground utility strikes in the United States and more than 11,000 in Canada, an increase of more than 13% since 2015.
Technology is a professional partner that complements existing team members’ efforts, allowing them to accomplish more without complex additions.
CLOSING THOUGHT
Today’s jobsite is full of potential pitfalls and is challenging enough without introducing additional ones. While contractors are accustomed to finding solutions to unexpected challenges, machine control is another tool they can use alongside their other proven options.
About the author:
Troy Dahlin is vice president, heavy construction segment, US/CAN of Leica Geosystems, part of Hexagon. Information based on data from the most recent issue of The Civil Quarterly from Dodge. For more, visit leica-geosystems.com.
Modern Contractor Solutions, November 2020
Did you enjoy this article?
Subscribe to the FREE Digital Edition of Modern Contractor Solutions magazine.
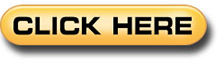